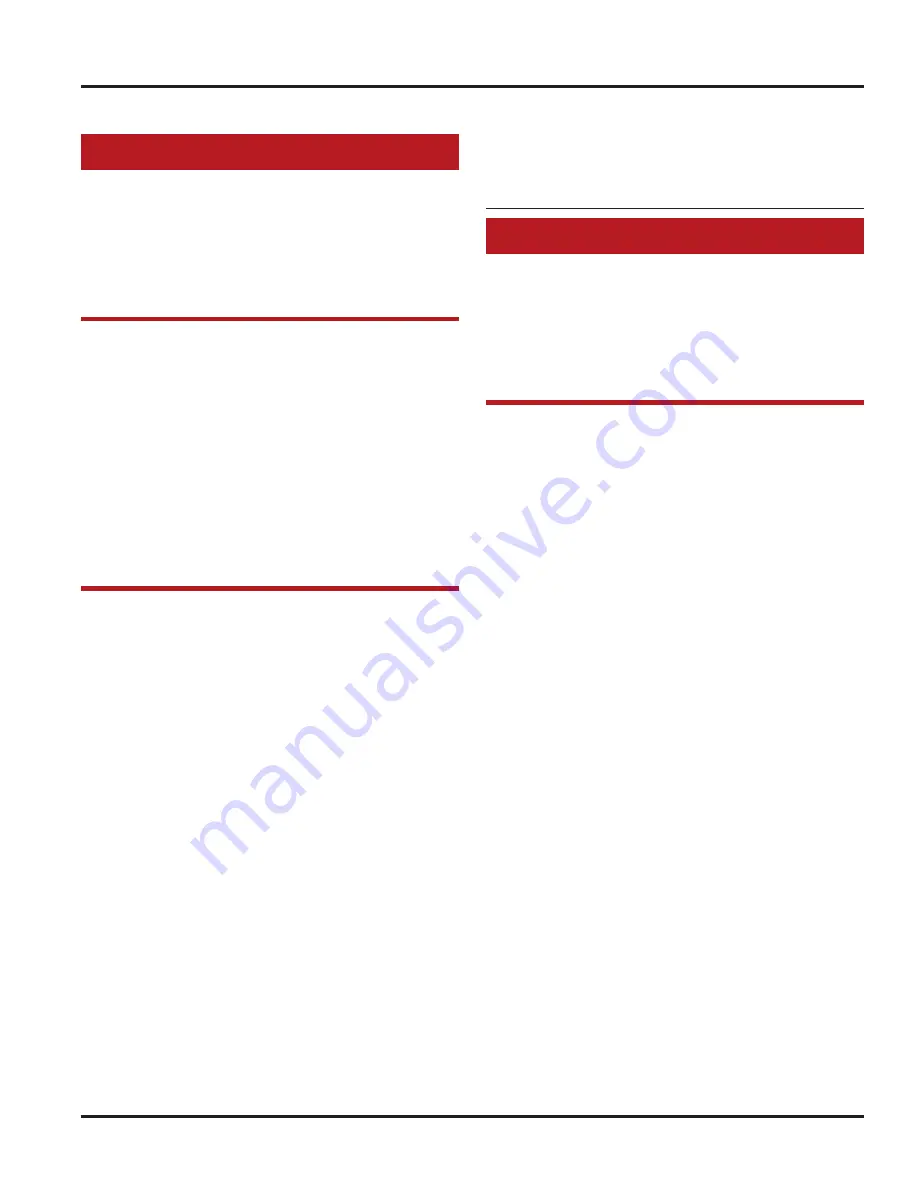
OPERATION - 3
Questions? Call (315) 298-5121, or visit us online at www.fulton.com
3-5
VSRT_IOM_2018-1213
SIEMENS LMV3 CONTROLLER NAVIGATION
!
WARNING
This information is for reference purposes only.
Fulton Companies is not responsible for this product,
including (but not limited to) its accuracy, reliability,
and safety. No Fulton document should substitute
for full review of documentation available from the
product manufacturer.
Perform the following steps once you have completed
first-time programming of the Siemens LMV3:
Note:
Fulton recommends use of the flame programmer
manual/Quick Start Guide when performing any
changes on the unit flame programmer.
1. Press and hold the F and A buttons
simultaneously. You will be prompted for your
password (####).
Note: #### is the last four digits of the national board
number.
2. Enter your password and press the “Enter”
button.
3. Using the “–” button, scroll to parameter level
100.
4. To enter into a parameter level and start
programming, press the enter button.
5. Use the “+” and “-” buttons to scroll through the
parameters.
6. Press the enter button to enter the parameter.
The current value will start flashing.
7. Use the “–” button to decrease the value or “+”
button to increase the value.
8. Once the desired value has been set, press the
“Enter” button. The number will stop flashing.
9. Press the “–” and “+” buttons together to back out
of the parameter level when finished.
10. Press the “–” or “+” buttons to scroll to the next
section of the program.
11. Repeat this process until all parameters have
been reviewed and set.
12. Once the parameters have been programmed,
back out to the front screen by pressing the –
and + buttons together.
Commissioning the Unit
!
WARNING
This information is for reference purposes only.
Fulton Companies is not responsible for this product,
including (but not limited to) its accuracy, reliability,
and safety. No Fulton document should substitute
for full review of documentation available from the
product manufacturer.
Perform the following steps for commissioning the unit
with the Siemens LMV3:
Note
: A combustion analyzer will be needed when
performing changes to the profile. Combustion settings
should only be adjusted by a qualified factory trained
and certified technician.
1. Press and hold the “F” and “A” buttons
simultaneously. You will be prompted for your
password (####).
OTE:
ote: #### is the last four digits of the national
board number.
2. Enter your password and press the “Enter”
button.
3. Using the “+” or “–” button, scroll to parameter
level 400. Press the “Enter” button. RUN will
appear. Press the enter button again.
4. Turn the boiler on and make sure that there
is a call for heat. PH12 means the unit is in
standby and is looking for a call for heat to start.
The unit should start to Pre-purge (PH22) and
drive to 100% purge (PH24), then begin purge
countdown in PH30.
5. Once the control has reached the Ignition
Position (PH36), press the “+” button. This will
allow the boiler to ignite the pilot flame. Once
the pilot is established, the boiler will transfer to
main flame.
6. You will be at P0. P0 is the start of the profile and
the Ignition position.
Содержание VSRT 10
Страница 2: ......
Страница 5: ...1 1 Section Safety Warnings 1 Installation 2 Operation 3 Maintenance Troubleshooting 4 Warranty 5...
Страница 11: ...2 1 Section Safety Warnings 1 Installation 2 Operation 3 Maintenance Troubleshooting 4 Warranty 5...
Страница 44: ...2 INSTALLATION Fulton 2018 2 34 VSRT_IOM_2018 1213...
Страница 45: ...3 1 Section Safety Warnings 1 Installation 2 Operation 3 Maintenance Troubleshooting 4 Warranty 5...
Страница 61: ...4 1 Section Safety Warnings 1 Installation 2 Operation 3 Maintenance Troubleshooting 4 Warranty 5...
Страница 88: ...5 1 Section Safety Warnings 1 Installation 2 Operation 3 Maintenance Troubleshooting 4 Warranty 5 Parts 6...
Страница 89: ...5 WARRANTY Fulton 2018 5 2 VSRT_IOM_2018 1213...