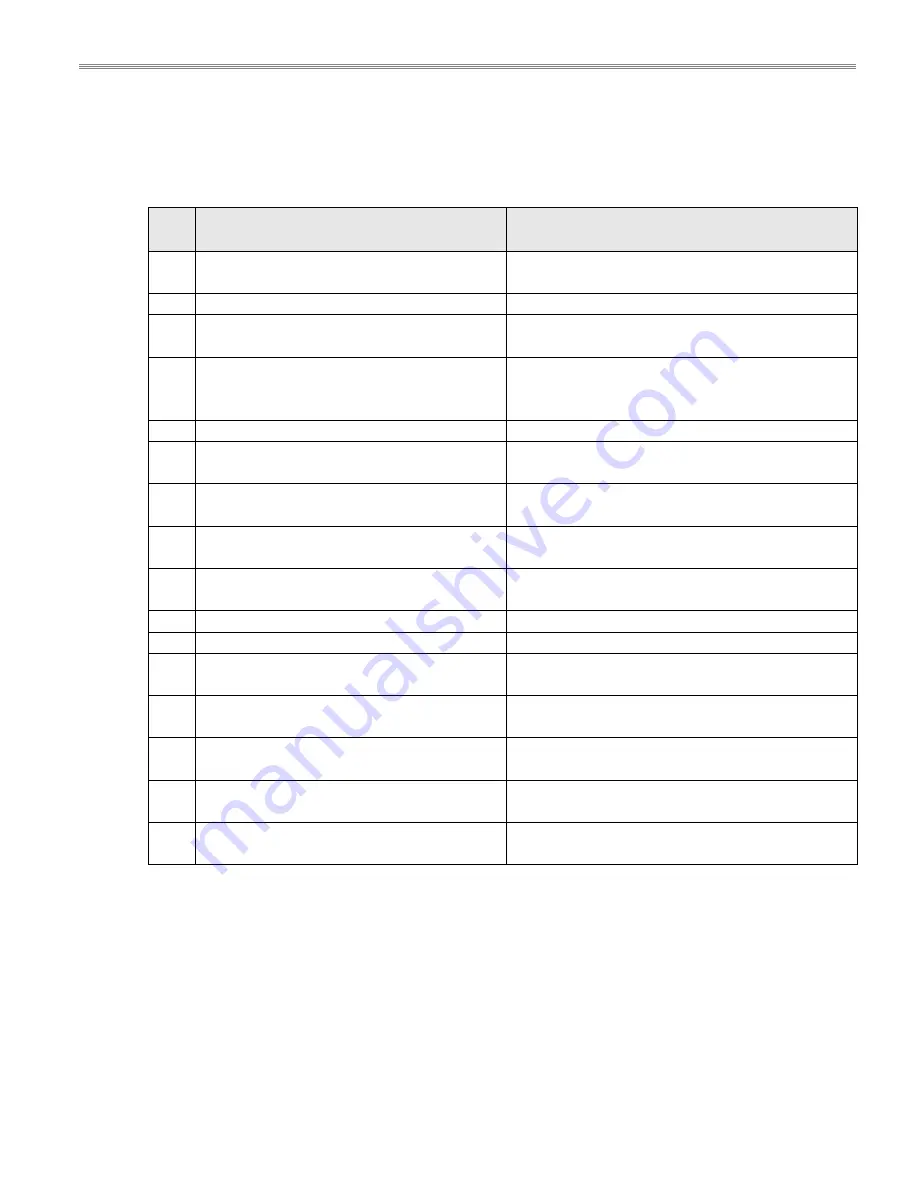
Troubleshooting
RTCSmp Built-In Temperature Controlled Hold-Line
Part # 4532287 Rev 2 (1/20/14)
25
10.3
Troubleshooting with Error Codes (for Service Technicians)
To obtain the internal data for troubleshooting, you need an IR Adapter, proper connectors, and software. The
table below is a reference guide. For further information and assistance, please contact Garland Technical Service.
Error
Code
Reason
Things To Check
E01
Hardware overcurrent or coil is not
connected(1)
Check the Chafing Dish or Pan material, Check wiring.
E02
Software overcurrent (1)
Check the Chafing Dish or Pan material.
E03
Heat sink overtemperature
T > 85°C (1)
Check installation (Airflow).
E04
Empty cooking detektor
Total failure of the sensor unit or sensor unit not
connected (1)
Check sensor unit.
Set point: 1080Ohm at 25°C
E05
Potentiometer defect or not connected (1)
Check the potentiometer wiring.
E06
Temperature inside the generator too high.T >
80°C (1)
Check installation (Airflow).
E10
Reduction KK temperature
T > 75°C (2)
Check installation (Airflow).
E12
Reduction internal temperature
T > 70°C (2)
Check installation (Airflow).
E20
Faulty or not connected heat sink temperature
sensor (1)
Contact Garland.
E21
Board sensor defect (1)
Contact Garland.
E24
Temperature processor central unit > 100°C (1) Check installation (Airflow).
E30
Heat retention plate sensor 1 over temperature
or defect (1)
Check warming process. Check sensor 1 Set point:
1080Ohm at 25°C
E41
Heat retention plate sensor 2 over temperature
or defect (1)
Check warming process. Check sensor 2 Set point:
1080Ohm at 25°C
E42
Heat retention plate sensor 3 over temperature
or defect (1)
Check warming process. Check sensor 3 Set point:
1080Ohm at 25°C
E43
Reduction KK temperature
T > 75°C (2)
Check installation (Airflow).
E01
Hardware overcurrent or coil is not
connected(1)
Check the Chafing Dish or Pan material, Check wiring.
(1) Power supply is interrupted immediately.
(2) The unit works with reduced power.