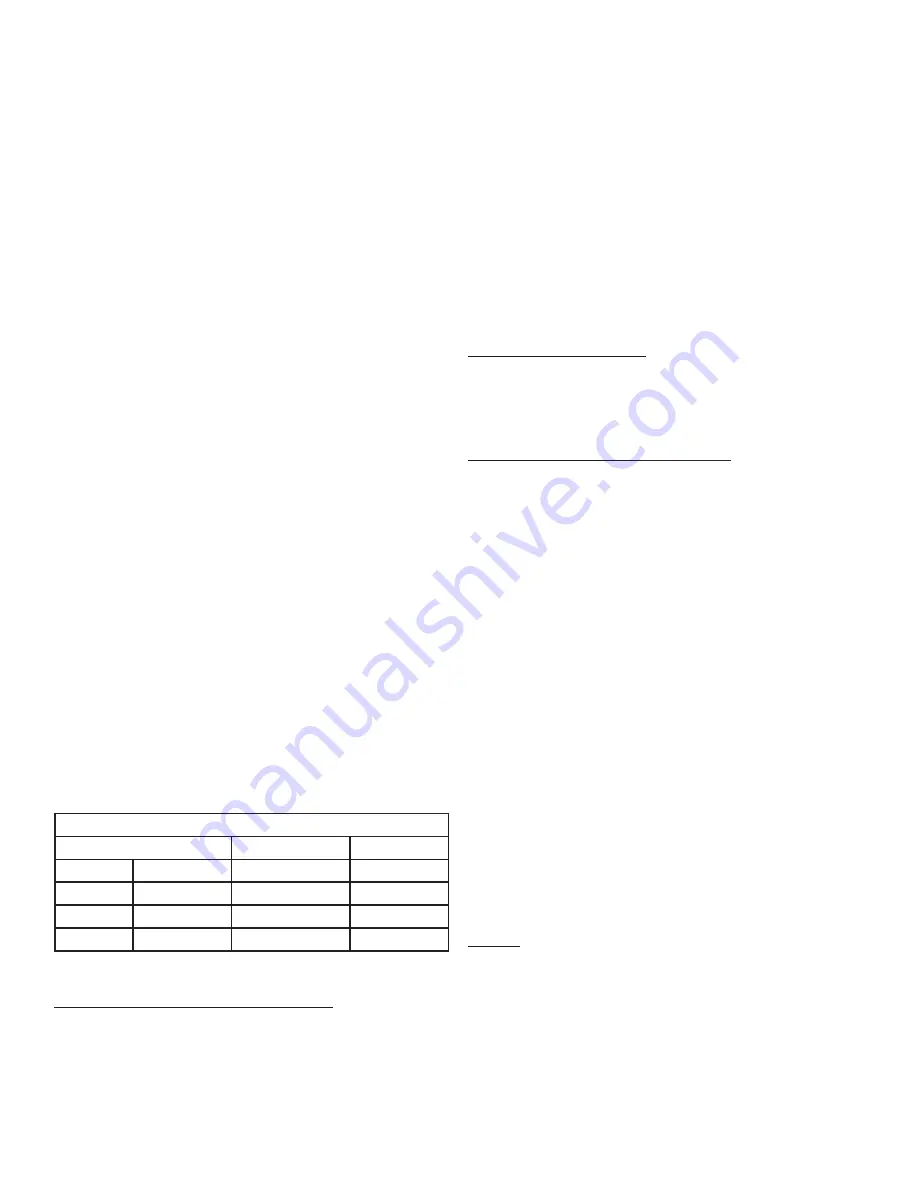
18
meter for one complete revolution. If this is a 2 cubic
foot dial, divide the seconds by 2; if it is a 1 cubic foot
dial, use the seconds as is. This gives the seconds
per cubic foot of gas being delivered to the unit.
3.
INPUT=GAS HTG VALUE x 3600 / SEC. PER
CUBIC FOOT
Example:
Natural gas with a heating value of 1000
BTU per cubic foot and 34 seconds per cubic foot as
determined by Step 2, then:
Input = 1000 x 3600 / 34 = 106,000 BTU per Hour.
