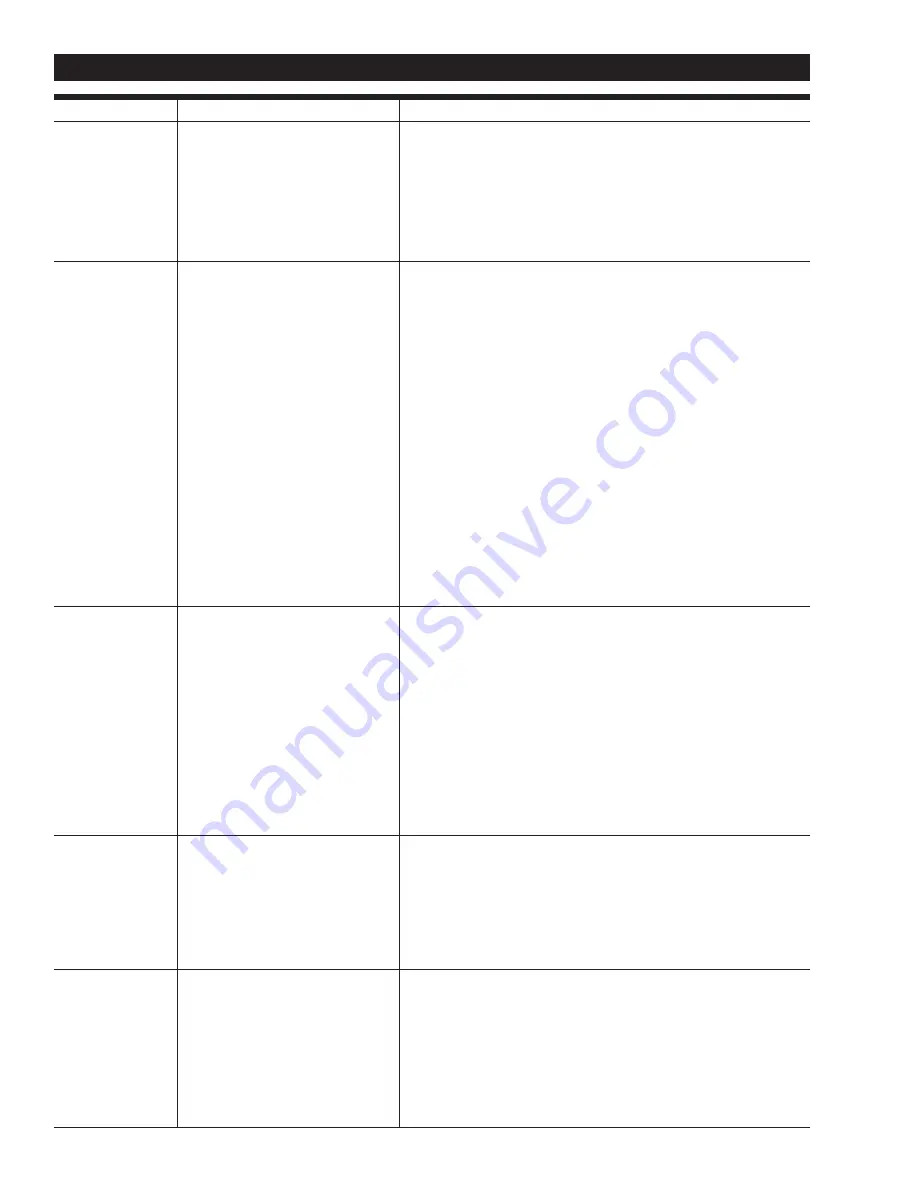
Rev. A 92149901
8
TROUBLESHOOTING
SYMPTOM
PROBABLE CAUSE
CORRECTIVE ACTION
A. MOTOR DOES
NOT RUN
1. Auxiliary temperature-limiting device
tripped
Turn pump switch off. Allow motor to cool approximately 30 minutes. Device
resets automatically. Try again.
2. Switch’s circuit breaker tripped
Turn power off at source. Determine source of high amp draw. Correct problem.
