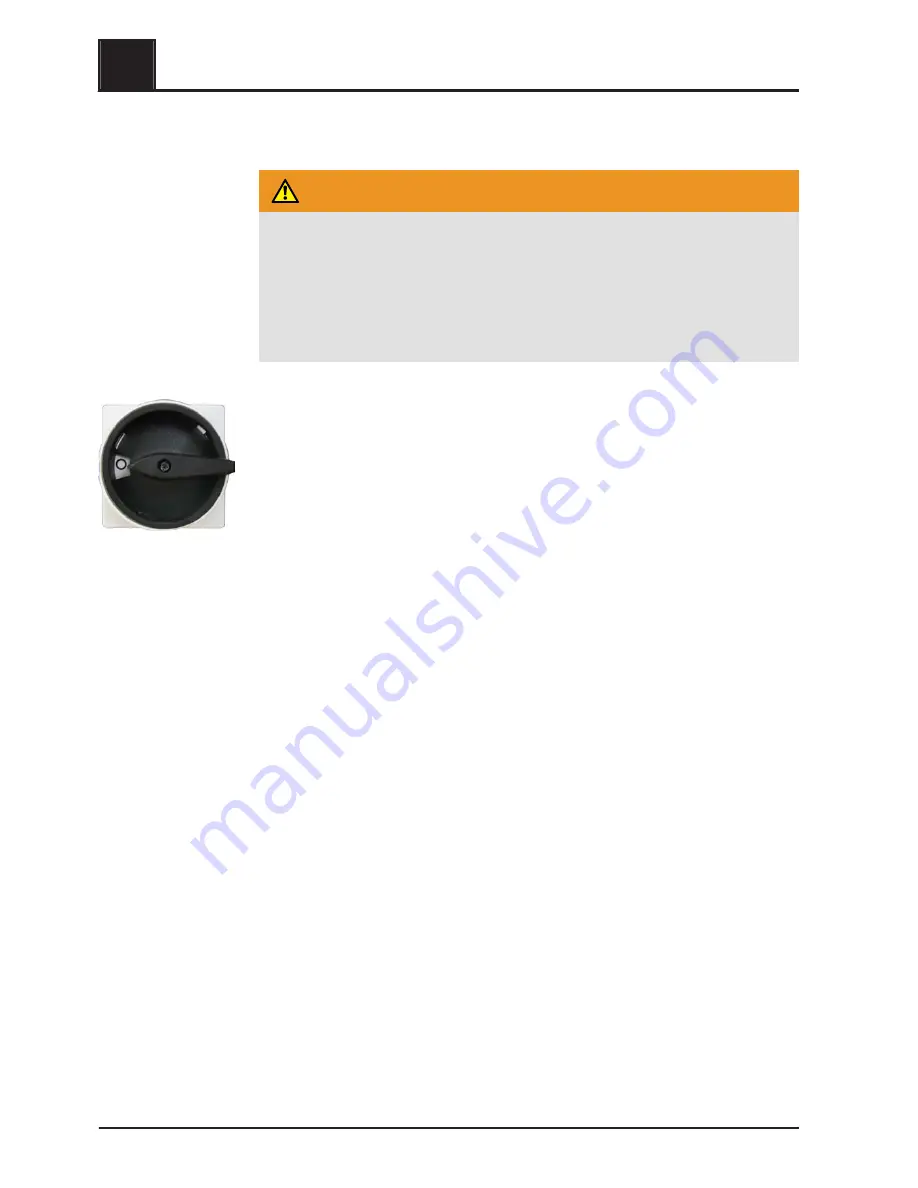
3.3.5 Switching off the power supply
WARNING
When turning off the main switch in automatic mode:
Serious combustion faults leading to serious accidents are possible.
Before turning off the main switch:
❒ Switch boiler off by tapping “Boiler OFF”
➥ The boiler follows the shutdown procedure and switches to "Switched off
OFF“ status after the cleaning cycle
❒ Turn off the main switch
➥ Boiler controller is switched off
➥ The components powered via the control cabinet are powered down
➥ CAUTION: the expansion switch cabinet, which has its own power supply, is
still live.
NOTICE! Frost protection function is no longer active!
3
Operating the system
Heating up the boiler
32
Froling GesmbH | A-4710 Grieskirchen, Industriestraße 12 | www.froeling.com