NOTE:
BTU content of the gas should be obtained
from the gas supplier. This measured input must not
be greater than shown on the unit rating plate.
4.
Relight all other appliances turned off in step 1. Be
sure all pilot burners are operating.
Main Burner Flame Check
Flames should be stable, soft and blue (dust may cause
orange tips but they must not be yellow) and extending
directly outward from the burner without curling, floating or
lifting off.
Heat Pump Start-Up Procedure Cooling
Note:
The reversing valve is energized when the
thermostat is placed in the cooling position. A clicking
sound should be noticeable from the reversing valve. By
lowering the temperature setting to call for cooling, the
contractor is energized. The compressor, blower and fan
should then be running.
1.
Turn thermostat system switch to “Cool,” and fan-
switch to “Auto” and turn temperature setting as high
as it will go.
2.
Inspect all registers and set them to the normal open
position.
3.
Turn on the electrical supply at the disconnect.
4.
Turn the fan switch to the “ON” position. The blower
should operate after a 10 second delay.
5.
Turn the fan switch to “Auto” position. The blower
should stop after a 60 second delay.
6.
Slowly lower the cooling temperature until the unit
starts. The compressor, blower and fan should now be
operating. Allow the unit to run 10 minutes, make sure
cool air is being supplied by the unit.
7. Turn the temperature setting to the highest position,
stopping the unit. The indoor blower will continue to
run for 60 seconds.
8. Turn the thermostat system switch to “OFF” and
disconnect all power when servicing the unit.
Heating
1.
Turn the thermostat system switch to “HEAT” and fan
switch to “AUTO”.
2.
Slowly raise the heating temperature setting. When
the heating first stage makes contact, stop raising
the temperature setting. The compressor, blower and
fan should now be running with the reversing valve in
the de-energized (heating) position. After giving the
unit time to settle out, make sure the unit is supplying
heated air.
valve external to the furnace.
2.
Turn off all electrical power to the system.
3.
Back outlet pressure test screw (inlet/outlet pressure
boss) out one turn (counterclockwise, not more than
one turn).
4.
Attach a hose and manometer to the outlet pressure
boss of the valve.
5.
Turn ON the gas supply.
6.
Turn on power and energize main (M) solenoid. Do
not energize the HI solenoid.
7. Measure gas manifold pressure with burners firing.
Adjust manifold pressure using the Manifold Gas
Pressure table.
8. Remove regulator cover screw from the low (LO)
outlet pressure regulator adjust tower and turn screw
clockwise to increase pressure, or counterclockwise
to decrease pressure.
9.
Energize main (M) solenoid as well as the HI
terminal.
10.
Remove regulator cover screw from the HI outlet
pressure regulator adjust tower and turn screw
clockwise to increase pressure, or counterclockwise
to decrease pressure.
11.
Turn off all electrical power and gas supply to the
system.
12.
Remove manometer hose from outlet pressure boss.
13.
Turn outlet pressure test screw in to seal pressure
port (clockwise, 7 in-lb minimum).
14.
Turn on electrical power and gas supply to the
system.
15.
Turn on system power and energize valve.
16.
Using a leak detection solution or soap suds, check
for leaks at pressure boss screw. Bubbles forming
indicate a leak. SHUT OFF GAS AND FIX ALL
LEAKS IMMEDIATELY.
Manifold Gas Pressure
Gas
Range
Nominal
Natural
Low Stage
1.6 -2.2” W.C.
2.0” W.C.
High Stage 3.2 - 3.8” W.C.
3.5” W.C.
Propane
Low Stage
5.7 - 6.3” W.C.
6.0” W.C.
High Stage 9.7 - 10.3” W.C. 10.0” W.C.
Manifold Gas Pressure
Gas BTU Input (Natural Gas Only) Check
To measure the gas input use a gas meter and proceed as
follows:
1.
Turn off gas supply to all other appliances except the
unit.
2.
With the unit operating, time the smallest dial on the
Содержание 209319576
Страница 34: ...34 THIS PAGE IS INTENTIONALLY LEFT BLANK...
Страница 35: ...35 THIS PAGE IS INTENTIONALLY LEFT BLANK...