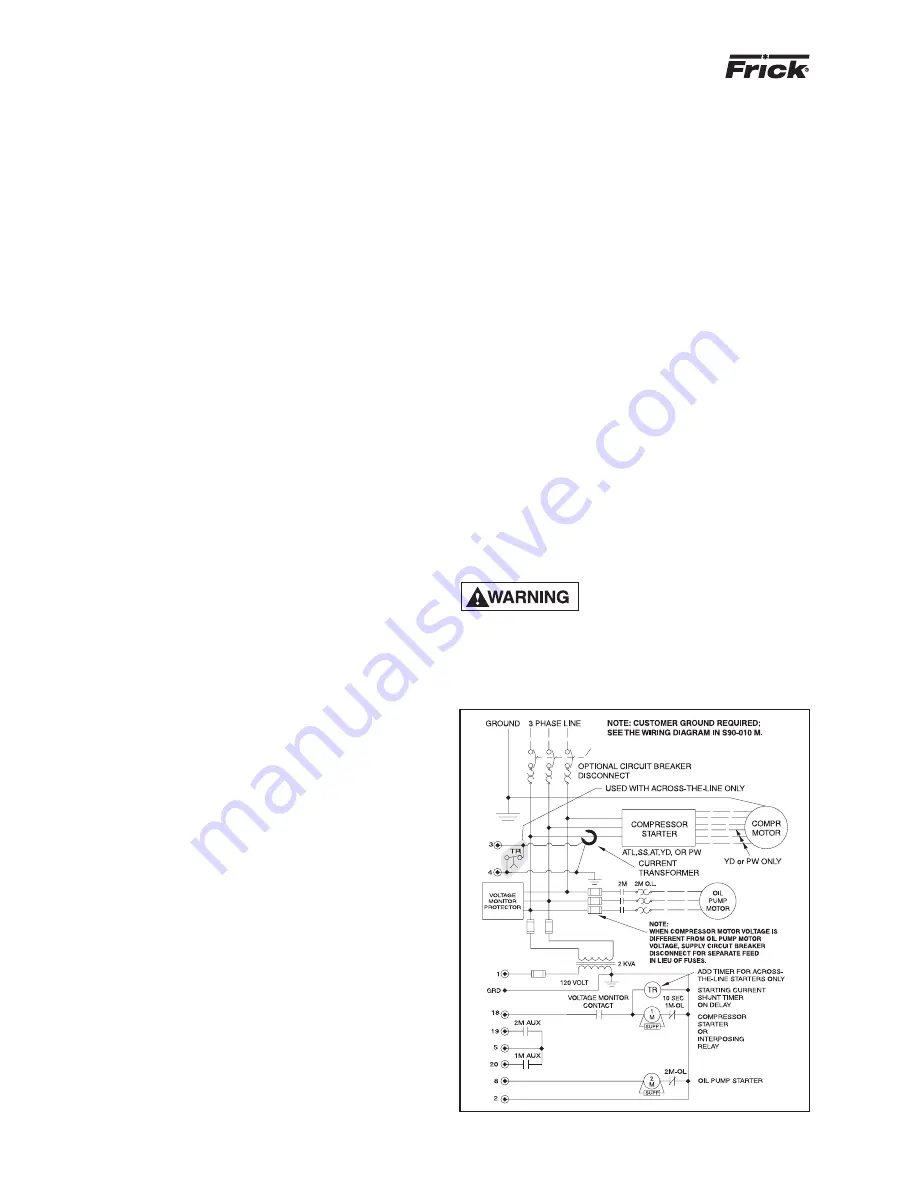
RWB II ROTARY SCREW COMPRESSOR UNITS
INSTALLATION
S70-200 IOM
Page 14
ECONOMIZER LOAD BALANCING
The most energy effi cient manner to operate an econ o miz er
system, when using multiple compressors on a com mon
economizer vessel, is to take as much of the fl ash gas as
possible to the compressors that are fully loaded. This can
be done in at least two ways.
1. Use the economizer output from the microprocessor to
turn off a solenoid, or to actuate the electric shutoff option
on a back-pressure regulator, based on percent of slide valve
travel. This will direct all the fl ash vapor to the other loaded
compressors.
