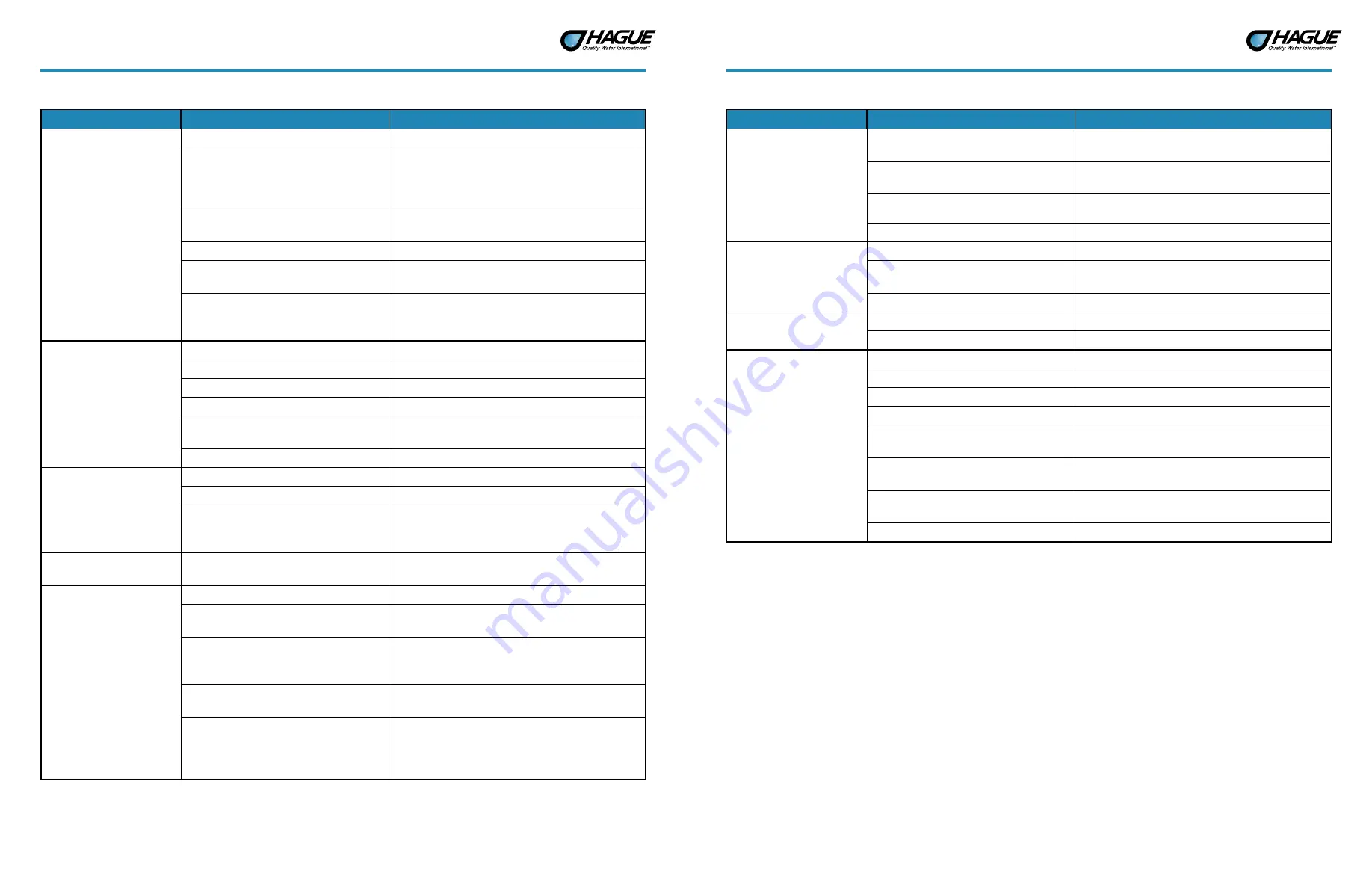
38
39
Troubleshooting
Problem
Possible Cause
Solution
No soft water after
regeneration
No salt in brine cabinet
Add salt
Sediment in brine cabinet has plugged the
brine line and air check/draw tube
Remove the brine line and flush clean
Remove the air check/draw tube and flush with clean
water. Clean injector assembly. Clean any sediment
from brine cabinet
Flow control is plugged
Remove brine piston housing and clear debris from the
flow control
Drain line is pinched, frozen, or restricted
Straighten, thaw, or unclog the drain line
Clogged injector assembly
Remove injector cap and clean nozzle and throat with
a wooden toothpick. Replace throat if removed
Salt bridge has formed due to high humidity
or the wrong kind of salt
Test with a blunt object like a broom handle. Push the
handle into the salt to dislodge the salt bridge, or use
hot water around the inside perimeter to loosen salt
No soft water
The bypass valve is in the Bypass position
Place the bypass valve in the Service position
Appliance is plumbed backward
Check that appliance is plumbed correctly
Extended power outage
Reset the time of day
Water hardness has increased
Re-test the water and re-enter a new setting number
Not metering water
Flow should be indicated with water usage. If no flow,
see below
Blending dial is open
Make sure blending dial is closed
No flow is indicated when
water is flowing
The bypass valve is in the Bypass position
Place the bypass valve in the Service position
Appliance is plumbed backward
Check that appliance is plumbed correctly
Sensor not receiving signal from magnet on
turbine
Remove sensor from bypass housing. Test with
magnet on either flat side of sensor. If flow is indicated,
check turbine. If no flow, replace sensor
Flow indicated when water
is not being used
The household plumbing system has a leak Repair the leak
No read-out in display
Electric cord is unplugged
Plug in the transformer
No electric power at outlet
Check power source. Make sure outlet is not controlled
by a switch
Defective transformer
Test with volt meter for 12 VAC at control. If less
than 10 VAC or greater than 14 VAC, replace the
transformer
Defective circuit board
With 12 VAC present at controller, replace the
controller
High ambient room temperature. If the
temperature exceeds 120°F (49°C), the
display will blank out. This does not affect
the operation of the controller
No action necessary
Troubleshooting
Problem
Possible Cause
Solution
Appliance stays in
regeneration
Controller not attached properly
Make sure the controller is pushed all the way onto the
drive end cap
Defective magnet disk
Replace magnet disk
Foreign object in main control valve
Remove foreign object(s) from the main control valve
Broken valve assembly. Motor running
Repair the drive end cap
Excess water in brine tank
Restricted, frozen, or pinched drain line
Remove restriction, thaw, or straighten drain line
Plugged brine line, brine line flow control, or
air check/draw tube
Clean flow control, air check/draw tube, and brine line.
Clean any sediment from the brine cabinet
Plugged injector assembly
Clean or replace injector. Replace throat if removed
Not regenerating in proper
sequence
Magnet disk defective
Replace magnet disk
Defective controller
Replace controller
Salty water (pink water
from iron filter)
Plugged injector
Replace injector screen, nozzle, and throat
Low water pressure
Maintain minimum pressure of 20 psi (1.4 bar)
Drain line or flow control is restricted
Remove restriction
Brine line restricted or crimped
Remove restriction, replace if crimped
Excessive amount of water in brine cabinet Verify correct water level relative to salt setting. Check
brine line and fittings for loose connections
Insufficient rinse time
Check mode setting chart for proper brine rinse time.
Adjust time, if necessary
Intermittent pressure drop from feed source Install check valve on the inlet water line to the
appliance (Check local plumbing codes first)
Brine valve drips water back to brine tank
Clean brine valve housing, replace piston assembly