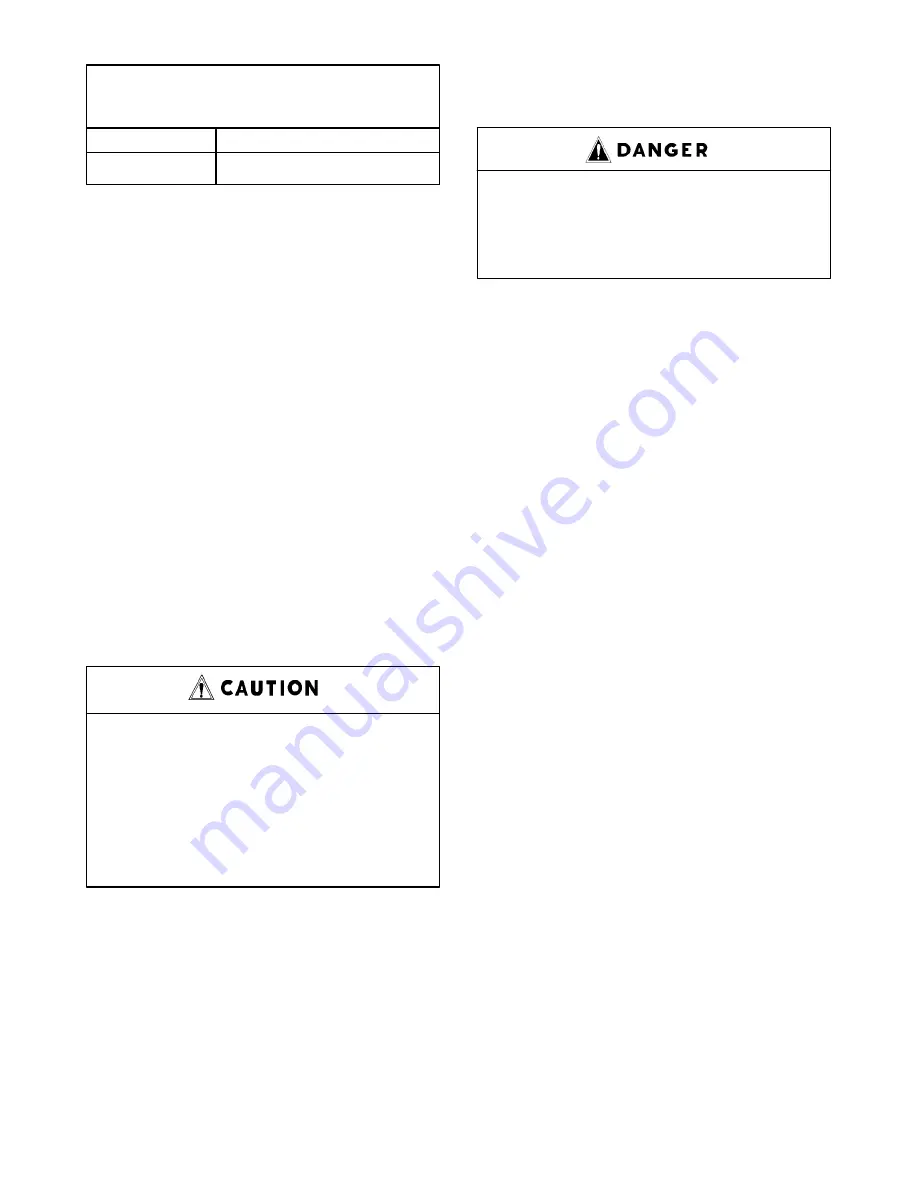
13–8–610 Page 10
* 80
o
F (27
_
C) Inlet Air
FIGURE 2–2 – AIR FLOW CHART
Minimum Air Flow* For Compressor
And Cooling – Cubic Feet/Minute
(Cubic Meters/Minute)
Air Cooled
All Models
6500 cfm (184 M
3
/min.)
FOUNDATION – The Electra–Screw
R
compressor re-
quires no special foundation, but should be mounted on
a smooth, solid surface. Whenever possible install the
unit near level. Temporary installation may be made at
a maximum 10
o
angle lengthwise or 10
o
sidewise.
