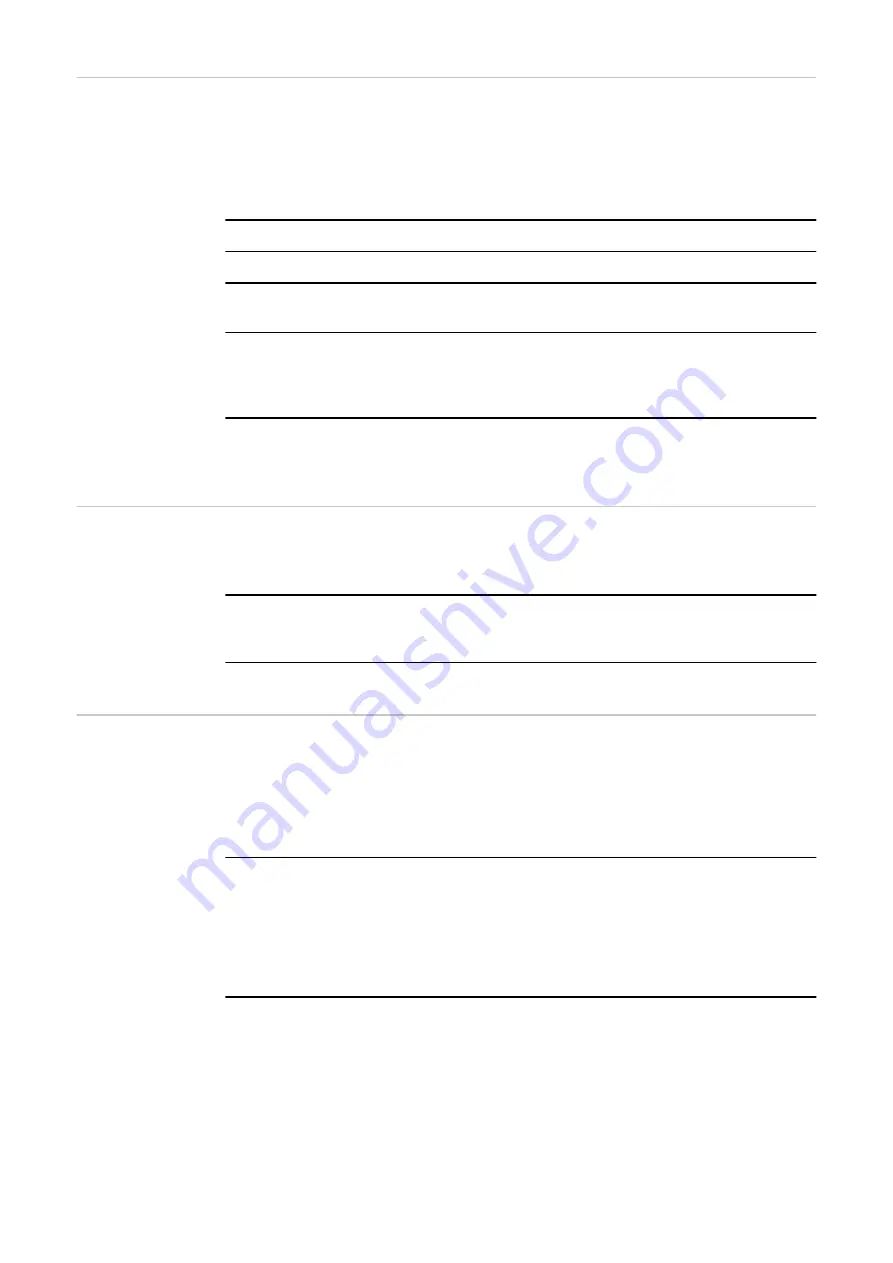
Meandering weld-
ing currents
If the following instructions are ignored, meandering welding currents can develop with
the following consequences:
-
Fire hazard
-
Overheating of parts connected to the workpiece
-
Damage to ground conductors
-
Damage to device and other electrical equipment
Ensure that the workpiece is held securely by the workpiece clamp.
Attach the workpiece clamp as close as possible to the area that is to be welded.
Position the device with sufficient insulation against electrically conductive environments,
such as insulation against conductive floor or insulation to conductive racks.
If power distribution boards, twin-head mounts, etc., are being used, note the following:
The electrode of the welding torch / electrode holder that is not used is also live. Make
sure that the welding torch / electrode holder that is not used is kept sufficiently insu-
lated.
In the case of automated MIG/MAG applications, ensure that only an insulated wire elec-
trode is routed from the welding wire drum, large wirefeeder spool or wirespool to the
wirefeeder.
EMC Device Clas-
sifications
Devices in emission class A:
-
Are only designed for use in industrial settings
-
Can cause line-bound and radiated interference in other areas
Devices in emission class B:
-
Satisfy the emissions criteria for residential and industrial areas. This is also true for
residential areas in which the energy is supplied from the public low-voltage mains.
EMC device classification as per the rating plate or technical data.
EMC measures
In certain cases, even though a device complies with the standard limit values for emis-
sions, it may affect the application area for which it was designed (e.g. when there is
sensitive equipment at the same location, or if the site where the device is installed is
close to either radio or television receivers).
If this is the case, then the operator is obliged to take appropriate action to rectify the
situation.
Check and evaluate the immunity to interference of nearby devices according to national
and international regulations. Examples of equipment that may be susceptible to interfer-
ence from the device include:
-
Safety devices
-
Network, signal and data transfer lines
-
IT and telecommunications devices
-
Measuring and calibrating devices
Supporting measures for avoidance of EMC problems:
1.
Mains supply
-
If electromagnetic interference arises despite the correct mains connection, ad-
ditional measures are necessary (e.g. use of a suitable line filter)
2.
Welding power-leads
-
must be kept as short as possible
-
must be laid close together (to avoid EMF problems)
-
must be kept well apart from other leads
3.
Equipotential bonding
10
Содержание CU 1100i
Страница 2: ......
Страница 16: ...16...
Страница 17: ...General information 17...
Страница 18: ...18...
Страница 26: ...26...
Страница 27: ...Connections and mechanical com ponents 27...
Страница 28: ...28...
Страница 31: ...Installation and commissioning 31...
Страница 32: ...32...
Страница 45: ...Close the cover on the cooling unit connection 3 45 EN...
Страница 46: ...46...
Страница 47: ...Troubleshooting 47...
Страница 48: ...48...
Страница 53: ...Care maintenance and disposal 53...
Страница 54: ...54...
Страница 70: ...70...
Страница 71: ...Technical data 71...
Страница 72: ...72...
Страница 82: ...82...
Страница 83: ...83 EN...