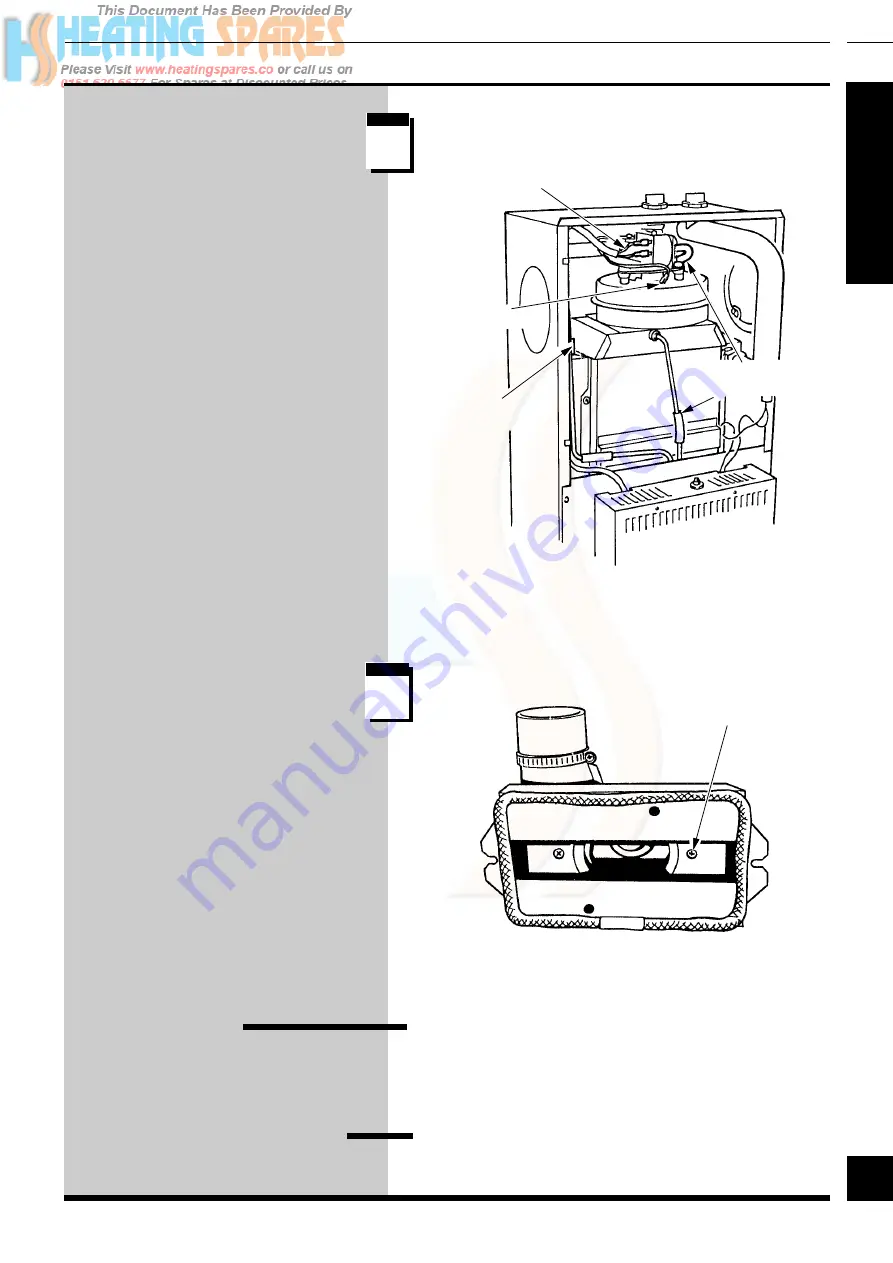
Supplied By www.heating spares.co Tel. 0161 620 6677
49
220692C
49
SECTION
12
Replacement of Parts
Main Burner
Main Burner Injector
Gain access as Section 10, steps 1 to 5 and 9.
Remove burner as in Section 10, step 13.
Gain access as Section 10, steps 1 to 5 and 9.
Remove the injector as in Section 10, steps 13 and 14.
Fan
Gain access as Section 10, steps 1, 2
and 5.
Remove the electrical connections and
disconnect the air tubes.
Remove the fluehood/fan assembly
screws and withdraw the assembly.
Turn the flue hood over and release the
two securing screws as shown.
Remove the sealant from the fan outlet
and manifold.
Take the beige/grey sealant supplied
with the replacement fan and place
firmly around the internal spigot of the
flue manifold.
After fitting the fan outlet to the spigot
smooth the sealant over the joint.
Make sure that when fitting the
replacement fan to the flue hood that it
is the correct way round for connection
to the flue, refer to the diagram in
Section 6, also steps 10 and 11.
Make sure that the earth connection
is remade onto the new fan assembly.
The polarity of the other connections is
not important.
3058
SECURING
SCREW (2)
FAN/FLUEHOOD
SCREW (2)
AIR PRESSURE
SWITCH TUBES
ELECTRICAL
CONNECTIONS
s t e p
1
s t e p
2
EARTH
CONNECTION