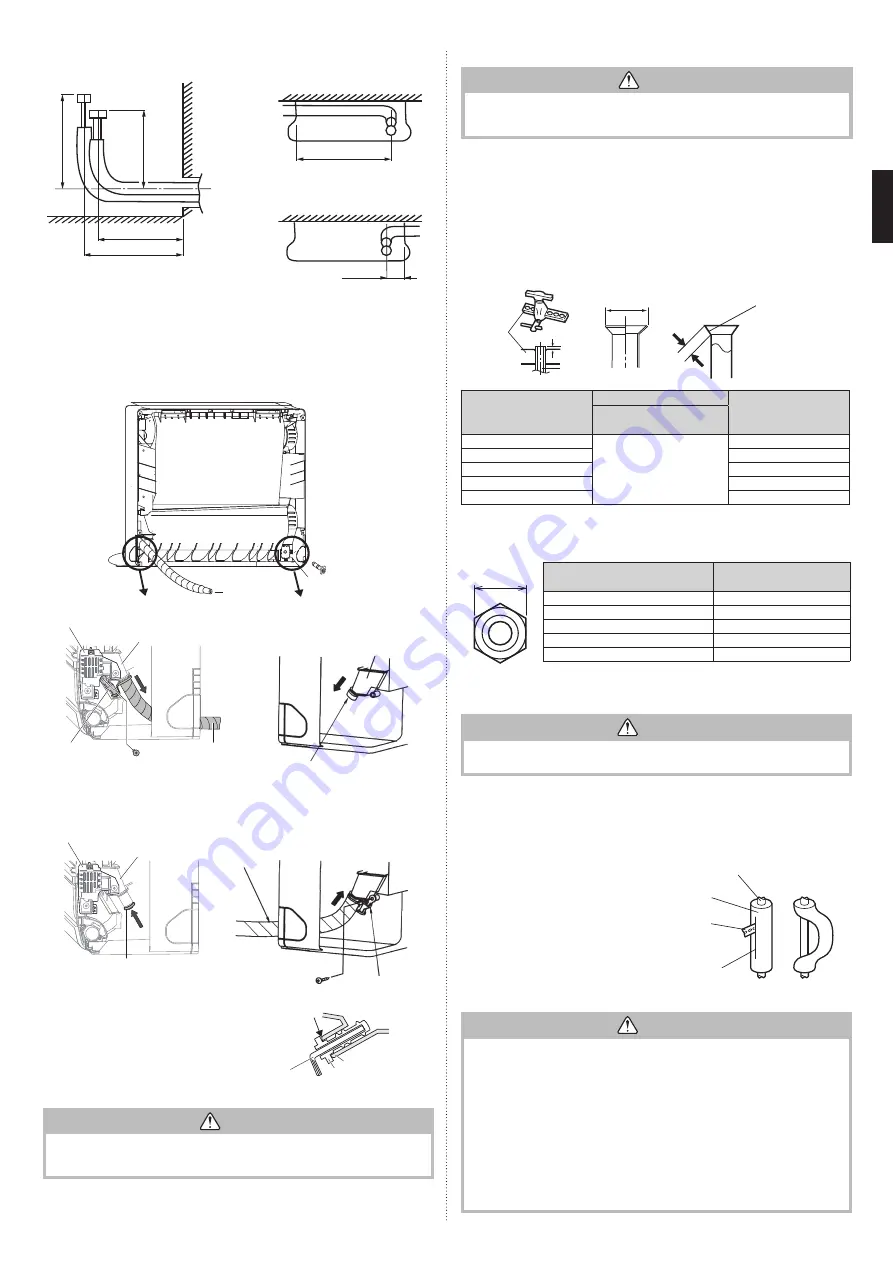
En-7
■
Rear piping
■
Left piping
Center of
wall hole
130 mm
Floor
280 mm
245 mm
Back wall
100 mm
Back wall
690 mm
■
Right piping
30 mm
Back wall
■
Left and right replacement of drain hose
The drain hose can be connected at either side of the indoor unit.
The unit has been shipped with the drain hose connected at left (viewed from the back of
the unit) and the drain cap applied at right.
(1) Remove the both side panels.
(2) Remove the screw and remove the drain holder from drain pan.
(3) Pull out the drain cap.
(4) Connect the drain hose to the right, attach the screw and insert the drain cap to the left.
