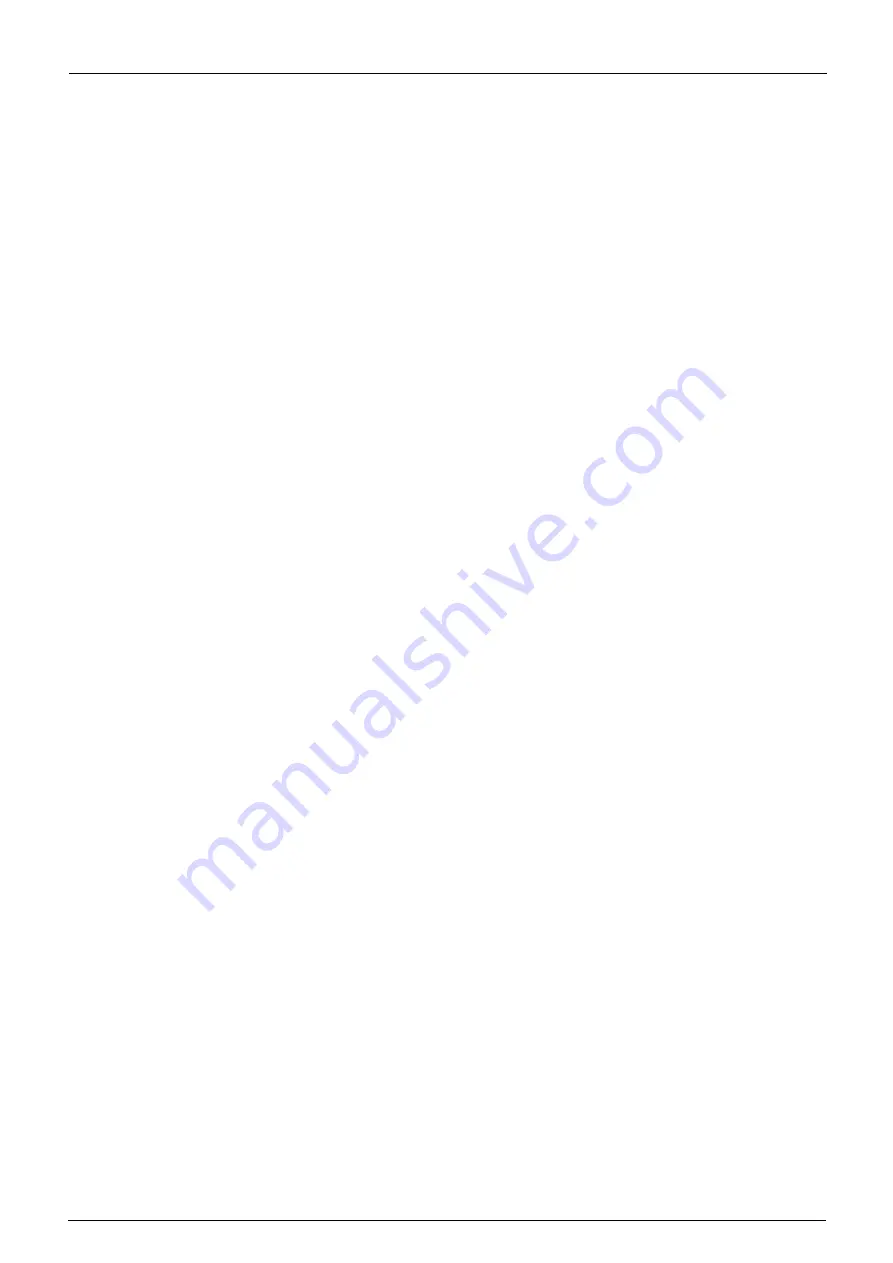
4
Hilge GmbH & Co. KG | BA.H2A.KYY.001.01.17.GB
Operating manual
GEA Hilge HYGIA K
6.4.2 Overview of parts of the K Lantern ______________________________________________________ 21
6.4.3 Overview of the drive parts ____________________________________________________________ 22
6.4.4 Instructions for disassembly ___________________________________________________________ 22
6.4.5 Instructions for assembly ______________________________________________________________ 23
6.4.6 Mounting of the shaft sleeve ___________________________________________________________ 23
6.4.7 Assembly of the motor, lantern and pump shaft ____________________________________________ 24
6.4.8 Assembly of the single mechanical seal, spiral spring _______________________________________ 27
6.4.9 Installing the mechanical seals _________________________________________________________ 28
6.4.10 Assembly of impeller and pump housing _________________________________________________ 29
6.4.11 Assembly of SUPER shroud __________________________________________________________ 32
6.5 Troubleshooting ____________________________________________________________________________ 33
6.6 Disposal ___________________________________________________________________________________ 34
6.7 HILGE assembly tool kit ______________________________________________________________________ 34
6.7.1 Contents and use ___________________________________________________________________ 34
7 Certificate of non-objection ____________________________________________________________________________ 35