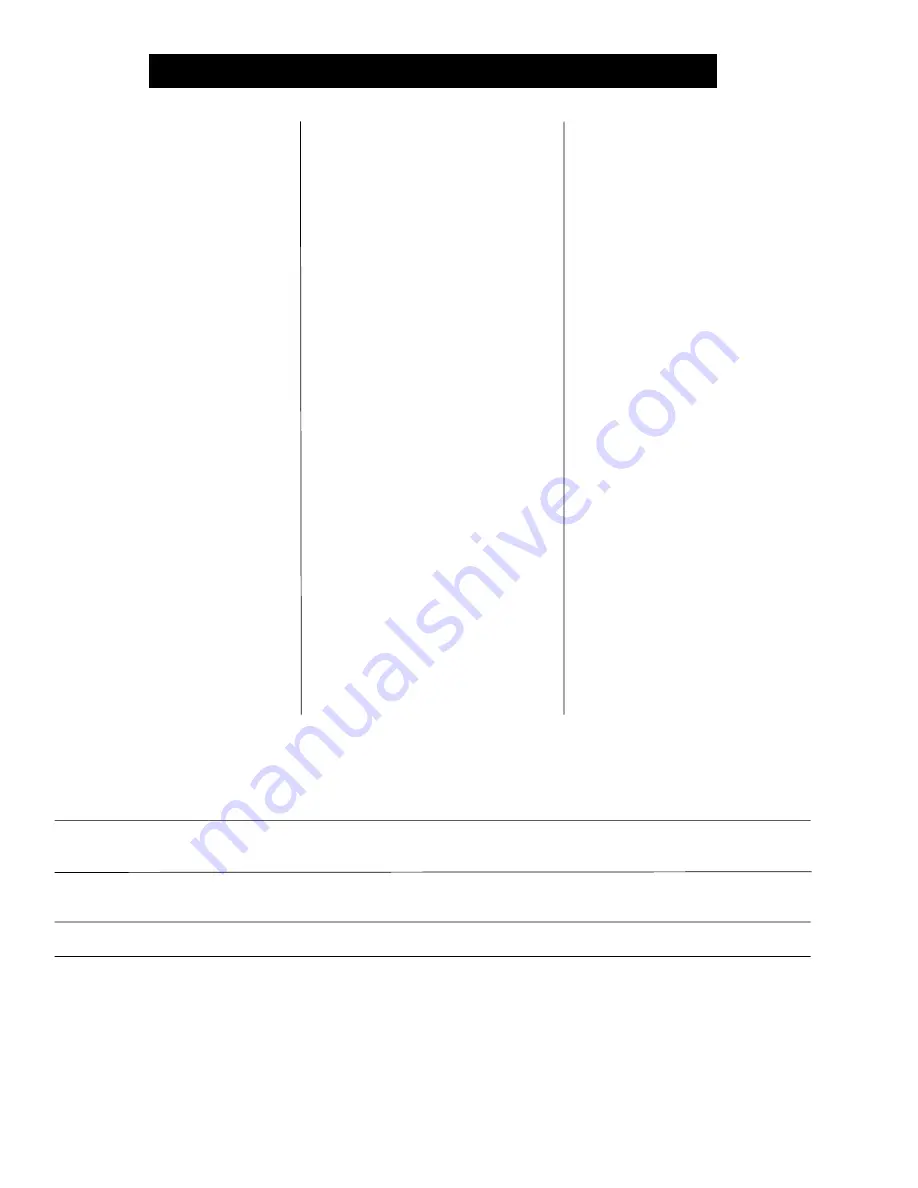
18
DRYER START UP
STAGED BATCH
OPERATION
1.
Turn the control power switch to on.
2.
Make sure the drying mode
switch is turned to staged batch.
3.
Open the main fuel supply valve
on the tank if using LP gas, or
the valve in the fuel supply line
if using natural gas. Turn on the
electric shut off, Maxon valve
(if so equipped), or open the
manual shut off valve to allow
fuel flow to the dryer.
4.
Set switches to the following
settings:
Load-Auto
Fan-Auto
Burner-Auto
Unload-1 speed
5.
To start the drying operation
push the dryer power start but-
8.
After purging for approxi-
mately 10 seconds the burner
will fire. For information con-
cerning burner adjustment
see the pre start section of this
manual.
9.
To properly set the correct dry,
cool and unload time for various
moisture content grains. See the
chart on page 18.
10. If the dryer is being operated in
all heat, move the fan switch
to the on position. In this posi-
tion the fan will run continu-
ously during the dry, cool and
unload stages of the staged
batch operation. If the dryer
is being operated in the dry
and cool mode, the preferred
position for the fan switch is the
on position, so the fan will run
continuously. If desired, the fan
can be turned off during the un-
ton. The controller will start all
the dryer components in their
proper order. If any of the se-
lected switches are improperly
positioned for staged batch dry-
ing, the display will indicate the
proper switch position, and will
not allow the dryer to operate
until the position of the switch is
corrected.
6.
The dryer should already be
filled with grain. And the load
auger switch is set to auto. In
both the auto and manual po-
sition, the grain level switch will
automatically keep the dryer full
of grain. In the auto position the
dryer will shut down after the
preset time period on the out of
grain timer, or if the grain flow
to the dryer is interrupted.
7.
The fan will start and airflow is
checked.
FAN & HEATER SWITCH SETTINGS
Fan Setting
Auto
Auto
On
On
Fan Function
Fans stay on during dry and cool
cycle only
Fans stay on during dry and cool
cycle only
Fans are on continuously
Fans are on continuously
Heater Function
Burners stay on during dry timer cycle
only
Burners stay on during dry and cool
Burners are on continuously
Burners shut down at the end of the
dry cycle
At the end of the dry cycle in staged batch, the fans and heaters will continue running if the moisture control is "on", until
the preset temperature on the moisture control thermostat is reached.
Heater Setting
Auto
On
On
Auto
Содержание COMPETITOR 2000 Series
Страница 2: ...2...
Страница 26: ...26 SERVICE...
Страница 34: ...34 SERVICE 100 SERIES SINGLE FAN WIRING TO CONTROL BOX...
Страница 35: ...35 SERVICE 100 SERIES FRONT PANEL EXTERNAL WIRING...
Страница 36: ...36 SERVICE 100 SERIES FRONT PANEL INTERNAL WIRING...
Страница 37: ...37 SERVICE 100 SERIES LOWER BACK PANEL COMPONENT LAYOUT...
Страница 38: ...38 100 SERIES EXTERNAL WIRING TO DRYER SERVICE...
Страница 39: ...39 100 SERIES UPPER CONTROL BOX WIRING SERVICE...
Страница 40: ...40 SERVICE 100 SERIES MAIN POWER WIRING...
Страница 41: ...41 SERVICE 100 SERIES CONTROL SCHEMATIC...
Страница 42: ...42 SERVICE 100 SERIES CONTROL SCHEMATIC...
Страница 43: ...43 SERVICE 100 SERIES CONTROL SCHEMATIC...
Страница 44: ...44 SERVICE 100 SERIES 220VOLT 1 PHASE POWER SCHEMATIC...
Страница 45: ...45 SERVICE 100 SERIES 220VAC 3PHASE POWER SCHEMATIC...
Страница 46: ...46 SERVICE 100 SERIES 440VAC 3 PHASE POWER SCHEMATIC...
Страница 52: ...52...