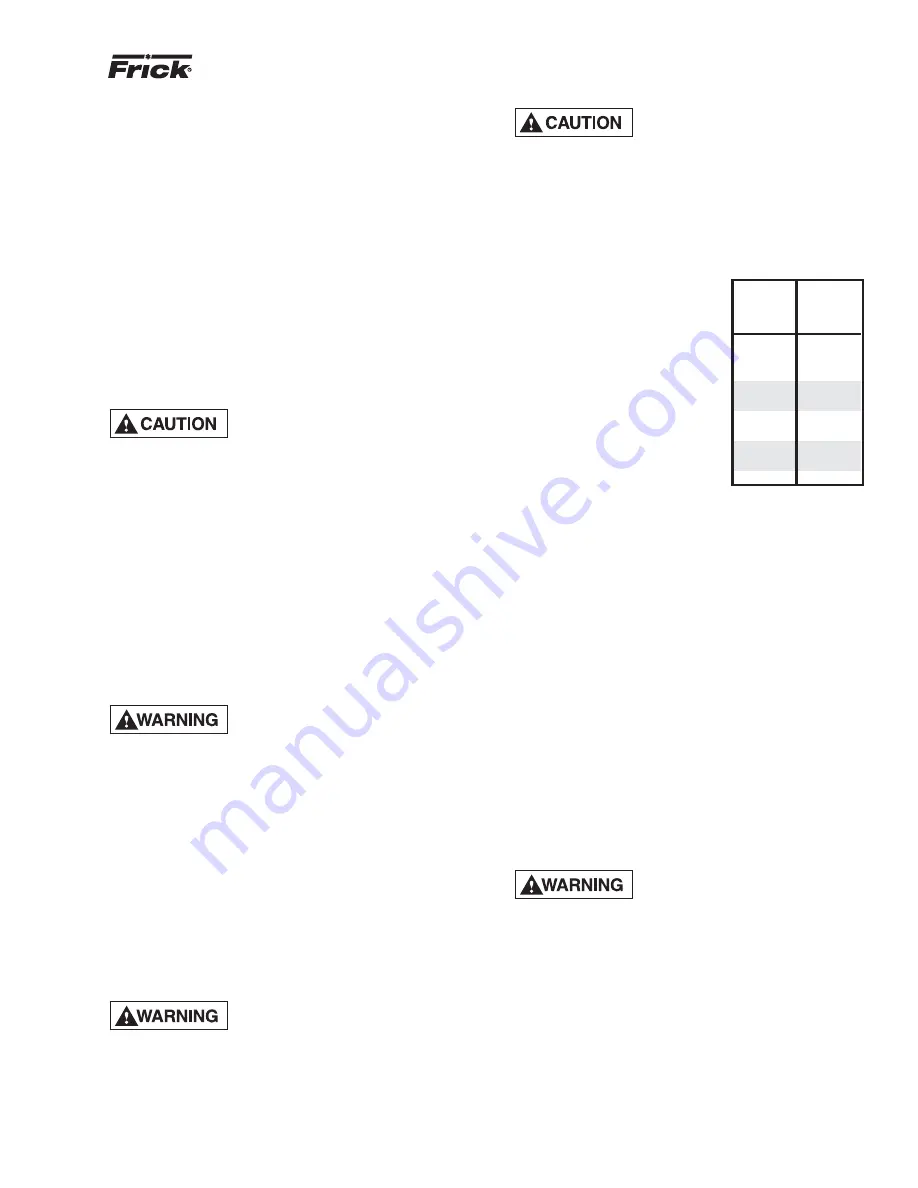
RWB II ROTARY SCREW COMPRESSOR UNITS
INSTALLATION
S70-200 IOM
Page 9
HOT ALIGNMENT OF COMPRESSOR/MOTOR
Hot alignments can only be made after the unit has op er at ed
for several hours and all components are at operating tem-
peratures.
Shut down the unit and quickly affi x dial indicator to cou pling
mo tor hub, then take readings of both the face and rim of the
compressor hub. If these readings are within tol er ance, record
reading, attach coupling guard and restart unit. How ev er, if
the reading is not within lim its, compare the hot read ing with
the cold alignment and adjust for this dif fer ence; i.e. if the
rim at 0° and 180° readings indicates that the motor rises
.005" between its hot and cold state, .005" of shims should
be re moved from under the motor.
After the initial hot alignment adjustment is made, restart unit
and bring to operating temperature. Shut down and re check
hot alignment. Repeat pro ce dure unit hot align ment is within
spec i fi ed tolerance.
