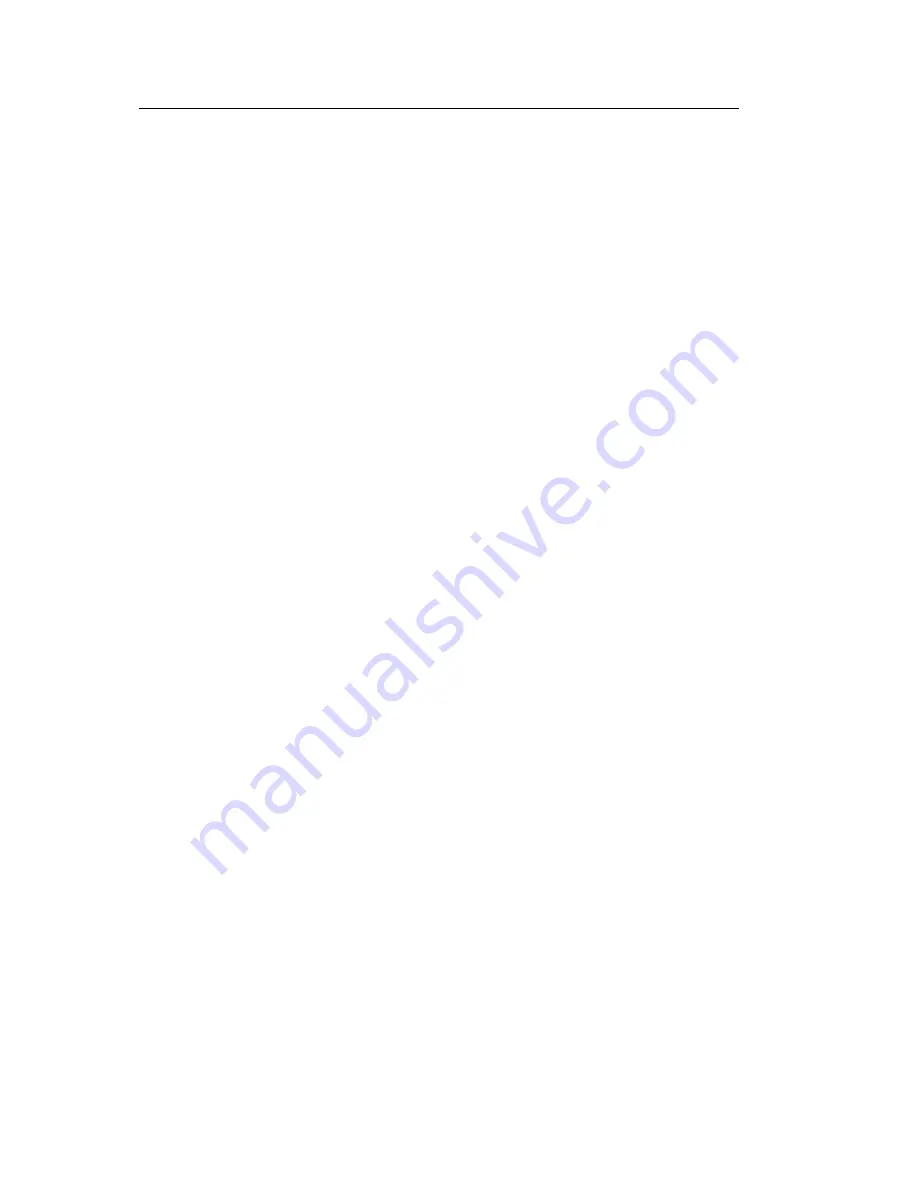
11
F600775R00
Component description
General Manual
Release date: September 2014
3.5
Safety and control features
3.5.1 Maximum pressure indicator
A relief valve (fitted with an electrical contact) is installed in the grease channel between the
plunger pump and the pump outlet. This relief valve leads the grease back to the reservoir if
the maximum grease pressure (300 bar) is exceeded during the pump phase of a grease cycle.
The grease pressure may become too high, for example, if the driver has forgotten to couple
the grease line to the respective quick coupler on the dipper arm after installing the hydraulic
hammer on the excavator.
The maximum admissible grease pressure can also be exceeded if the viscosity of the grease
is too high (due to a low ambient temperature).
3.5.2 Minimum pressure indicator
A minimum grease pressure switch is also installed in the grease channel between the plung-
er pump and the pump outlet. If the minimum grease pressure (20 bar) is not reached during
the pump cycle, the switch will signal this to the control unit. The control unit then processes
and stores this message.
3.5.3 Minimum level switch
A minimum level switch is installed in the grease reservoir. If the grease reaches its minimum
level, the switch will signal this to the control unit. The control unit will process, store and
report the occurrence of that condition.
The pump will be disabled automatically when the allowed amount of grease is finished. After
refilling the grease reservoir the pump will be enabled automatically.
3.5.4 Revolutions of pump drive shaft
As integrated sensor monitors the drive shaft rotations. When it does not sense a rotation
every 10 seconds of a pumping phase it will abort the greasing cycle.
3.5.5 Defective wiring and short-circuits
Open-loads (interruptions) in the wiring sensors, the minimum level switch, the relief valve,
the electric motor and any external signalling devices will be detected and processed and
stored by the control unit. This is also applicable to short-circuits in the wiring.
3.5.6 Hydraulic hammer
When the hydraulic hammer is controlled by the BreakAlube control unit (parameter setting),
the control unit will disable the hydraulic hammer when an error is detected that caused to
pump cycle to be unfinished.
Содержание BreakAlube-3
Страница 1: ...General Manual Automatic Greasing System BreakAlube 3 F600677R00 YOUR EFFICIENCY IS OUR CHALLENGE...
Страница 7: ...7 F600775R00 General information General Manual Release date September 2014 4 3 2 6 5 1...
Страница 34: ...BreakAlube 3 F600775R00 34 Maintenance Automatic Greasing System Release date September 2014 Notes...
Страница 35: ......