Make sure pump switch is in off position before restoring power. Restore power
to pump. Circuit breaker is reset manually by turning pump’s power switch off
and on
3. Switch defective
Remove switch coverplate and inspect switch. Replace, if necessary.
4. Motor burned out
Replace motor as described in the Repair Section.
B. MOTOR RUNS
BUT DOES NOT
PUMP FLUID
1. Drive key broken
Remove gear coverplate and replace drive key. Make sure gears turn freely
with the key removed.
2. Suction pipe clogged, damaged, or
missing
Remove pump from tank. Inspect suction pipe. Clean or replace, as necessary.
3. Gear coverplate or O-ring damaged
Remove and inspect the coverplate and O-ring. Replace, as necessary. Refer
to the Repair Section on Servicing O-rings.
4. Strainer clogged or defective
Remove strainer coverplate. Remove and clean strainer. Install again.
5. Bypass poppet O-ring worn or missing Inspect the O-ring, using instructions in the Repair Section. Replace, if
necessary.
6. Bypass poppet O-ring dirty
Remove poppet assembly and clean poppet and cavity.
7. System air leak
Tighten all pump fittings and connections. Inspect suction pipe for leaks or
damage.
8. System air lock
This can occur if external filter, meters, or an off-the-shelf automatic nozzle
is being used. To correct, remove the pipe plug in the top outlet port and
fill the gear cavity with fuel. Use of a factory-supplied automatic nozzle is
recommended.
9. Poor connections or low voltage
Make sure electrical connections are secure. Check power source.
10. Fuel level low
Fill tank.
11. Bypass poppet binding or damaged
Remove the bypass poppet, spring, and O-ring. Clean cavity. Inspect and
replace components, as necessary.
C. LOW
FLOWRATE
1. Poor connections or low voltage
Make sure electrical connections are secure. Also check power source.
2. Strainer partially clogged
Remove the strainer coverplate. Remove and clean the strainer. Install again.
3. Suction pipe clogged or damaged
Remove pump from tank. Inspect suction pipe. Clean or replace, as necessary.
4. Fuel tank empty
Fill tank.
5. Using off-the-shelf automatic nozzle
Factory-supplied automatic nozzle is recommended.
6. System air leak
Tighten all pump fittings and connections. Inspect suction pipe for leaks or
damage. Replace, as necessary.
7. Suction pipe too close to tank bottom Suction pipe must have at least 1/4 in. (0.6 cm) clearance from bottom of the
tank.
8. Bypass poppet spring weak
Remove the bypass poppet and inspect spring. Replace, if necessary.
9. Discharge hose too long
Long hoses reduce flow rate. Shorten hose.
D. MOTOR
STALLS WHEN
OPERATING IN
BYPASS MODE
1. Running too long in bypass mode
Limit bypass operation to 10 minutes.
2. Gears worn
Remove gear coverplate and inspect gears and drive key. Make sure gears
turn freely with the key removed. Replace, if worn.
3. Wiring defective
Use Wiring instructions in the Installation Section to ensure proper connections.
4. Bypass poppet binding or damaged
Remove the bypass poppet, spring, and O-ring. Clean cavity. Inspect
components and replace, as necessary.
5. Motor defective
Replace motor as described in the Repair Section
E. RAPID
OVERHEAT OF
MOTOR
1. Duty cycle too long
Pump operation should not exceed the standard duty cycle of 30 minutes ON,
and 30 minutes OFF. Allow the pump to cool for 30 minutes.
2. Strainer clogged
Remove strainer coverplate. Remove and clean strainer. Install again.
3. Suction pipe clogged or damaged
Remove pump from tank. Inspect suction pipe. Clean or replace, as necessary.
4. Gears worn
Remove gear coverplate and inspect gears and drive key. Make sure gears
turn freely with key removed. Replace, if necessary.
5. Fuel level low
Fill tank.
6. Running too long in bypass mode
Limit bypass operation to 10 minutes
Содержание M-1115S
Страница 11: ......