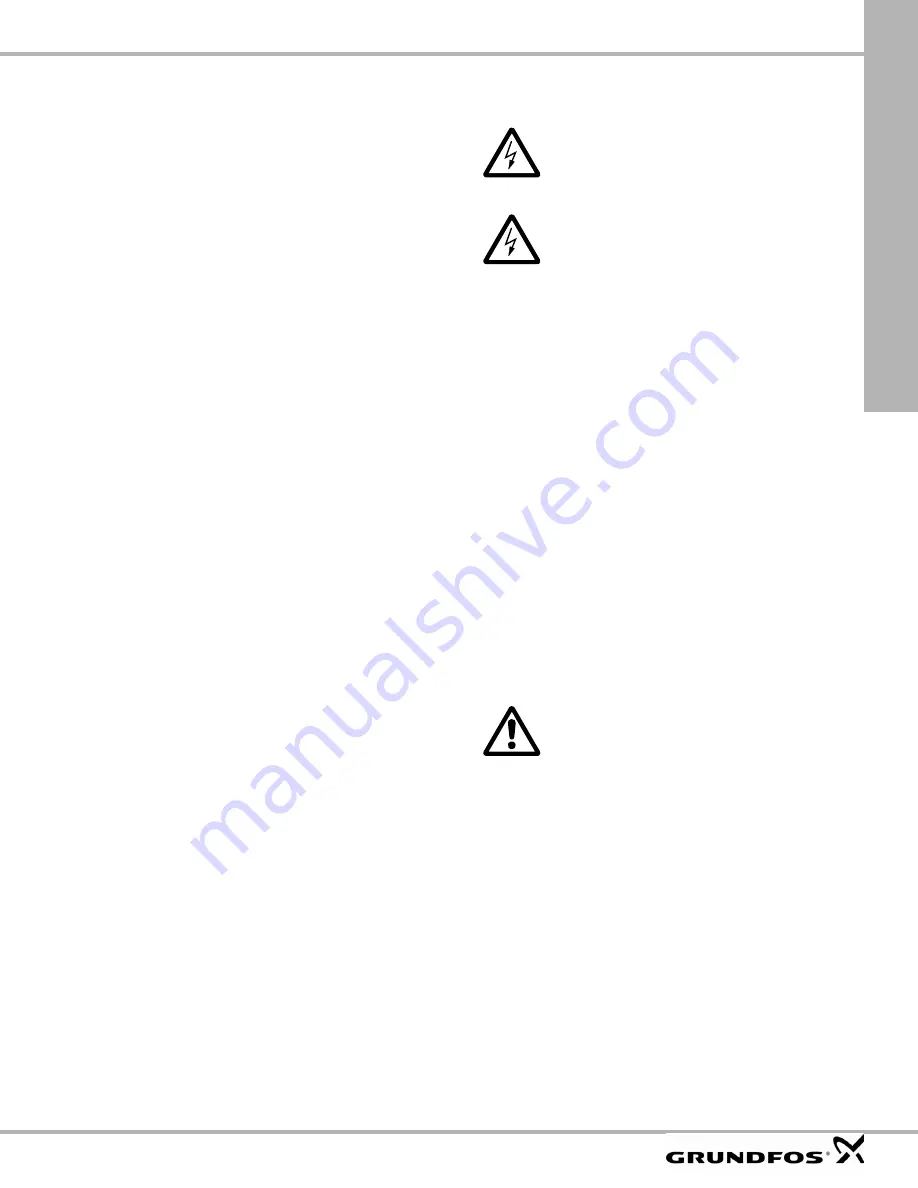
Eng
lish
(US)
8
4.14 Coupling alignment (LF)
• The following anchoring and alignment procedure is typical
and, if performed with care, should result in a smooth running,
trouble-free installation.
• If the pump and motor were shipped mounted on the pump
base as an assembly, remove the coupling guard.
• The pump and motor were accurately aligned at the factory,
but handling during shipment usually alters this pre-alignment.
Using a small straight edge and feeler gauges or a dial
indicator, check for horizontal, vertical, and angular
misalignment of the coupling hubs Fig. 5 and Fig. 6.
• Coupling alignment is correct when the dial indicator reads no
more than .005" run out in any direction (or when the straight
edge contacts both hubs evenly in both horizontal and vertical
positions). If misalignment is detected, loosen the motor and
shift or shim as necessary to re-align, then re-tighten bolts.
Always align the motor to the pump as piping strain will occur
if the pump is shifted. Never reposition pump on base!
• After final piping connections to the pump have been made,
motor wiring compared, correct rotation has been established,
and piping filled with liquid, check shaft alignment once again.
• Leave the coupling guards off until the pump priming
procedure is completed for a final shaft alignment check.
• To protect personnel from rotating machinery, Always install
coupling guards after installation is complete; before starting
pump!
4.15 Coupling alignment (LCS)
• No alignment of the pump and motor is required.
5. Installation-electrical
5.1 Motors general
the motor control circuit must have the following components in
order to comply with the National Electrical Code.
• Motor Disconnecting Device: A motor disconnecting device
must be installed that is capable of disconnecting both the
controller (motor starter) and the motor from their source of
power.
• The disconnecting device must be located so that the
controller (motor starter) can be seen from the disconnecting
means. In all cases, the distance from the disconnecting
device to the controller must be less than 50'.
• In most installations the disconnecting device will be a circuit
breaker or fusible disconnect switch.
Motor short circuit and ground fault protection:
• Short circuit and ground fault protection are usually provided
by means of a circuit breaker or fusible disconnect switch.
• The selection of the size of the circuit breaker or fuse must be
in accordance with Section 430-52 and Table 430-152 of the
National Electrical Code.
Motor controller with running over current protection (magnetic
starter):
• These components must be installed in accordance with
applicable local and state electrical codes in addition to the
National Electrical Code.
5.2 Installation wiring
• Mount the control panel or motor starter(s) in close proximity
to the pump to provide convenient control and ease of
installation.
• Wire panel or starter(s) to motor(s) and pilot device(s): Wires
to each motor must be sized for at least 125 % of the motor
nameplate full load amps. AWG #16 Type THW stranded wire
is recommended for wiring of pilot devices (float switches).
• Check incoming power source to ensure that it is the same as
the voltage and phase of the motors.
• Verify that the starters are suitable to operate the pump motors
on voltage and phase that is available.
Warning
Use only qualified electricians for electrical
installation and maintenance.
Refer to manuals provided with electrical
accessory components and disconnect power
supply as recommended for servicing.
Warning
Never do maintenance work when the unit is
connected to power.
Warning
Whenever powered equipment is being used in
explosive surroundings, the rules and
regulations generally or specifically imposed by
the relevant responsible authorities or trade
organizations must be observed.
PA
CO Pumps
11