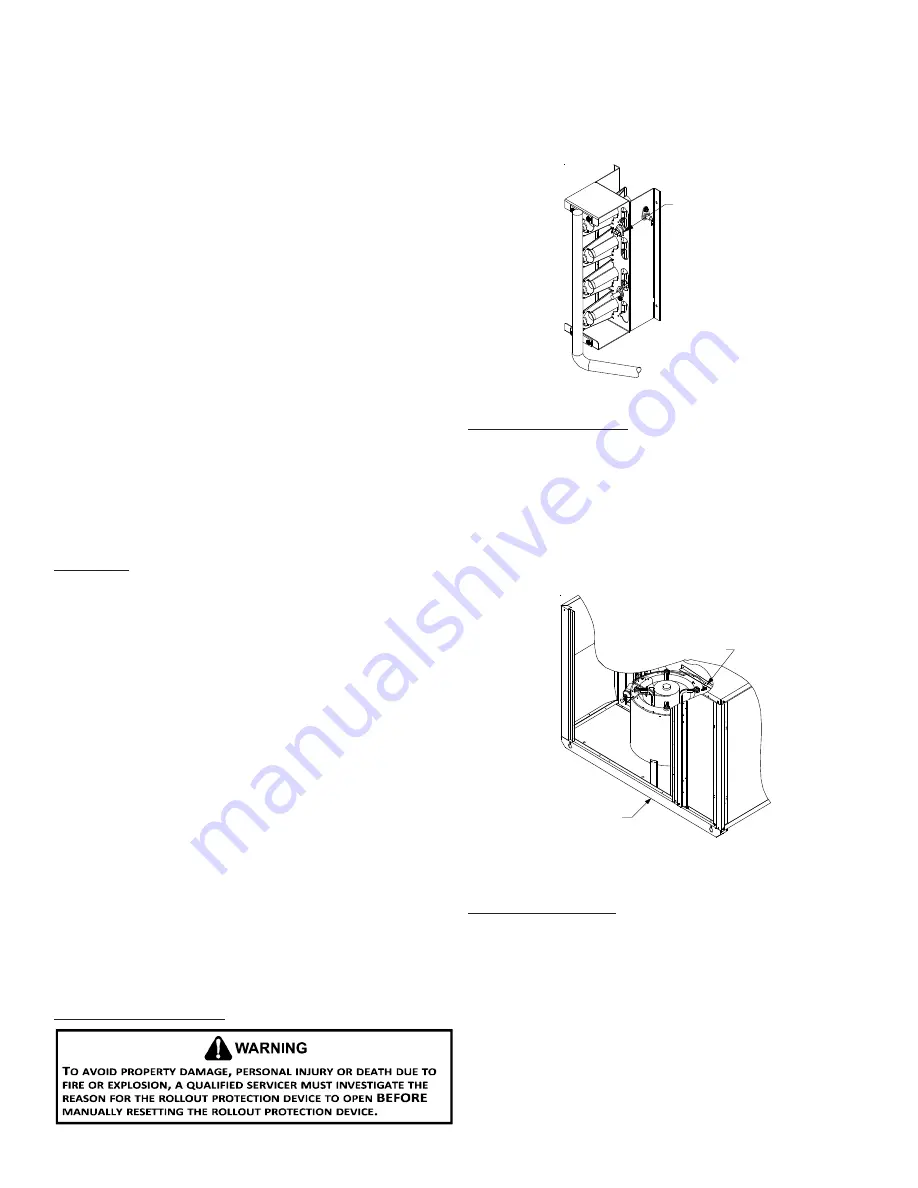
16
thermostat call for FAN is removed.
Air flow Measurement and Adjustment
Please review the Duct Work section before proceeding
with the airflow measurements and adjustments in this
section.
Unit blower curves (see Specification Sheets) are based
on external static pressure (ESP per in/W.C.). The
duct openings on the unit are considered internal static
pressure. As long as ESP is maintained, the unit will deliver
the proper air up to the maximum static pressure listed for
the CFM required by the application (i.e. home, building,
etc.)
In general, 400 CFM per ton of cooling capacity is a rule
of thumb. Some applications depending on the sensible
and latent capacity requirements may need only 350 CFM
or up to 425 CFM per ton. Check condition space load
requirements (from load calculations) and equipment
expanded ratings data to match CFM and capacity.
After unit is set and duct work completed, verify the ESP
with a 1-inch inclined manometer with pilot tubes or a
Magnahelic gauge and confirm CFM to blower curves in the
Specification Sheets.
NOTE:
Never run CFM below 350 CFM per ton, evaporator
freezing or poor unit performance is possible.
Air Flow Adjustments For Indoor Blower Motor
EEM Motor
Adjust the CFM by changing the 24V low voltage lead at
the speed terminal block on the motor. (T1, T2, T3, T4,
T5). See Blower Performance Data in the appendix for
airflow delivered at each speed tap.
NOTE:
Factory set T1 (G, fan and low stage gas heat), T2
(high stage gas heat, T4 (nominal heat pump / cooling).
T3 is for optional low speed cooling and heat pump. T5 is
for optional high speed cooling and heat pump.
START-UP, ADJUSTMENTS, AND CHECKS
Heating Start-up ( Natural Gas / LP)
This unit is equipped with an electronic ignition device to
automatically light the main burners. It also has a power
vent blower to exhaust combustion products.
On new installations, or if a major component has been
replaced, the operation of the unit must be checked.
Check unit operation as outlined in the following
instructions. If any sparking, odors, or unusual sounds are
encountered, shut off electrical power and check for wiring
errors, or obstructions in or near the blower motors.
Rollout Protection Control
The rollout protection device opens, cutting power to the
gas valve, if the flames from the burners are not properly
drawn into the heat exchanger. The rollout protection
device is located on the burner bracket. The reason for
elevated temperatures at the control must be determined
and repaired prior to resetting this manual reset control.
Rollout Protection
Rollout Protection on Burner Bracket
Secondary Limit Control
The secondary limit control is located on the top of the
blower scroll assembly. This control opens when elevated
temperatures are sensed. Elevated temperatures at the
control are normally caused by blower failure.
If the power to the unit is interrupted during the heating
cycle, it may cause the secondary limit to trip. Once the
blower compartment temperature drops below the limit
reset temperature, the limit will automatically reset.
Secondary
Control Limit
Back of Unit
Secondary Control Limit
Pre-Operation Checks
1.
Close the manual gas valve external to the unit.
2.
Turn off the electrical power supply to the unit.
3.
Set the room thermostat to its lowest possible setting.
4.
Remove the heat exchanger door on the side of the
unit by removing screws.
5.
This unit is equipped with an ignition device which
automatically lights the main burner. DO NOT try to
light burner by any other method.
6.
Move the gas control valve switch to the OFF
position. Do not force.
Содержание 209319576
Страница 34: ...34 THIS PAGE IS INTENTIONALLY LEFT BLANK...
Страница 35: ...35 THIS PAGE IS INTENTIONALLY LEFT BLANK...