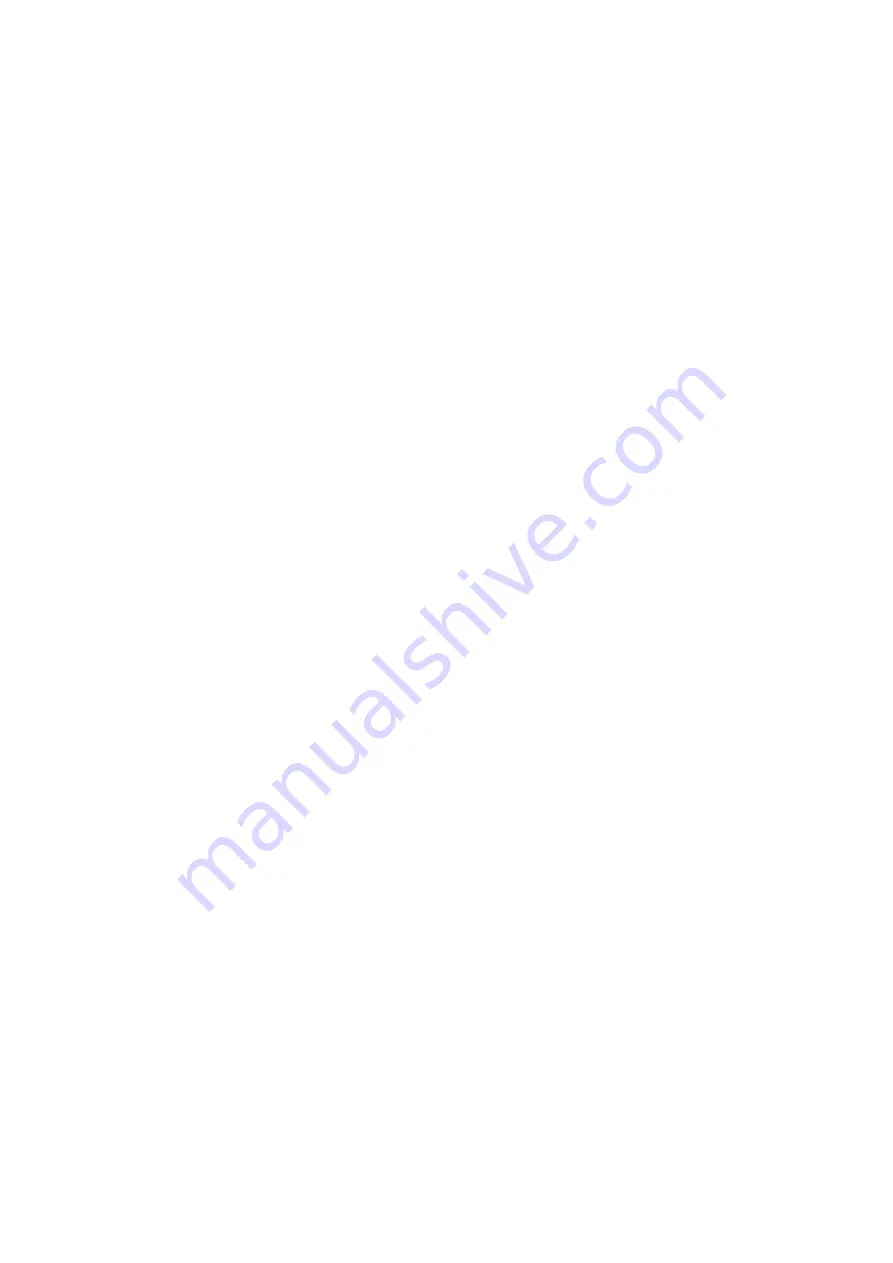
11. CONTENTS OF PACKAGE
SUPPLIED
The following parts are supplied:
A:
Contains the front element, rear element, intermediate
elements (4,11), any turbofans, the gaskets and rings, tie-
rods and assembly guides, doors and accessories.
B:
Contains the jacket and insulation.
C:
Contains the lower and upper front panel.
D:
Contains the instrument support.
12. INSTALLATION
(fig. 5)
The boiler must be installed by a properly qualified person.
It must be installed in a room of a suitable size in compliance
with the relevant safety rules.
The plumbing system must ensure a minimum flow of water into
the boiler as shown in the specification.
In the technical data table and the picture 22 the loses of head
side water of the boiler are indicated.
Figure 5 shows two examples of plumbing system layout. If a
sealed expansion tank is used, a safety valve must be fitted.
Always remember to comply with any local rules on the safety
of heating systems.
LEGEND
1 -Open expansion tank
6 -Delivery
2 -Pump
7 -Heating shell
3 -One-way valve
8 -Sealed expansion tank
4 -Re-circulation pump
9 -Filling valve
5 -Return
10 -Safety valve
13. HOW TO INSTALL THE BOILER
Boiler installation INVOLVES 4 separate stages.
1. Assembling the boiler shell.
2. Mounting the doors, burner and turbofans (only for boilers
with 6 or 7 elements).
3. Mounting the jacket and control panel.
4. Plumbing connections and hydraulic test.
NOTE: Distance between Burners axis and Ground is 302
mm, so if the Burner is higher than the normal, a
basement of right height is necessary to be
mounted underneath the Boiler (at least 150 mm).
STAGE 1 - Assembling the boiler shell (figs. 6, 7, 8, 9, 10)
1) Place the slides (8) in the boiler's final position in the room.
Fix the rear element (1) to the slides using M10x35 bolts (6,
7, 9).
2) Fill the slots "A" in the flue gas area and edging with the
sealant supplied.
3) Mount the containment ring (33) on the hubs with the gasket
(32) in a central position. Bring the 1
st
intermediate element
(31) up to the rear element (1).
