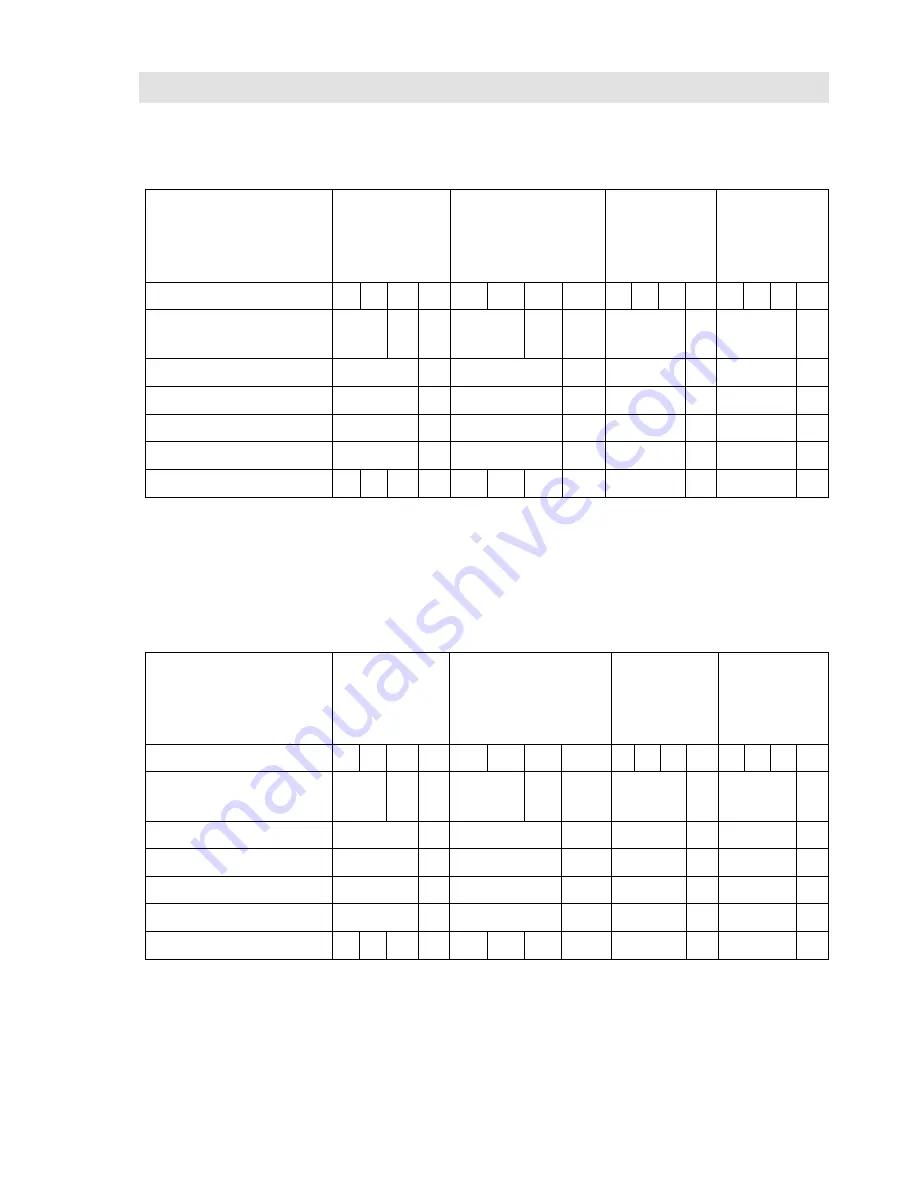
29
Technical data
Dimensions and weights
BW 31
Flanges to
EN PN40*
Flanges to ASME
Class 150/Class 300
Screwed
sockets,
socket-weld
ends
Butt-weld
ends via
transition
pieces
Nominal size DN
15 20 25 40 15 20 25 40 15 20 25 40 15 20 25 40
Overall length [mm]
150 160 200
150
160 216/
230**
95
130
200
Height without ESD*** [mm]
128
188
128
188
128
188
128
188
Height with ESD*** [mm]
187
248
187
248
187
248
187
248
Space required for servicing
110
70
110
70
110
70
110
70
Width of cover flange[mm]
85
115
85
115
85
115
85
115
Weight [kg]
4.4 5.3 5.7 12 4.4 5.3 5.7 12
2.4
8.0
2.9
8.5
* DN40: PN25
** Class 300: 230 mm
*** External setting device
BW 31A
Flanges to
EN PN40*
Flanges to ASME
Class 150/Class 300
Screwed
sockets,
socket-weld
ends
Butt-weld
ends via
transition
pieces
Nominal size DN
15 20 25 40 15 20 25 40 15 20 25 40 15 20 25 40
Overall length [mm]
150 160 200
150
160 216/
230***
95
130
200
250
Height without ESD*** [mm]
128
188
128
188
128
188
128
188
Height with ESD*** [mm]
150
235
150
235
150
235
150
235
Space required for servicing
110
70
110
70
110
70
110
70
Width of cover flange[mm]
85
115
85
115
85
115
85
115
Weight [kg]
4.4 5.3 5.7 12 4.4 5.3 5.7 12
2.4
8.0
2.9
8.5
* DN40: PN25
** Class 300: 230 mm
*** External setting device