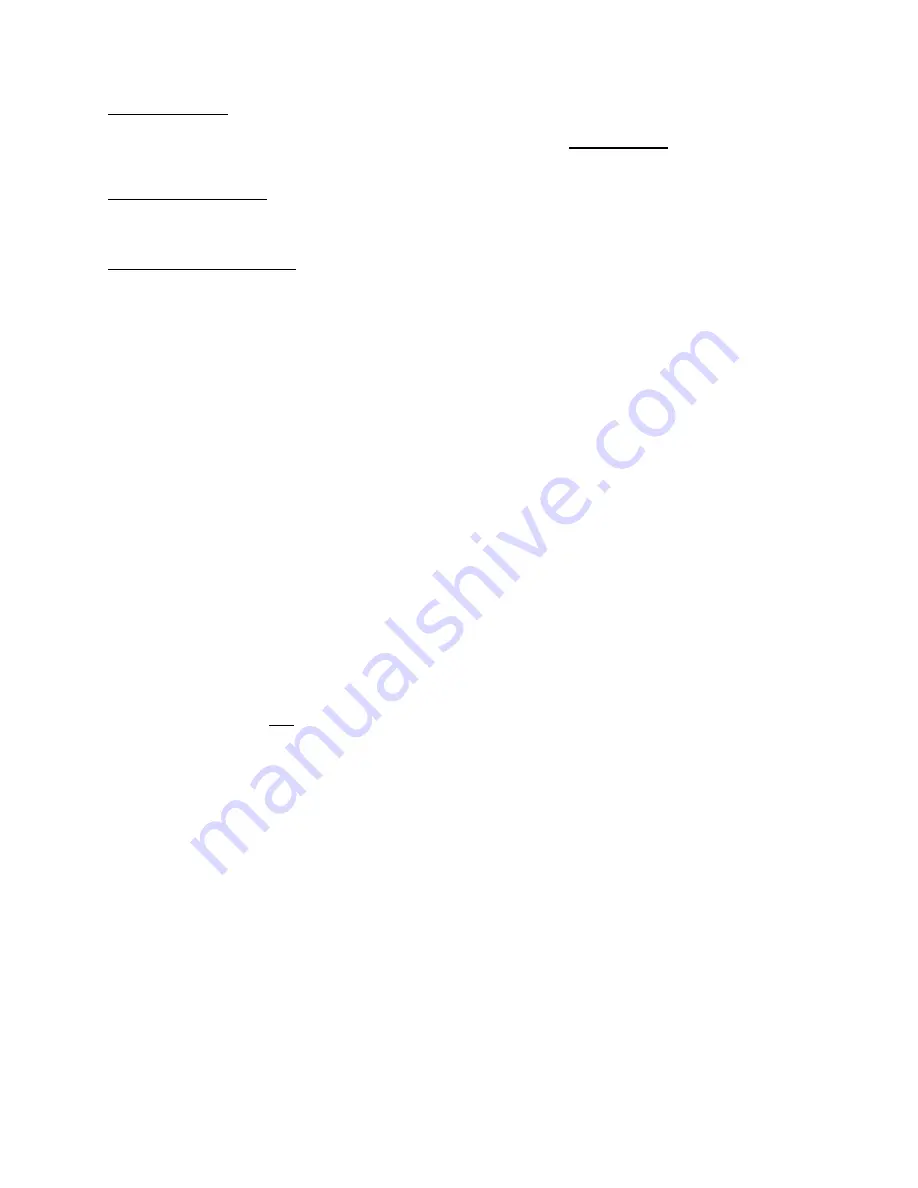
13-11-607 Page 44
The capillary tube (mm) controls the flow of wash water used to flush away the contaminants captured by
the RO membrane. The flushing process, active whenever the membrane is filtering water, requires 3.5
gpm of treated water for every 1 gpm of treated water delivered. The fast-flush valve (ll) is provided to
intensify the flushing process during periodic maintenance.
The 3.2 gal holding tank (nn) stores the filtered water output from the RO membrane for use in timed
batch cycles. An internal flexible membrane, pressurized with 10 psig air (tank without water), helps
evacuate the water from the holding tank.
The electronic timer module, included in the supplied programmable logic controller (PLC), and powered
by 120 VAC, determines the frequency (off time) and duration (on time) of the RO system water
dispensing cycles:
•
The GD designed program is downloaded to the PLC via an RS485 port and is stored in a
non-volatile EEPROM memory to end battery failure worries.
•
The “off” cycles are adjustable in 1, 2, 3, 5 and 7day intervals, and the “on” cycles are
adjustable to a 3 or 5 minute. intervals, but are typically set to 3 days “off”/3 minute. “on”
cycles.
•
A short test mode, 10 seconds “off”/5 seconds “on”, is provided to check the timer
operation.
•
Two additional cycles are provided to initially fill the reservoir with water in the field: 4 hour
and 8 hour “on” cycles. These cycles allow the field user to fill the reservoir unattended –
at the end of the “on” period, the cycle freezes in time until the mode switch is toggled off/on
again.
•
The setting of the cycles is accomplished via wire jumpers between PLC terminals 4, 5,
6, 7, and 9 – See Figure 8-1, page 46, for details.
•
An external switch is provided to execute the program in memory (run mode) or to halt and/or
allow the loading of programming (stop mode).
•
The external switch, when toggled from “stop” to “run”, resets the time counter to 0 and
initiates the “on” cycle first. This is particularly helpful when using one of the two fill cycles
during initial package commissioning.
•
At power-up, the timing sequence starts with the “off” cycle first. If the program execution is
halted via the external “run/stop” mode switch, the cycle under operation is “frozen” in time
until the switch is set back to “run”.
•
During the “on” cycle, whenever the compressor is running, the “fill” relay and the water fill
solenoid valve are energized and the water stored in the holding tank is admitted into the
package water system via the compressor intake.
•
During the “on” cycle, whenever the compressor is stopped, the dump solenoid valve is
energized and the water stored in the holding tank is evacuated via the package drain tube-
works.
•
When the water level in the package receiver reaches a high level, the package high level
float switch triggers the package ES controller to dump the excess water mass via the
package drain valve.
Содержание PUREAIR EWC99C
Страница 7: ...13 11 607 Page 2 Figure 1 2 PACKAGE ILLUSTRATION 307EWC797 B Ref Drawing...
Страница 8: ...13 11 607 Page 3 Figure 1 3 AIR WATER SCHEMATIC 308EWC797 F Ref Drawing...
Страница 25: ...13 11 607 Page 20 Figure 4 2 FLOW CHART FOR SETUP PROGRAMMING 300EWC1255 Ref Drawing...
Страница 38: ...13 11 607 Page 33 Figure 4 4 WIRING DIAGRAM FULL VOLTAGE 305EWC546 B Ref Drawing Page 1 of 2...
Страница 39: ...13 11 607 Page 34 305EWC546 B Ref Drawing Page 2 of 2...
Страница 40: ...13 11 607 Page 35 Figure 4 5 WIRING DIAGRAM FULL VOLTAGE LESS STARTER 306EWC546 B Ref Drawing Page 1 of 2...
Страница 41: ...13 11 607 Page 36 306EWC546 B Ref Drawing Page 2 of 2...