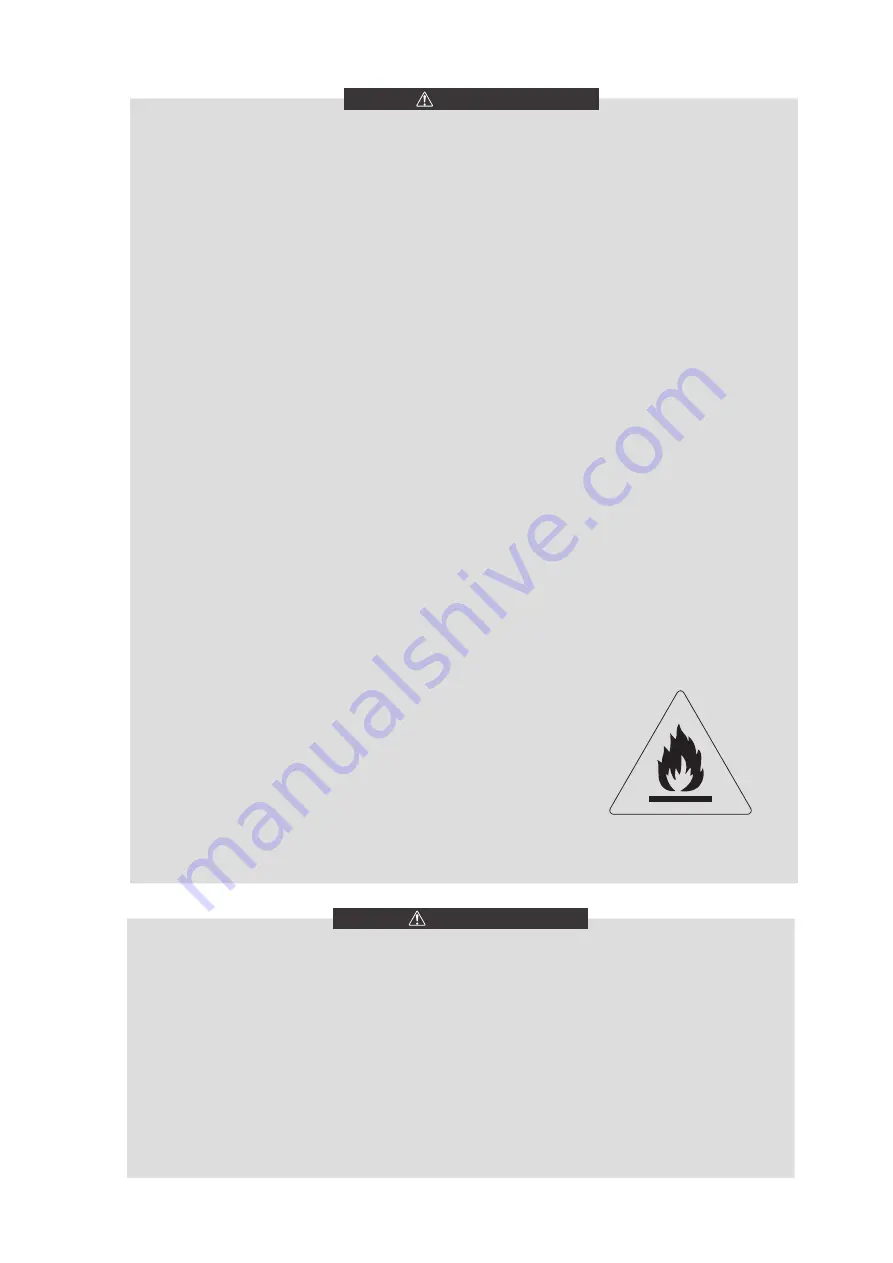
03
WARNING
CAUTION
• Servicing shall only be performed as recommended by the equipment manufacturer. Maintenance and repair
requiring the assistance of other skilled personnel shall be carried out under the supervision of the person
competent in the use of flammable refrigerants.
• Tear apart and throw away plastic packaging bags so that children will not play with them.Children playing with
plastic bags face danger.
• Safely dispose of packing materials such as nails and other metal or wood parts that could cause injuries.
• Ask your dealer or qualified personnel to perform installation work in accordance with this manual. Do not install
the unit yourself. Improper installation could result in water leakage, electric shocks or fire.
• Be sure to use only specified accessories and parts for installation work. Failure to use specified parts may
result in water leakage, electric shocks, fire, or the unit falling from its mount.
• Install the unit on a foundation that can withstand its weight. Insufficient physical strength may cause the
equipment to fall and possible injury.
• Perform specified installation work with full consideration of strong wind, hurricanes, or earthquakes. Improper
installation work may result in accidents due to equipment falling.
• Make certain that all electrical work is carried out by qualified personnel according to the local laws and
regulations and this manual using a separate circuit. Insufficient capacity of the power supply circuit or improper
electrical construction may lead to electric shocks or fire.
• Be sure to install a ground fault circuit interrupter according to local laws and regulations. Failure to install a
ground fault circuit interrupter may cause electric shocks and fire.
• Make sure all wiring is secure. Use the specified wires and ensure that terminal connections or wires are
protected from water and other adverse external forces. Incomplete connection or affixing may cause a fire.
• When wiring the power supply, form the wires so that the front panel can be securely fastened. If the front panel
is not in place there could be overheating of the terminals, electric shocks or fire.
• After completing the installation work, check to make sure that there is no refrigerant leakage.
• Never directly touch any leaking refrigerant as it could cause severe frostbite.Do not touch the refrigerant pipes
during and immediately after operation as the refrigerant pipes may be hot or cold, depending on the condition
of the refrigerant flowing through the refrigerant piping, compressor and other refrigerant cycle parts. Burns or
frostbite are possible if you touch the refrigerant pipes. To avoid injury, give the pipes time to return to normal
temperature or, if you must touch them, be sure to wear protective gloves.
• Do not touch the internal parts (pump, backup heater, etc.) during and immediately after operation. Touching the
internal parts can cause burns. To avoid injury, give the internal parts time to return to normal temperature or, if
you must touch them, be sure to wear protective gloves.
• Do not use means to accelerate the defrosting process or to clean, other
than those recommended by the manufacture.
• The appliance shall be stored in a room without continuously operating
ignition sources (for example: open flames, an operating gas appliance or
an operation electric heater.)
• Do not pierce or burn.
• Be aware that refrigerants may not contain an adour.
Caution: Risk of fire/
flammable materials
• Ground the unit.
• Grounding resistance should be according to local laws and regulations.
• Do not connect the ground wire to gas or water pipes, lightning conductors or telephone ground wires. Incomplete
grounding may cause electric shocks.
- Gas pipes
:
Fire or an explosion might occur if the gas leaks.
- Water pipes: Hard vinyl tubes are not effective grounds.
- Lightning conductors or telephone ground wires: Electrical threshold may rise abnormally if struck by a lightning
bolt.
• Install the power wire at least 3 feet (1 meter) away from televisions or radios to prevent interference or noise.
(Depending on the radio waves, a distance of 3 feet (1 meter) may not be sufficient to eliminate the noise.)
• Do not wash the unit. This may cause electric shocks or fire. The appliance must be installed in accordance with
national wiring regulations. If the supply cord is damaged, it must be replaced by the manufacturer, its service
agent or similarly qualified persons in order to avoid a hazard.