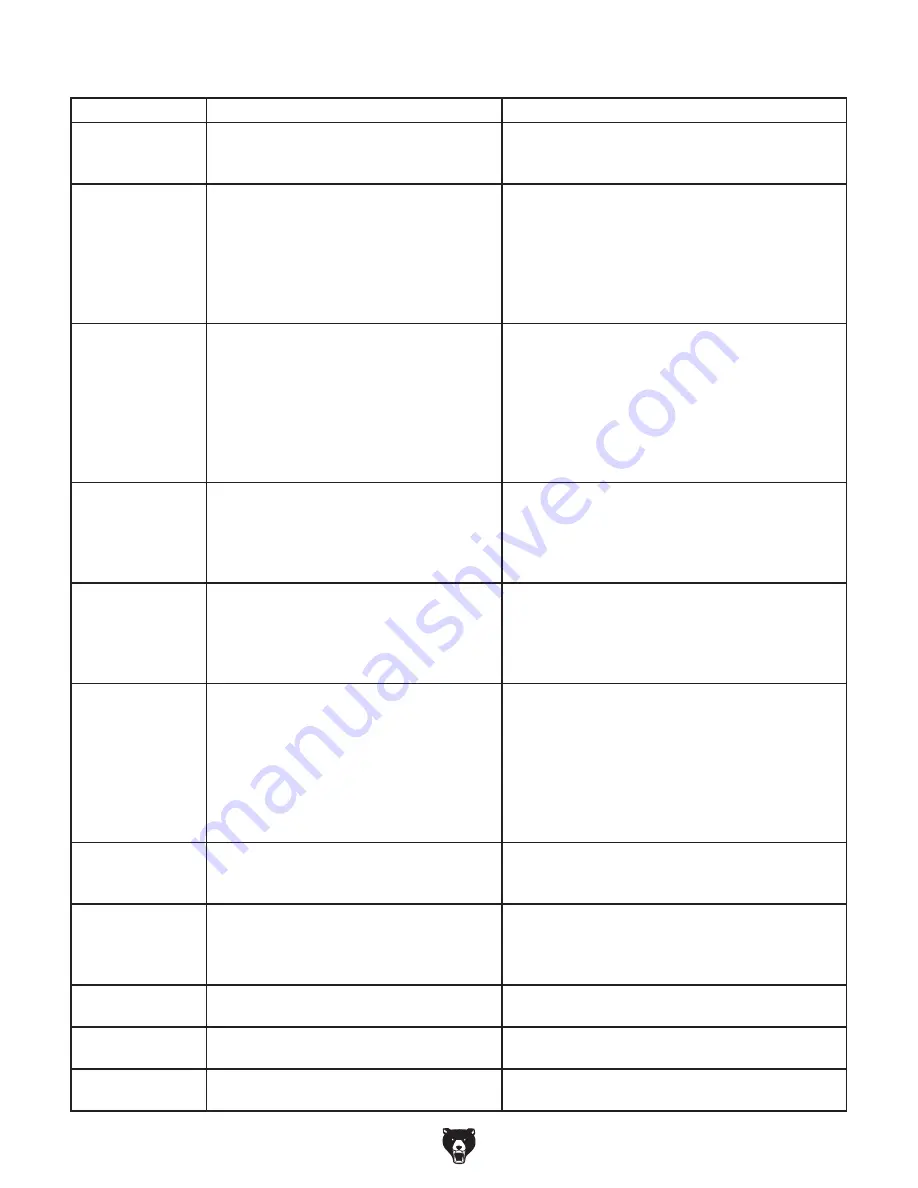
-52-
Model G0796/G0797 (Mfd. Since 1/18)
Mill
Symptom
Possible Cause
Possible Solution
Tool loose in
spindle.
1. Tool is not fully drawn up into spindle taper.
2. Debris on tool or in spindle taper
3. Taking too big of a cut.
1. Tighten drawbar.
2. Clean tool and spindle taper.
3. Lessen depth of cut and allow chips to clear.
Breaking tools or
cutters.
1. Spindle speed/feed rate is too fast.
2. Cutting tool is too small.
3. Cutting tool getting too hot.
4. Taking too big of a cut.
5. Spindle extended too far down.
1. Set spindle speed correctly or use slower feed rate
(
Page 34).
2. Use larger cutting tool and slower feed rate.
3. Use coolant or oil for appropriate application.
4. Lessen depth of cut and allow chips to clear.
5. Fully retract spindle and raise table (
Pages 30 and
37). This increases rigidity.
Workpiece or tool
vibrates or chatters
during operation.
1. Table locks not tight.
2. Workpiece not secure.
3. Spindle speed/feed rate is too fast.
4. Spindle extended too far down.
5. Quill lock lever not tight.
6. Gibs too loose in table.
1. Tighten table locks (
Page 30).
2. Properly clamp workpiece on table or in vise.
3. Set spindle speed correctly or use slower feed rate
(
Page 34).
4. Fully retract spindle and raise table (
Pages 30 and
37). This increases rigidity.
5. Tighten quill lock lever (
Page 37).
6. Tighten gibs (
Page 54).
Table is hard to
move.
1. Table locks are tightened down.
2. Chips have loaded up on ways.
3. Ways are dry and need lubrication.
4. Table limit stops are interfering.
5. Gibs are too tight.
1. Fully release table locks (
Page 30).
2. Frequently clean away chips or debris.
3. Lubricate ways (
Page 48).
4. Make sure that table limit stops are not in the way.
5. Adjust gibs (
Page 54).
Headstock is hard to
raise.
1. Headstock lock(s) or gib is at fault.
2. Headstock leadscrew is binding.
3. Gib is too tight.
1. Loosen/replace lock lever and adjust gib (
Pages 37
and 54).
2. Clean and relubricate headstock leadscrew and
gears (
Page 48).
3. Adjust gib (
Page 54).
Bad surface finish.
1. Spindle speed/feed rate is too fast.
2. Dull or incorrect cutting tool.
3. Wrong rotation of cutting tool.
4. Workpiece not secure.
5. Spindle extended too far down.
1. Set spindle speed correctly or use slower feed rate
(
Page 34).
2. Sharpen cutting tool or select one that better suits
the operation.
3. Check for proper cutting tool rotation.
4. Properly clamp workpiece on table or in vise.
5. Fully retract spindle and raise table (
Pages 30 and
37). This increases rigidity.
Cutting results not
square.
1. Table and spindle are not at 90° to each
other.
2. Table travel is inconsistent.
1. Tram the spindle (
Page 57).
2. Adjust gibs (
Page 54).
Spindle overheats.
1. Poor spindle bearing lubrication.
2. Spindle bearings too tight.
3. Mill operated at high speeds for extended
period.
1. Replace spindle bearings.
2. Properly adjust spindle bearing preload.
3. Allow mill to cool.
Lack of power at
spindle.
1. Belts are loose.
2. Wrong voltage.
1. Properly tension belts.
2. Correct voltage.
Spindle does not
fully retract.
1. Poorly adjusted return spring.
2. Worn return spring.
1. Increase return spring tension.
2. Replace return spring.
Spindle switch does
not work.
1. Shorted/disconnected wiring.
1. Inspect wiring connections. Replace/repair as
necessary.
Содержание G0796
Страница 96: ......