Drain
hose
Drain cap
Drain pan
Drain hose
Drain holder
Screw
Drain pan
Drain cap
Refrigerant leakage sensor
NOTE:
When attaching/removing the drain holder and drain hose on the refrigerant leak-
age sensor side, be very careful not to give a shock to the sensor.
Drain holder
Drain hose
Screw
Drain cap
Drain pan
Refrigerant leakage sensor
■
Installation method of Drain cap
Use a hexagonal wrench (4 mm at opposite side)
to insert the drain cap, till the drain cap contacts
the tip of drain cook.
No gap
Drain cock
Drain cap
Hexagon
wrench
CAUTION
Insert the drain hose and drain cap into the drain port, making sure that it comes
in contact with the back of the drain port, and then mount it. If the drain hose is not
connected properly, leaking will occur.
3.3.6. Pipe connection
CAUTION
Tighten the flare nuts with a torque wrench using the specified tightening method.
Otherwise, the flare nuts could break after a prolonged period, causing refrigerant to
leak and generate hazardous gas if the refrigerant comes into contact with a flame.
■
Flaring
Use special pipe cutter and flare tool designed for R410A or R32 pipework.
(1) Cut the connection pipe to the necessary length with a pipe cutter.
(2) Hold the pipe downward so that cuttings will not enter the pipe and remove any burrs.
(3) Insert the flare nut (always use the flare nut attached to the indoor unit(s) and outdoor
unit or branch box respectively) onto the pipe and perform the flare processing with a
flare tool. Use the special R410A or R32 flare tool, or the conventional flare tool. Leak-
age of refrigerant may result if other flare nuts are used.
(4) Protect the pipes by pinching them or with tape to prevent dust, dirt, or water from
entering the pipes.
Die
A
Pipe
B
L
Check if [L] is flared uniformly
and is not cracked or scratched.
Pipe outside diameter
[mm (in.)]
Dimension A [mm]
Dimension B [mm]
Flare tool for R32,
clutch type
6.35 (1/4)
0 to 0.5
9.1
9.52 (3/8)
13.2
12.70 (1/2)
16.6
15.88 (5/8)
19.7
19.05 (3/4)
24.0
When using conventional flare tools to flare R32 pipes, the dimension A should be approx-
imately 0.5 mm more than indicated in the table (for flaring with R32 flare tools) to achieve
the specified flaring. Use a thickness gauge to measure the dimension A.
Width across
flats
Pipe outside diameter
[mm (in.)]
Width across flats
of flare nut [mm]
6.35 (1/4)
17
9.52 (3/8)
22
12.70 (1/2)
26
15.88 (5/8)
29
19.05 (3/4)
36
NOTE:
The flare nut specification is compliant with ISO14903.
■
Bending pipes
CAUTION
• To prevent breaking of the pipe, avoid sharp bends.
• If the pipe is bent repeatedly at the same place, it will break.
• The pipes are shaped by your hands. Be careful not to collapse them.
• Bend R70 mm or more with a pipe bender.
• Do not bend the pipes in an angle more than 90°.
• When pipes are repeatedly bend or stretched, the material will harden, making it difficult
to bend or stretch them anymore.
• Do not bend or stretch the pipes more than 3 times.
•
When bending the pipe, do not bend it as
is. The pipe will be collapsed. In this case,
cut the insulating pipe with a sharp cutter as
shown on the right, and bend it after expos-
ing the pipe. After bending the pipe as you
want, be sure to put the heat insulating pipe
back on the pipe, and secure it with tape.
Pipe
Insulating
pipe
Cutter
Cut line
■
Flare connection
CAUTION
• Be sure to install the pipe against the port on the indoor unit correctly. If the center-
ing is improper, the flare nut cannot be tightened smoothly. If the flare nut is forced
to turn, the threads will be damaged.
• Do not remove the flare nut from the indoor unit pipe until immediately before con-
necting the connection pipe.
• Hold the torque wrench at its grip, keeping it in the right angle with the pipe, in order
to tighten the flare nut correctly.
• Tighten the flare nuts with a torque wrench using the specified tightening method.
Otherwise, the flare nuts could break after a prolonged period, causing refrigerant to
leak and generate hazardous gas if the refrigerant comes into contact with a flame.
• Connect the piping so that the control box cover can easily be removed for servic-
ing when necessary.
• In order to prevent water from leaking into the control box, make sure that the pip-
ing is well insulated.
9378533080-04_IM.indb 7
9378533080-04_IM.indb 7
2022/2/14 15:13:14
2022/2/14 15:13:14