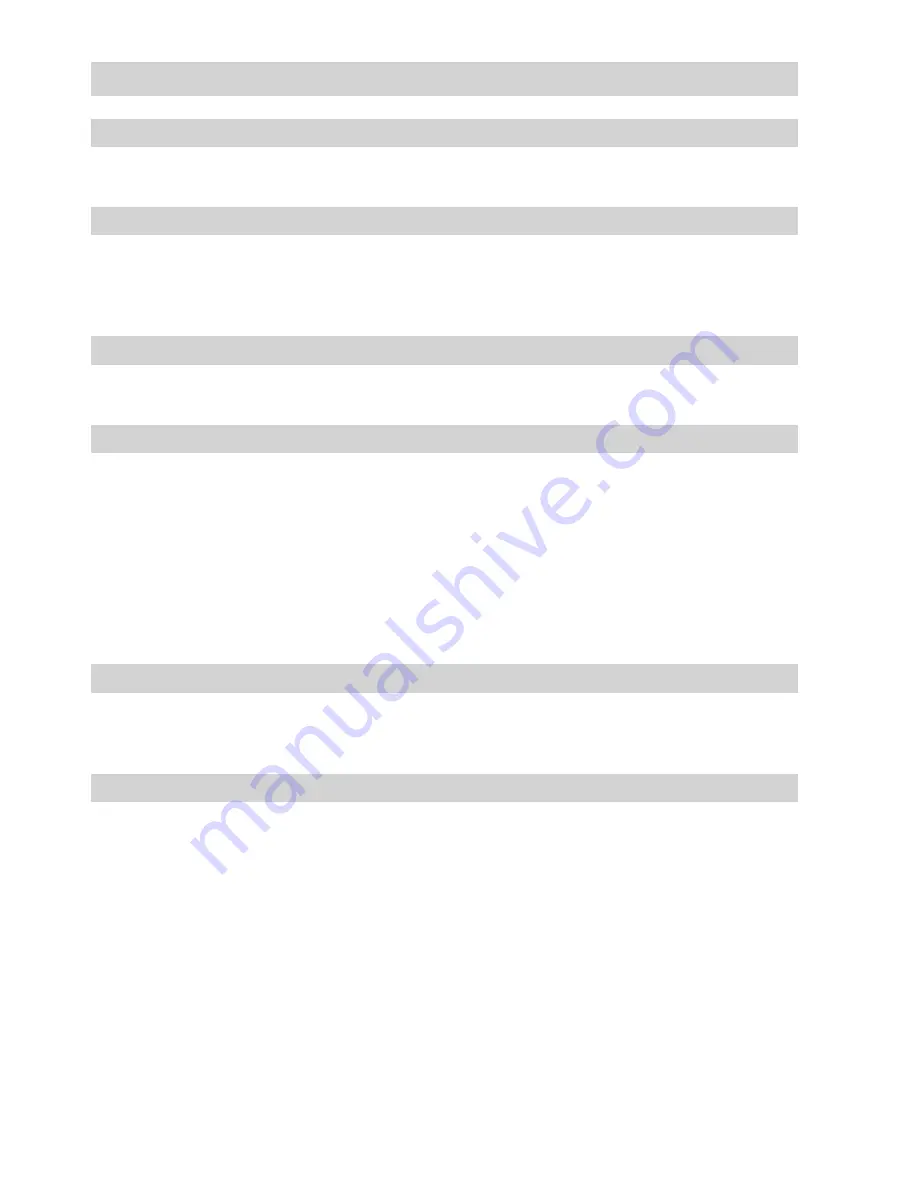
4
Danger .................................................................................................................................................35
NRR 240 .............................................................................................................................................35
Danger .................................................................................................................................................36
Systematic malfunction analysis ...........................................................................................................36
System malfunction 1 ...........................................................................................................................37
System malfunction 2 ...........................................................................................................................37
System malfunction 3 ...........................................................................................................................38
System malfunction 4 ...........................................................................................................................39
System Malfunctions
Danger .................................................................................................................................................39
Disposal................................................................................................................................................39
Decommissioning
Contents
– continued –
Page
NRR 240 .............................................................................................................................................33
MAX alarm ............................................................................................................................................33
MIN alarm .............................................................................................................................................33
Alarm
NRR 240 .............................................................................................................................................32
Test
Note on the Declaration of Conformity / Declaration by the Manufacturer .............................................39
Annex
Fault finding list for troubleshooting ......................................................................................................34
Operational malfunctions
Содержание NRR 2-40
Страница 1: ...1 E N English Level Controller NRR 2 40 Original Installation Instructions 810369 06 ...
Страница 9: ...9 Technical Data continued Dimensions Fig 2 1 1 8 100 73 ...
Страница 10: ...10 Design 0 Fig 3 9 NRR 2 40 9 a ...
Страница 11: ...11 Functional Elements NRR 2 40 Fig 5 Fig 4 1 7 6 5 4 3 2 8 ...
Страница 13: ...13 Installation continued Fig 6 Example of Installation b 9 0 0 Fig 7 20 20 a ...
Страница 17: ...17 Fig 10 NRR 2 40 as continuous controller Wiring diagram Electrical Connection continued d e g l h k i l ...