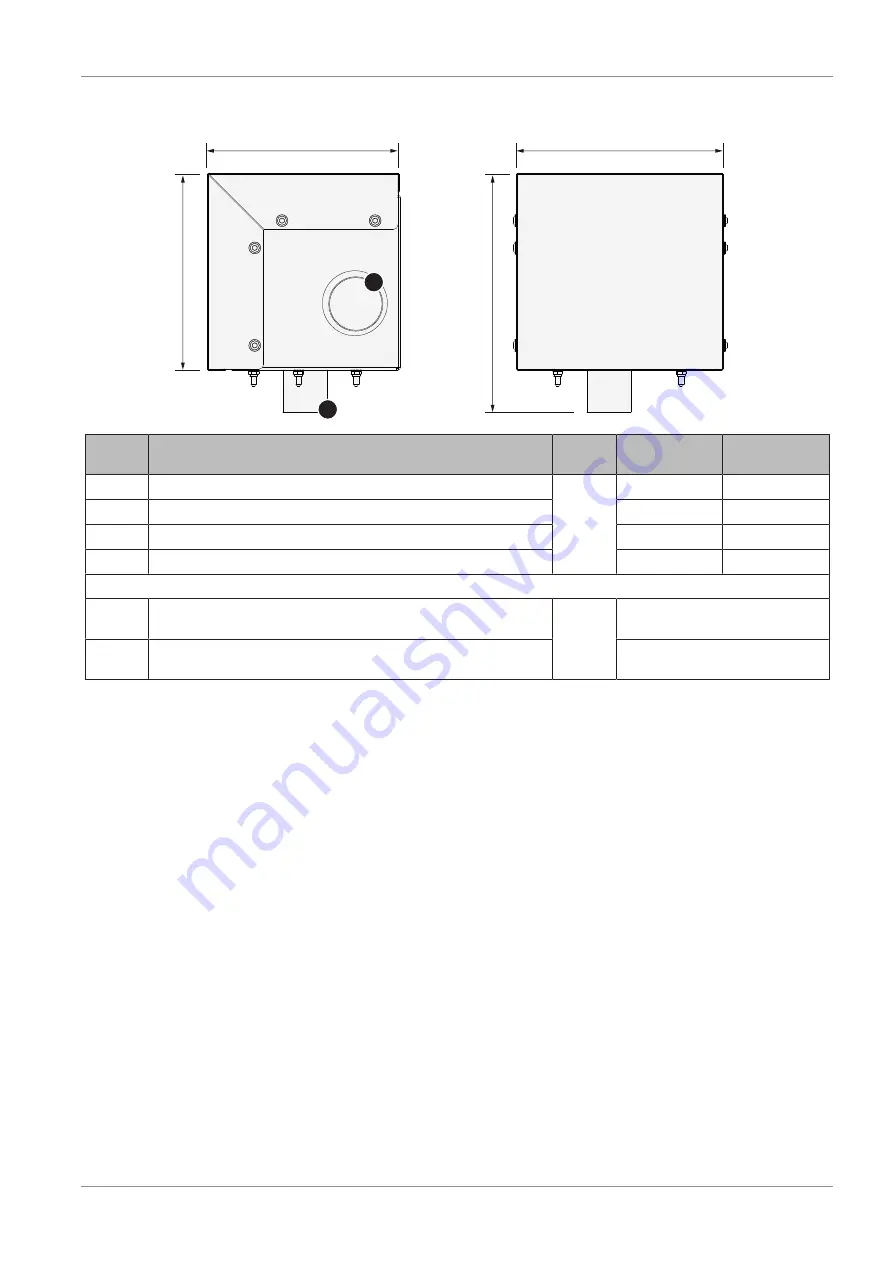
Technical information | 4
M1820921_en | Installation instructions Dual fuel boiler SP Dual compact
23
4.4 External suction module
B1
H1
H2
L1
1
2
Dimensi
on
Description
Unit
Size 1
Size 2
L1
Length of suction module
mm
220
265
B1
Width of suction module
235
290
H1
Height of suction module
225
235
H2
Total height incl. hose connection
275
285
1
Return-air line connection
(line to suction point)
mm
50
2
Return-air line connection
(line to boiler)
50