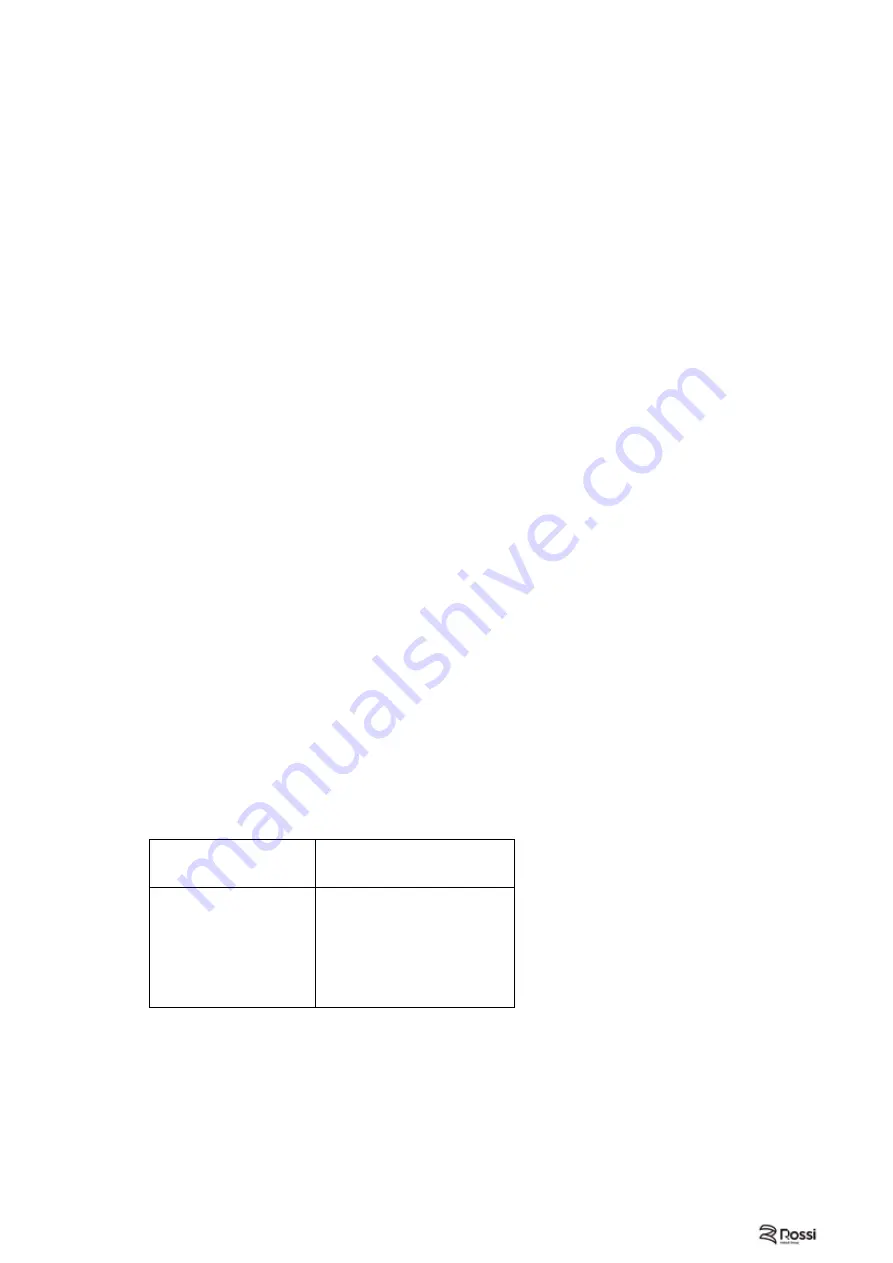
55
UTD.123.2019-10.00_EN
Sizes
81 (A, E, G series) and
021A (EP series) are
lubricated for life
, assuming external pollution-
free environment. An overall guide to oil-change interval is given in the table, and assumes pollution-free
surroundings. Where heavy overloads are present, halve the values. Apart from running hours replace or
regenerate synthetic oil at least each 5 years.
8.3 - Lubrication of extruder support (helical and bevel helical, sizes 100 ... 4501
)
The lubrication of extruder support, supplied
WITHOUT OIL
like the gear reducer, is oil bathed and can be
joint or separate compared with the gear reducer's one.
Separate lubrication
1)
The gear reducer must be filled with lubricant with ISO viscosity degree stated in table 8.2b, whereas the
extruder support
– equipped with metallic plug with filter and valve, drain and level – must be filled with
polyalfaolefines basis synthetic oil
with viscosity degree ISO
320 cSt
8.2.d, AGIP Blasia SX, MOBIL SHC
Gear, KLÜBER Klübersynth GEM4, ARAL Degol PAS, BP Enersyn EPX, SHELL Omala S4 WE; approx quantities
see table 8.3.1) and up to level stated on
extruder support
.
Common/Joint lubrication
2)
The
gear reducer
and the
support
must be filled with the same
polialfaolefines basis synthetic oil
, with
iSO viscosity degree stated in table 8.2b and up to
level
stated on the
gear reducer
. For mounting position
B6, during the filling, remove the upper plug positioned on the extruder support in order to facilitate the
air flow from inside. In this circumstance, cause of the elimination of potential residual air, an oil filling up
to level could be necessary.
1)
The inner part of gear reducer is separated from the
extruder support through a seal ring.
2)
The inner part of gear reducer is connected with the
extruder support; the common lubrication is present
on gear reducer and gearmotors 2I sizes 100 ... 360
or in presence of independent cooling unit when it is
used both for gear reducer and extruder support.
Gear red.
size
Approximate
oil quantity extruder support
l
140, 160
0.8
180
1.1
200
1.5
225
2.5
250, 280
4
320 ... 360
9.1
4000, 4001
20
4500, 4501
16
Grease-lubricated bearings:
Lubrication is «for life» assuming uniform load and pollution-free environment. Replace the grease every
year with running up to 12 h/d and every 6 months with running of 12
÷
24 h/d; in these occasions re-
lubricate the
backstop device
with grease SHELL Alvania RL2. Bearing should be filled with ESSO Gadus
S2 V100 bearing-grease for ball bearings, KLÜBER STABURAGS NBU 8 EP for roller bearings.
Attention!
for bearings requiring greasing refero to ch. 15 ... 20 and consult Rossi in case of doubt.
Combined gear reducers.
Lubrication remains independent, thus data relative to each single gear reducer
hold good.
Output bearings for slewing drives
(
EP series Slewing drives
)
In the case of slewing drives (output designs R-S-H), regardless of the mounting position, the output bearing
has an independent grease lubrication.
The re-lubrication of the bearing has to be carried out at each oil change.
For maintenance intervals
and grease quantity, refer to relevant table 8.2e
It is recommended to re-lubricate bearings and seals with the same grease the gear reducer was supplied;
as alternative, it is possible to use similar grease types.
ATTENTION: the re-lubrication procedure may cause a grease leakage from bearing seat to oil chamber.
This does not affact gear reducer operation. However it is recommended to re-lubricate before replacing
gear reducer oil, in order to remove any grease leaked into oil chamber. For grease quantities follow the data
contained in table 19.1 on page 93.
Table 8.3.1
Содержание Rossi A Series
Страница 1: ...A E G H EP series ATEX Operating Instructions ...
Страница 7: ...7 UTD 123 2019 10 00_EN This page is intentionally left blank ...
Страница 118: ...118 UTD 123 2019 10 00_EN ...
Страница 119: ...119 UTD 123 2019 10 00_EN ...