2. A dual-setpoint back-pressure regulator valve can be used
in each of the individual econ o miz er vapor lines. When a com-
pressor is running near full load, the BPR valve will op er ate
on the desired setpoint, or basically wide open, to min i mize
pressure drop in the line. When one compressor un loads
below the slide valve position where the econ o miz er out put
on the mi cro pro ces sor turns on, the dual-set point fea ture of
the regulator can be actuated by this output to con trol the
pressure, on the vessel side of the regulator, to be a few psi
higher. Consequently, the fl ash gas will be sent to the loaded
compressors fi rst, until they can’t handle all the va por and
the pressure in the vessel starts to rise. Then, some of the
vapor will go to the unloaded com pres sor to help main tain
the vessel at the desired pressure. An ex am ple of a back-
pressure regulator with electric shutoff and the dual-setpoint
feature is an R/S A4ADS.
ELECTRICAL
NOTE: Before proceeding with electrical installation,
read the instructions in the section “Proper Installation
of Elec tronic Equip ment in an Industrial Environment”.
RWB II units are supplied with a QUANTUM control system.
Care must be taken that the controls are not ex posed to
phys i cal dam age dur ing han dling, storage, and installa tion.
The single-box con trol door must be kept tight ly closed to
pre vent mois ture and foreign mat ter from entry.
NOTE: All customer connections are made in the sin gle-
box control mounted on the oil separator. This is the
ONLY elec tri cal enclosure and it should be kept tight ly
closed when ev er work is not being done in it.
VOLTAGE PROTECTION
Frick
®
does not advise nor support the use of UPS power
systems in front of the Quantum
™
panel. With a UPS power
system providing shutdown protection for the Quantum
™
,
the panel may not see the loss of the 3-phase voltage on
the motor because the UPS could prevent the motor starter
contactor from dropping out. With the starter contactor still
energized, the compressor auxiliary will continue to feed
an “Okay” signal to the panel. This will allow the motor to
be subjected to a fault condition on the 3-phase bus. Some
fault scenarios are:
1.
The 3-phase bus has power “on” and “off” in a continuous
cyclic manner which may cause the motor to overheat
due to repeated excessive in-rush currents.
2.
Motor cycling may damage the coupling or cause other
mechanical damage due to the repeated high torque
motor “bumps”.
3.
Prolonged low voltage may cause the motor to stall and
overheat before the motor contactor is manually turned
off.
Under normal conditions, the loss of 3-phase power will shut
the Quantum
™
panel down, and it will restart upon power
return. If the panel was in:
•
Auto – Compressor motor will return to running as
programmed.
•
Remote – The external controller would reinitialize the
panel and proceed to run as required.
•
Manual – The compressor will have to be restarted
manually after the 3-phase bus fault has been cleared.
If the local power distribution system is unstable or prone to
problems, there are other recommendations to satisfy these
problems. If power spikes or low or high line voltages are the
problem, then Frick
®
recommends the use of a Sola
®
constant
voltage (CV) transformer with a line suppression feature. If
a phase loss occurs, then you will typically get a high motor
amp shutdown. If problems continue to exist, then an exami-
nation of the plant’s power factor may be in order.
Unless careful design failure analysis is considered in the
implementation of power systems, the alternative solutions
provide a safer and less expensive implementation. In either
case, only one Sola
®
may be used per compressor. Each
compressor needs to be individually isolated from each other
through a dedicated control transformer. Sharing a common
control power source is an invitation for ground loops and
the subsequent unexplainable problems.
MOTOR STARTER PACKAGE
SBC Board damage may occur
with out timer re lay in stalled in
con trol panel as shown in Starter
Wir ing Diagram, Figure 15. All Frick mo tor starter pack-
ag es have the tim er re lay as stan dard.
STARTER WIRING DIAGRAM
Figure 15
Содержание RWB II
Страница 43: ...RWB II ROTARY SCREW COMPRESSOR UNITS MAINTENANCE S70 200 IOM Page 43 P I DIAGRAM...
Страница 46: ...RWB II ROTARY SCREW COMPRESSOR UNITS MAINTENANCE S70 200 IOM Page 46 P I DIAGRAM LIQUID INJECTION BOOSTER...
Страница 50: ...RWB II PLUS ROTARY SCREW COMPRESSOR UNITS FORMS S70 200 IOM Page 50 OPERATING LOG SHEET...