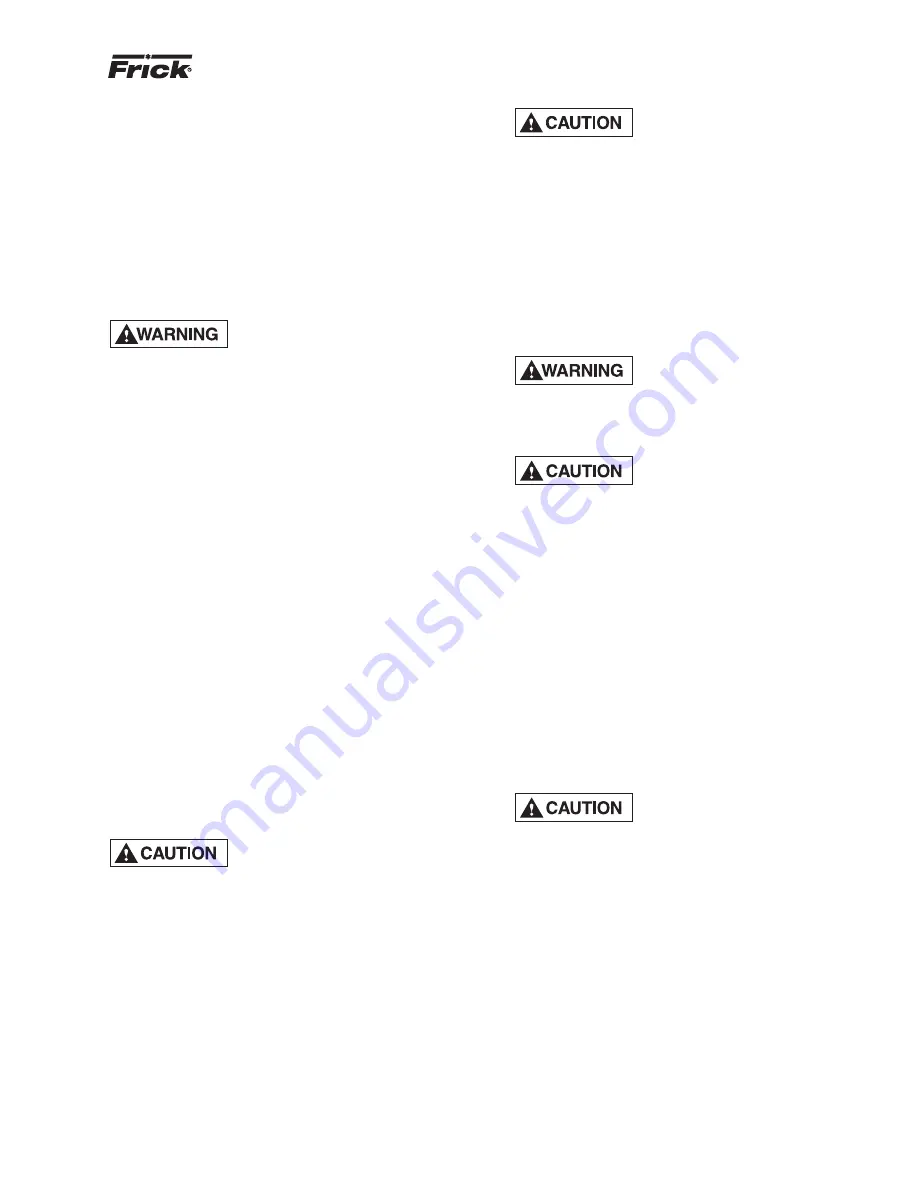
RWB II ROTARY SCREW COMPRESSOR UNITS
MAINTENANCE
S70-200 IOM
Page 27
STRAINER - LIQUID INJECTION
To clean the liquid injection strainer the unit must be shut
down. The procedure is as follows:
1. Push [STOP] key on microprocessor panel to shutdown
unit, then open disconnect switches for compressor and oil
pump motor starters.
2. Close liquid supply service valve located before liquid
so le noid.
3. Immediately screw in the manual solenoid valve stem
to relieve liquid re frig er ant pres sure trapped between
the so le noid and the service valve.
Excessive pressure from ex pand ing
refrigerant trapped be tween stop
valve and so le noid may cause
gas ket and O-ring fail ure and un con trolled re frig er ant
release.
4. Close service valve located be tween the compressor and
the liquid injection thermovalve.
