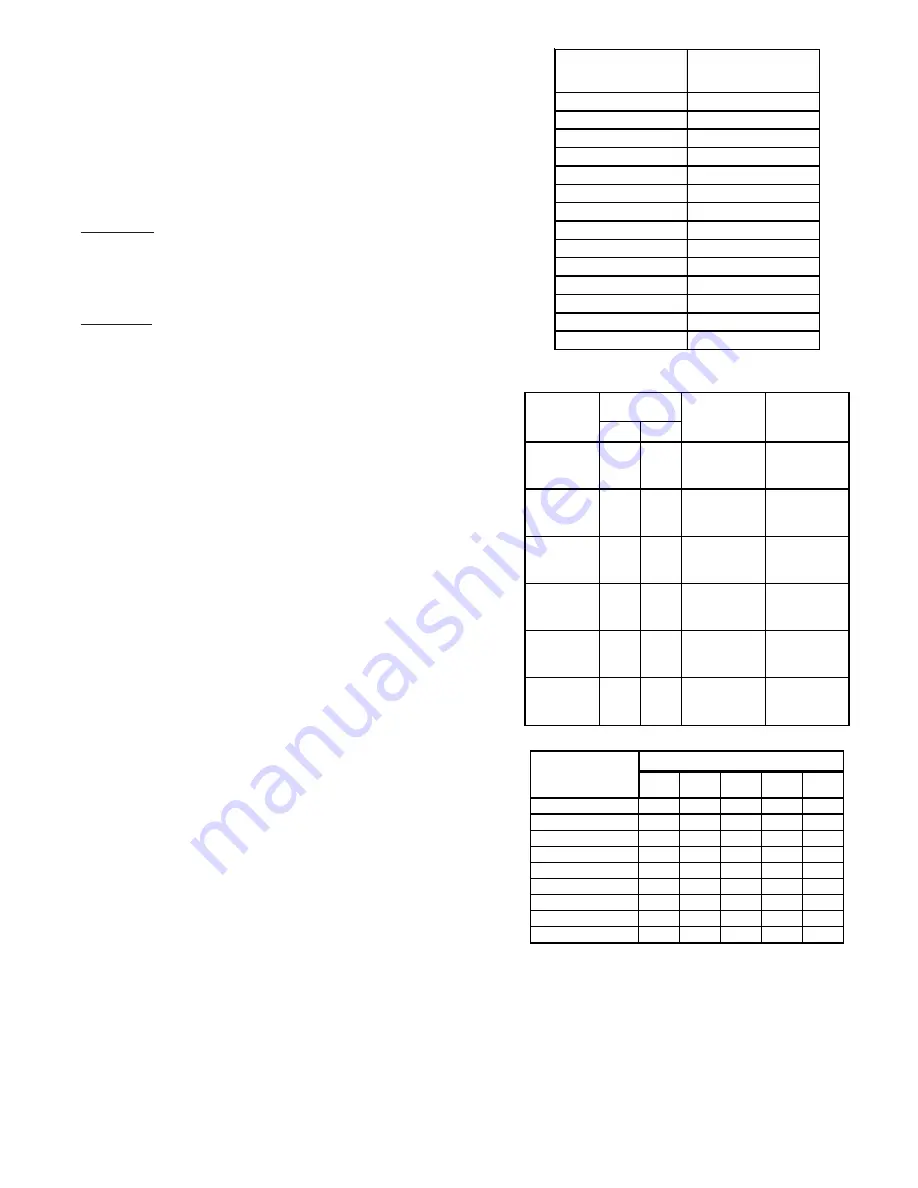
11
After unit is set and ducted, verify ESP with a 1" inclined
manometer with pitot tubes or a Magnahelic gauge and
confirm CFM to blower curves in the specification sheets.
All units have three speed blower motors. If low speed is not
utilized, the speed tap can be changed to medium or high
speed. Never run CFM below 350 CFM per ton, evaporator
freezing or poor unit performance is possible.
ADJUSTING SPEED TAP FOR INDOOR BLOWER
MOTOR
PSC Motor
Adjust the CFM for the unit by changing the speed tap of
the indoor blower motor at the EBTDR “com” connection
with one of the speed taps on “M1” or “M2”. (Black-High
Speed, Blue-Medium Speed, Red-Low Speed.)