CAUTION! To keep the elements vertical and parallel, use
awire "B" wound round the upper hubs.
4) Repeat steps 2 and 3 for all the intermediate elements (31)
and the front element (30).
5) Insert the tie-rods (10) with the shorter threaded part "C"
towards the front. Centre the 17x34x4.2 washers (5) and
screw in the nuts (4) by hand.
6) Inlet and outlet distributor (37, 38 fig.23) must be mounted
screwing them upon threads on the rear section. This
operation must to be absolutely set before clenching the
Boiler body.
7) Tighten the nuts (4) alternately until the elements come into
contact. Complete the operation with a dynamometric
spanner set to 5 kgm (* 50 Nm).
8) Mount the 1 1/4" adapters (15) on the front element (30) the
sheath (28) for the probes in the upper adapter and the
drain cock (16) in the lower one.
STAGE 2 -Mounting the doors and burner (figs. 12, 2)
1) Apply the insulating cord (35) (ø12x1300) to the upper door
(20) and the insulating cord (36) (ø 12x1070) to the lower
door (18). Insert them by knocking slightly with a mallet and
make a joint "D" at the bottom of the door.
2) Determine which side the doors (20, 18) are to open. Mount
the M12x130 tie-rods (23) using the nuts (11) and washers
(12). On the other side mount the eyebolts (13) and tighten
them temporarily using the nuts (11) and washers (12).
3) Mount the cleaning door (20) and burner door (18), locking
them in the eyebolts (13) by means of the respective pins
(29, 14).
CAUTION! After inserting the pins, remember to tighten
the eyebolts (13) fully.
4) Only for boilers with 6 or 7elements: fit the turbofans (27) (n.
4 for 6 elements and n. 2 for 7 elements)
NOTE: Turbofans for 7-element boilers must be inserted in
the central flue gas passages.
5) Close the doors and tighten the brass nuts (21).
CAUTION! Check carefully that the doors close properly.
STAGE 3 - Mounting the jacket and control panel
(figs. 2, 12, 13, 14, 15, 16, 17, 18, 19)
1) Cover the boiler shell with layers of insulation (57) making
sure the bottom one is centred and adheres properly.
2) Mount the brackets (24, 25) on the front element and lock
them with nuts M16 (26).
3) Fit the insulating panel (58) onto the rear element (1),
centring the holes in the tie-rods (10).
4) Mount the rear panel (63), centring the holes in the tie-
rods (10).
5) Mount the sides (40, 55) of the jacket.
6) Lock the sides onto the brackets (24, 25) and to the rear
panel (63) using the screws (65).
7) Secure the control panel (45) onto the instrument
support (46) using the four screw (44)
8) Unwind the capillaries of the thermostats (50, 52) and
the thermometer (47). Insert the probes in the sheath
(28) and tighten them with the probe retaining spring.
CAUTION! When unwinding the capillaries, be very careful
not to create sharp bends or twists.
9) Mount the complete control panel onto the side panel (40,
55) centring the holes and secure it with the screws (65).
10) Connect the cable of the power supply, insert this in the
wire lead and lock this in position.
CAUTION!
Connect all earthing cables to the screw.
11) Lastly, mount the top panel (56) and the front panel (43, 42)
in that order.
12) Stick the rating plate on to the right-hand side panel (40) of
the jacket.
STAGE 4 -Plumbing connections and hydraulic test
Fill the boiler and carry out a hydraulic test in compliance with
the European standard EN 303-1.
The test pressure must be 6.5 bar.
14. CONNECTING TO THE STACK
The products of combustion must be discharged through a pipe with
a diameter at least that of the flue gas pipe, connected to a stack
with a suitable capacity. The cross section and height of the stack
must guarantee the minimum draft specified and the thermal
insulation must comply with the relevant standards. The
SPECIFICATION table shows load loss values on the gas side for
each model of boiler.
15. INSTALLING THE BURNER
(fig. 2)
The lower panel (18) has a coupling for the burner.
For 6÷10 sections 4 coupling M8 on Ø170 are used.
For 11÷13 sections two different coupling are used:
•
N°4 of M8 – Ø170 centre distance
•
N°4 of M10 – Ø240 centre distance.
It is advisable to graphitize the burner screws to facilitate removal
later on.
If the burner has a flange that can not be adapted to the fitting, an
adapter is required plus an insulation panel.
The diameter of the burner head may differ from that of the
insulation, in which case the hole must be adapted as accurately
as possible to prevent backfiring.
The maximum diameter allowed is 150 mm.
Содержание GIEGA NTG 114
Страница 1: ...GIEGA NTG 82 220 kW GAS OR OIL BOILER INSTALLATION AND MAINTENANCE HANDBOOK 1312 1312AS2413 711292...
Страница 3: ...1 7 6 2 3 4 5 6 7 2 3 10 8 5 4 9 Fig 5 Fig 6 Fig 8 Fig 7 Fig 9...
Страница 4: ...58 57 24 25 26 63 10 Fig 10 Fig 11 Fig 12 Fig 13...
Страница 5: ...40 55 65 24 25 40 55 65 63 45 46 44 65 56 65 Fig 14 Fig 18 Fig 17 Fig 16 Fig 15...
Страница 6: ...43 42 37 38 Fig 19 Fig 23 Fig 22 Fig 21 Fig 20...
Страница 14: ...GIEGA NTG 82 220 kW MANTEMENIOI 1312 1312AS2413...
Страница 15: ...1 2 1 3 4 5 1 31 20 31 B EN 303 MANUFACTURER SERIAL NUMBER MODEL POWER...
Страница 19: ...16 17 18 fig 3 5 R 51 50...