Mounting bolts are not normally required. However,
installation conditions such as piping rigidity, angle of
tilt, or danger of shifting from outside vibration or mov-
ing vehicles may require the use of mounting bolts and
shims to provide uniform support for the base. Belt
alignment and tension should be checked after installa-
tion. (For information on belt alignment and tension see
Section 7, page 37.)
OIL RESERVOIR DRAIN – The oil drain is piped from
the bottom of the reservoir to the side of the frame. This
drain is approximately 2 inches (50 mm) above the floor
level. If this is not sufficient to conveniently drain the oil
some other methods of providing drain are:
1.
Elevate the compressor unit on a suitable struc-
ture to obtain the desired drain height.
If the compressor unit base is raised
above floor level, the space between
the floor and the base bottom must be
closed with solid material all around
to prevent recirculation of hot air from
the oil cooler end and over tempera-
ture operation.
2.
Construct an oil sump or trough below the floor
level and pump or bail the drained oil.
3.
Pump oil from the reservoir filler opening or drain
to a container.
ENCLOSURE – The compressor, electric motor, oil
cooler and aftercooler are mounted inside the enclo-
sure. Service doors are provided for maintenance ac-
cess. Be sure to allow enough space around the unit
for the doors to open completely. Any of the enclosure
doors may be removed by opening the door and lifting
it up slightly to disengage the hinges.
Do not operate the compressor with
the fan and belt guard removed. Ex-
posed fan and belts may cause injury
to personnel.
The motor inspection/air filter service panel is held by
two latches and lifts away from the enclosure. The air
outlet panel is attached by screws to the enclosure and
is not readily removeable.
INSTALLATION FOR COLD WEATHER OPERA-
TION (FIGURE 2–3) – It is recommended that the unit
be installed inside a shelter that will be heated to tem-
peratures above freezing (32
_
F, 0
_
C). This will elimi-
nate many of the problems associated with operating
units in cold climates, such as freezing in control lines
and downstream of the cooler.
Refer to Engineering Data Sheet 13–9–411 for the ad-
vantages of using the heat recovered from rotary com-
pressors. This heat recovery could easily pay for an ad-
equate shelter for the unit.
When an outside installation must be made, the pre-
cautions required will depend on the severity of the en-
vironment. The following are general guidelines for
outside installations:
Cold Weather (Down To +10
_
F, –12
_
C)
1.
Be sure all drains, traps, and control lines, includ-
ing pressure transducer lines are heated to avoid
freezing of condensate. Heat tape with thermo-
stat control is generally satisfactory for this pur-
pose and can be obtained at various local plumb-
ing or hardware outlets at nominal cost.
2.
If an air–cooled aftercooler is to be used, provi-
sions to bypass the aftercooler must be made.
Since cold air contains very little moisture, suc-
cessful operation can be achieved without the af-
tercooler.
3.
Provide at least some simple shelter such as a ply-
wood windbreak to protect against drifting snow.
4.
Use only Gardner Denver
R
AEON
t
9000 SP lu-
bricant.
5.
Monitor the unit carefully during start–up and op-
eration to be sure it is functioning normally.
6.
Specify NEMA 4 enclosure for electrical devices.
Содержание ELECTRA-SCREW EDEQHH
Страница 10: ...13 8 610 Page 2 200EDE797 Ref Drawing FIGURE 1 2 PACKAGE MINIMUM PRESSURE CHECK VALVE MIXING VALVE OIL FILTER...
Страница 11: ...13 8 610 Page 3 200EDE797 Ref Drawing FIGURE 1 3 PACKAGE OIL LEVEL GAUGE SEPARATOR AIR FILTER...
Страница 12: ...13 8 610 Page 4 202EDE797 Ref Drawing FIGURE 1 4 PACKAGE CONTROLLER STARTER BOX...
Страница 15: ...13 8 610 Page 7 DECALS 206EAQ077 212EAQ077 218EAQ077 211EAQ077 207EAQ077...
Страница 16: ...13 8 610 Page 8 DECALS 216EAQ077 217EAQ077 222EAQ077 221EAQ077 208EAQ077...
Страница 33: ...13 8 610 Page 25 FIGURE 4 10 WIRING DIAGRAM FULL VOLTAGE DUAL CONTROL 204EDE546 Ref Drawing...
Страница 34: ...13 8 610 Page 26 FIGURE 4 11 WIRING DIAGRAM WYE DELTA 205EDE546 Ref Drawing...
Страница 53: ......