X-13 Motor
The blower motor speed for the X-13 motor is controlled by
three 24V low voltage leads: green, yellow, and white. The
green lead sets the speed for fan-only mode. The yellow
lead sets the speed for cooling and heat pump heating
mode (if applicable). The white lead sets the speed for
electric heat mode (emergency heat and second stage
heat, if applicable).
The leads are factory connected as follows: Green to T1,
Yellow to T2, and White to T3. T1 is the low speed setting
and is dedicated to fan-only mode. T2 and T3 are medium
speed settings. T4 and T5 are high speed settings. To
adjust the blower speed, move the yellow and/or white wires
to T4 and T5.
NOTE:
If more than one lead is energized at
the same time, the motor will use the higher speed setting.
CHECKING CHARGE
After completing airflow measurements and adjustments, the
unit’s refrigerant charge must be checked. The design charge
(per table on page 7) is based on 400 CFM per ton at minimum
ESP per AHRI test conditions (generally between .15 - .25
ESP). When air quantity or ESP is different than above,
charge must be adjusted to the proper amount. All package
units should be charged to the superheat method at the
compressor suction line (these are fixed orifice devices).
For charging in the warmer months, 10
º
F superheat at the
compressor is required at conditions: 95
º
F outdoor ambient
(dry bulb temperature), 80
º
F dry bulb / 67
º
F wet bulb indoor
ambient, approximately 50% humidity. This superheat varies
when conditions vary from the conditions described.
A superheat charge chart is available for other operating
conditions. Use it to provide the correct superheat at the
conditions the unit is being charged at.
After superheat is adjusted it is recommended to check unit
sub-cooling at the condenser coil liquid line out. In most
operating conditions 10 - 15
º
F of sub-cooling is adequate.
Suction Pressure
Saturated Suction
Temperature (°F)
50
26
53
28
55
30
58
32
61
34
63
36
66
38
69
40
72
42
75
44
78
46
81
48
84
50
87
52
TABLE 5
Suction Pressure Temperature (R-22)
DB
WB
63
301 - 332
73 - 83
115
75
67
306 - 335
77 - 78
71
311 - 342
82 - 92
63
268 - 299
72 - 82
105
75
67
273 - 304
77 - 87
71
278 - 309
80 - 90
63
233 - 264
67 - 77
95
75
67
238 - 269
72 - 82
71
243 - 274
77 - 87
63
198 - 229
62 - 72
85
75
67
203 - 234
67 - 77
71
208 - 239
71 - 81
63
172 - 203
57 - 67
75
75
67
175 - 206
61 - 71
71
180 - 211
66 - 76
63
144 - 175
52 - 62
65
75
67
149 - 180
56 - 66
71
155 - 186
60 - 70
INDOOR
TEMP. °F
LIQUID
PRESSURE
PSIG
SUCTION
PRESSURE
PSIG
OUTDOOR
TEMP. °F
TABLE 6 -
Operating Pressures
65
70
75
80
85
100
-
-
-
10
10
95
-
-
10
10
10
90
-
-
12
15
18
85
-
10
13
17
20
80
-
10
15
21
26
75
10
13
17
25
29
70
10
17
20
28
32
65
13
19
26
32
35
60
17
25
30
33
37
Ambient Condenser
Inlet Temp (°F
Drybulb)
Return Air Temp. (°F Drybulb)
TABLE 7 -
System Superheat
SUPERHEAT CAN BE DETERMINED AS FOLLOWS:
1.
Read suction pressure. Determine Saturated Suction
Temperature from tables or pressure gauge saturated
temperature scale (R-22).
2.
Read suction line temperature.
3.
Use the following formula:
SUPERHEAT = SUCTION LINE TEMP - SAT. SUCTION TEMP
Содержание GPC 13 SEER H Series
Страница 18: ...18 THIS PAGE LEFT BLANK INTENTIONALLY...
Страница 19: ...19 THIS PAGE LEFT BLANK INTENTIONALLY...