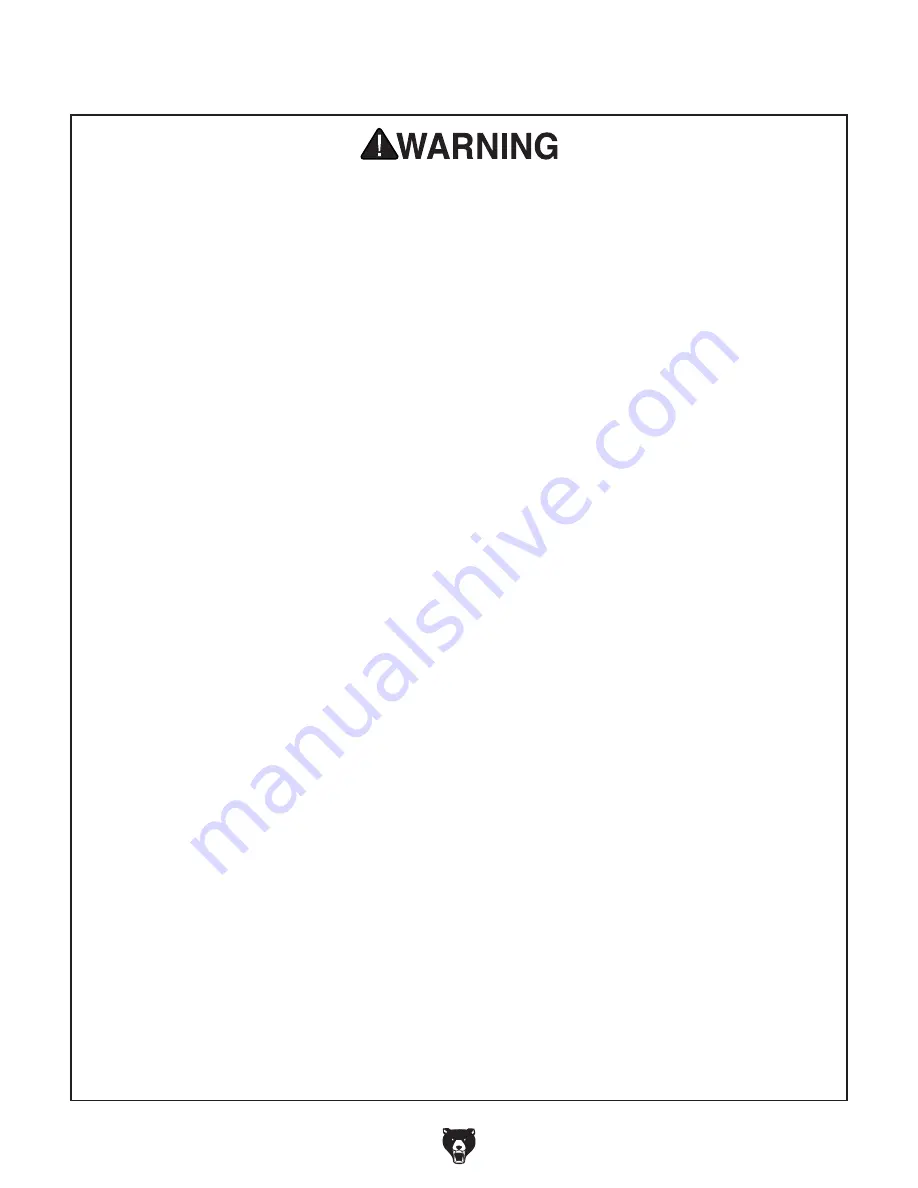
-10-
Model G0810 (Mfd. Since 10/15)
Additional Safety for Drill Presses
Serious injury or death can occur from getting clothing, jewelry, or long hair entangled in
rotating spindle or bit/cutting tool. Contact with rotating bit/cutting tool can result in severe cuts
or amputation of fingers. Flying metal chips can cause blindness or eye injuries. Broken bits/
cutting tools, unsecured workpieces, chuck keys, or other adjustment tools thrown from rotating
spindle can strike nearby operator or bystanders with deadly force. To reduce the risk of these
hazards, operator and bystanders MUST completely heed hazards and warnings below.
WORKPIECE CONTROL. An unsecured work-
piece may unexpectedly shift, spin out of control,
or be thrown if bit/cutting tool “grabs” during opera-
tion. Clamp workpiece to table or in table-mounted
vise, or brace against column to prevent rotation.
NEVER hold workpiece by hand during operation.
NEVER start machine with bit/cutting tool touching
workpiece; allow spindle to gain full speed before
drilling.
INSPECTING BIT/CUTTING TOOL. Damaged
bits/cutting tools may break apart during operation
and hit operator or bystanders. Dull bits/cutting
tools increase cutting resistance and are more
likely to grab and spin/throw workpiece. Always
inspect bits/cutting tools for sharpness, chips, or
cracks before each use. Replace dull, chipped, or
cracked bits/cutting tools immediately.
MAINTAINING MACHINE. Keep machine in prop-
er working condition to help ensure that it functions
safely and all guards and other components work
as intended. Perform routine inspections and all
necessary maintenance. Never operate machine
with damaged or worn parts that can break or
result in unexpected movement during operation.
CLEANING MACHINE SAFELY. To avoid contact
with tool/bit, never clear chips while spindle is
turning. To avoid cuts and eye injuries, DO NOT
clear chips by hand or with compressed air—use
a brush or vacuum instead.
DISCONNECT POWER FIRST. To reduce risk of
electrocution or injury from unexpected startup,
make sure drill is turned
OFF, disconnected
from power, and all moving parts have come to a
complete stop before changing bits/cutting tools
or starting any inspection, adjustment, or mainte-
nance procedure.
WEARING PROPER PPE. Flying chips created by
drilling can cause eye injuries or blindness. Always
wear a face shield in addition to safety glasses.
Always keep hands and fingers away from drill bit/
cutting tool. Avoid awkward hand positions, where
a sudden slip could cause hand to move into bit/
cutting tool.
AVOIDING ENTANGLEMENT. DO NOT wear
loose clothing, gloves, or jewelry, and tie back long
hair. Keep all guards in place and secure. Always
allow spindle to stop on its own. DO NOT stop
spindle using your hand or any other object.
REMOVING ADJUSTMENT TOOLS. Chuck key,
drawbar wrench, and other tools left on machine
can become deadly projectiles when spindle is
started. Remove all loose items or tools used on
spindle immediately after use.
SECURING BIT/CUTTING TOOL. Firmly secure
bit/cutting tool so it does not fly out of spindle dur-
ing operation or startup.
SECURING TABLE AND HEADSTOCK. To avoid
accidental contact with tool/bit, tighten all table
and headstock locks before operating drill.
CORRECT SPINDLE SPEED. Using wrong spin-
dle speed can cause bits/cutting tools to break
and strike operator or bystanders. Follow recom-
mended speeds and feeds for each size/type of
bit/cutting tool and workpiece material.
WORKPIECE PREPARATION. To avoid loss of
workpiece control, DO NOT drill material with an
uneven surface on the table, unless a suitable sup-
port is used. To avoid impact injuries, make sure
workpiece is free of nails or foreign objects in area
to be drilled.
Содержание G0810
Страница 60: ......