5. Carefully loosen capscrews se cur ing the strainer cover to
the strainer. Allow pressure to re lieve slowly.
6. When all entrapped refrigerant has been relieved, care-
ful ly remove loos ened capscrews (as liquid refriger ant is
sometimes caught in the strainer), strain er cover and strain er
basket.
7. Wash the strainer basket and cov er in solvent and blow
clean with air.
8. Reassemble strainer.
9. Open service valve between com pres sor and liquid in-
jec tion thermovalve and check for leak age.
10. Screw out manual solenoid valve stem.
11. Carefully open liquid supply ser vice valve.
12. Leak test.
13. Close disconnect switches for com pres sor and oil pump
motor start ers.
14. Start unit.
COALESCER FILTER ELEMENT(S)
Use of fi lter elements other than
Frick may cause warranty claim
may to be denied.
When changing the coalescer fi lter element(s) it is recom-
mended that the oil be changed, cartridge(s) in oil fi l ters
OF-1, OF-2, and OF-3 (if ap pli ca ble) be changed, and the
fol low ing ap pli ca ble strainer el e ments be removed and
cleaned.
1. Refer to oil changing Steps 1 through 8.
2. Loosen manway cover retainer bolts, remove retainers,
manway cov er and cover gasket. Dis card cov er gasket.
3. Remove and retain nut securing co a lesc er fi lter retainer.
4. Remove retainer, coalescer fi lter el e ment and 2 O-rings.
Discard fi lter el e ments.
5. Install new coalescer fi lter element(s).
Seat el e ment in center of locating
tabs on separator bulk head.
6. Replace coalescer fi lter retainer and nut. Torque nut to 21
ft-lb. DO NOT OVER TIGHT EN NUT.
7. Install a new manway gasket and replace manway
cover.
8. Tighten manway bolts. NOTE: RE TIGHTEN AFTER THE
COM PRESSOR UNIT IS RE PRES SUR IZED, SINCE MAN-
WAY BOLTS WILL LOOSEN.
9. Refer to oil changing Steps 9 through 14.
CHANGING OIL
DO NOT MIX OILS of different
brands, manufacturers, or types.
Mix ing of oils may cause ex ces sive
oil foam ing, nui sance oil level cut outs, oil pressure
loss, gas or oil leakage and cat a stroph ic compressor
fail ure.
Use of fi lter elements other than
Frick may cause warranty claim
may to be denied.
Shut down the unit when changing oil. At the same time all oil
fi lter cartridges must be changed and all oil strainer el e ments
removed and cleaned. The procedure is as follows:
1. Press the [STOP] key on the microprocessor panel to stop
the compressor unit.
2. Open the disconnect switch for the compressor motor
start er.
3. Close the suction and dis charge service valves; also
close the liq uid-in jec tion and economizer ser vice valves, if
ap pli ca ble.
4. SLOWLY vent separator to low-side system pressure us-
ing the bypass line on the suction trap. NOTE: Recover or
trans fer all re frig er ant vapor, in ac cor dance with lo cal
or di nanc es, before opening to at mo sphere. The sep a -
ra tor MUST be equalized to at mo spher ic pressure.
Oil en trained refrigerant may va-
por ize, caus ing a sep a ra tor pres-
sure in crease. Repeat vent ing and
re cov ery pro ce dure, if nec es sary.
5. Open the drain valve(s) located on the underside of the
separator and drain the oil.
6. Drain the oil fi lter(s) OF-1 and, if ap plicable, the oil cool ers
and fi lter OF-2.
7. Remove the old fi lter cartridges, then in stall new ones
(as previously described in the section OIL FILTER (OF-1)
MAIN SIN GLE/DUAL).
8. Remove, clean, and re in stall strain er elements in the
strain ers.
9. Evacuate the unit to 28" Hg vacuum.
10. Open the suction service valve and pressurize the unit
to system suction pressure. Close the suction valve and leak
test.
Содержание RWB II
Страница 43: ...RWB II ROTARY SCREW COMPRESSOR UNITS MAINTENANCE S70 200 IOM Page 43 P I DIAGRAM...
Страница 46: ...RWB II ROTARY SCREW COMPRESSOR UNITS MAINTENANCE S70 200 IOM Page 46 P I DIAGRAM LIQUID INJECTION BOOSTER...
Страница 50: ...RWB II PLUS ROTARY SCREW COMPRESSOR UNITS FORMS S70 200 IOM Page 50 OPERATING LOG SHEET...