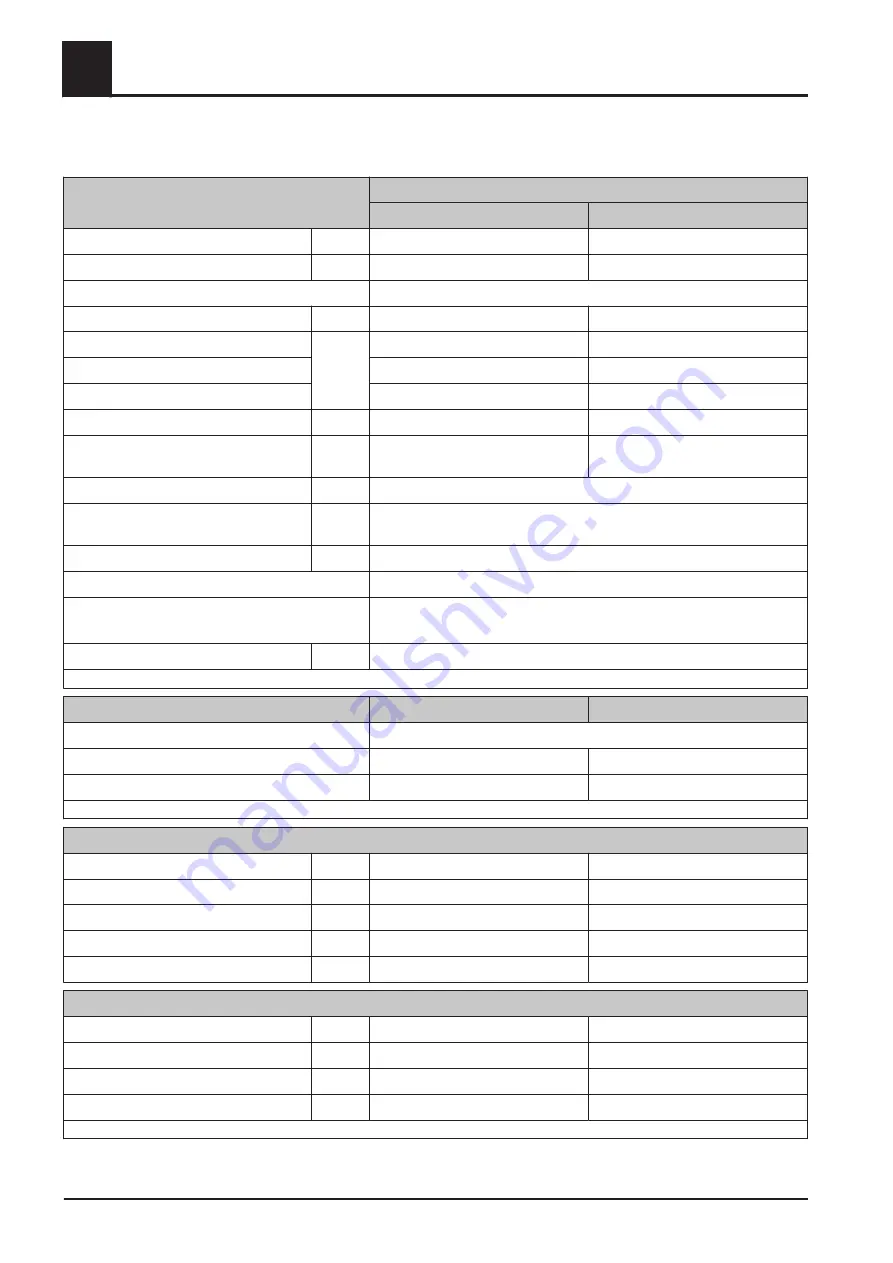
3.3 Technical specifications
Description
TM
400
500
Nominal heat output
kW
399
499
Heat output range
kW
119-399
149-499
Electrical connection
400 V / 50 Hz / 35 A or as per circuit diagram
Power consumption (pellets, wood chip)
kW
1.38 / 1.75
1.57 / 2.08
Total weight incl. fittings
kg
8,400
8,400
Weight - combustion chamber
2,200
2,200
Weight - heat exchanger
2,150
2,150
Heat exchanger water capacity
l
750
750
Water pressure drop
(ΔT = 10 / 20 K)
mbar
14.3 / 5.6
19 / 8.5
Minimum boiler return temperature
°C
65
Maximum permitted operating tempera‐
ture
°C
90
Permitted operating pressure
bar
6
Boiler class as per EN 303-5:2012
5
Permitted fuel as per EN 14961
1)
Part 2: Wood pellets class A1 / D06
Part 4: Wood chips class A2 / P16A-P45A
Airborne sound level
dB(A)
< 70
1.Detailed information on the fuel is included in the operating instructions in the section on “Permitted fuels”
400
500
Testing institute
TÜV Austria
1)
Test report no.
11-UW/Wels-EX-177/5
11-UW/Wels-EX-177/1
Date of issue
20/03/2012
18/09/2011
1.TÜV Austria Services GmbH, Geschäftsbereich Umweltschutz, Am Thalbach 15, A-4600 Thalheim/Wels
Test data for wood chips - emissions in [mg/MJ] (nominal load/partial load)
Carbon monoxide (CO)
mg/MJ
9 / 4
<2 / 4
Nitrogen oxide (NOx)
mg/MJ
44 / 51
46 / 51
Organic hydrocarbons (OGC)
mg/MJ
<1 / <2
<1 / <2
Dust
mg/MJ
15 / 11
18 / 11
Boiler efficiency
%
93.9 / 90.3
93.6 / 90.3
Test data for wood chips - emissions in [mg/m³]
1)
(nominal load/partial load)
Carbon monoxide (CO)
mg/m³
14 / 5
<2 / 5
Nitrogen oxide (NOx)
mg/m³
65 / 76
67 / 76
Organic hydrocarbons (OGC)
mg/m³
<1 / <3
<1 / <3
Dust
mg/m³
22 / 16
26 / 16
1.Emissions values based on dry flue gas at standard temperature and pressure (0°C, 1,013 mbar) with a volume content of oxygen of 13%
3
Technology
Technical specifications
14
Fröling GesmbH | 4710 Grieskirchen, Industriestraße 12 | www.froeling.at