I N S TA L L C O U
P L I N G G UA R D
B E F O R E O P E R AT I N G C O M -
PRES SOR.
OIL PUMP COUPLING
Compressor units with direct motor/pump cou pled pumps
need no pump/motor coupling alignment since this is main-
tained by the close-coupled arrangement.
HOLDING CHARGE AND STORAGE
Each RWB II compressor unit is pressure and leak tested at
the Frick factory and then thoroughly evacuated and charged
with dry nitrogen to ensure the integrity of the unit during
shipping and short term storage prior to installation.
NOTE: Care must be taken when entering the unit to
en sure that the nitrogen charge is safely released.
Holding charge shipping gauges
on separator and ex ter nal oil cool er
are rated for 30 PSIG and are for
check ing the ship ping charge only. They must be re-
moved before pressure testing the sys tem and before
charg ing the sys tem with re frig er ant. Failure to remove
these gaug es may result in cat a stroph ic fail ure of the
gauge and un con trolled re lease of re frig er ant re sult ing
in se ri ous in ju ry or death.
All units must be kept in a clean, dry location to prevent
cor ro sion dam age. Reasonable con sid er ation must be
giv en to proper care for the solid-state com po nents of the
mi cro pro ces sor.
Unit which will be stored for more than two months must have
the nitrogen charge checked periodically.
COMPRESSOR UNIT OIL
DO NOT MIX OILS of different
brands, manufacturers, or types.
Mix ing of oils may cause ex ces sive
oil foam ing, nuisance oil level cut outs, oil pressure
loss, gas or oil leakage and cat a stroph ic compressor
failure.
Use only Frick
®
refrigeration oil
and fi lters or warranty claims may
be denied.
The oil charge shipped with the unit is the best suited lu-
bri cant for the con di tions specifi ed at the time of pur chase.
If there is any doubt due to the refrigerant, operating pres-
sures, or temperatures, refer to Frick Pub. E160-802 SPC
for guid ance.
OIL CHARGE
The normal charging level is mid-
way in the top sight glass located
mid way along the oil sep a ra tor
shell. Normal op er at ing lev el is
mid way be tween the top sight
glass and bot tom sight glass.
The table gives the ap prox i mate oil
charge quan ti ty.
* Includes total in oil sep a ra tor and
pip ing. Additional oil supplied for
oil cool er.
Add oil by at tach ing the end of a
suitable-pressure-type hose to the
oil charging valve, lo cat ed on the
top of the oil sep a ra tor at the com pres sor end. Using a
pres sure-type pump and the rec om mend ed Frick oil, open
the charg ing valve and pump oil into the sep a ra tor. NOTE:
Fill slow ly be cause oil will fi ll up in the sep a ra tor faster
than it shows in the sight glass.
Oil distillers and similar equipment which act to trap oil must
be fi lled pri or to unit operation to nor mal design outlet lev els.
The same pump used to charge the unit may be used for
fi lling these auxiliary oil res er voirs.
NOTE: The sight glass located in the coalescing end
of the sep a ra tor near the discharge con nec tion should
re main empty.
OIL HEATER(S)
Standard units are equipped with two or three 500 watt oil
heat ers, providing suffi cient heat to maintain the oil tem-
per a ture for most indoor ap pli ca tions during shut down cy cles
to per mit safe start-up. Should ad di tion al heating capacity
be re quired be cause of low am bi ent tem per a ture, con tact
Frick. The heat ers are en er gized only when the unit is not
in op er a tion.
DO NOT ENERGIZE THE HEAT ERS
when there is no oil in the unit, the
heat ers will burn out. The oil heat-
ers will be en er gized when ev er 120 volt con trol pow er is
ap plied to the unit and the com pressor is not run ning,
un less the 16 amp circuit break er in the micro en clo sure
is turned off.
60
35
76
35
100
65
134
65
177
110
222
110
270
140
316
140
399
140
480
170
BASIC*
CHARGE
(gal.)
RWB II
MODEL
NO.
Содержание RWB II
Страница 43: ...RWB II ROTARY SCREW COMPRESSOR UNITS MAINTENANCE S70 200 IOM Page 43 P I DIAGRAM...
Страница 46: ...RWB II ROTARY SCREW COMPRESSOR UNITS MAINTENANCE S70 200 IOM Page 46 P I DIAGRAM LIQUID INJECTION BOOSTER...
Страница 50: ...RWB II PLUS ROTARY SCREW COMPRESSOR UNITS FORMS S70 200 IOM Page 50 OPERATING LOG SHEET...