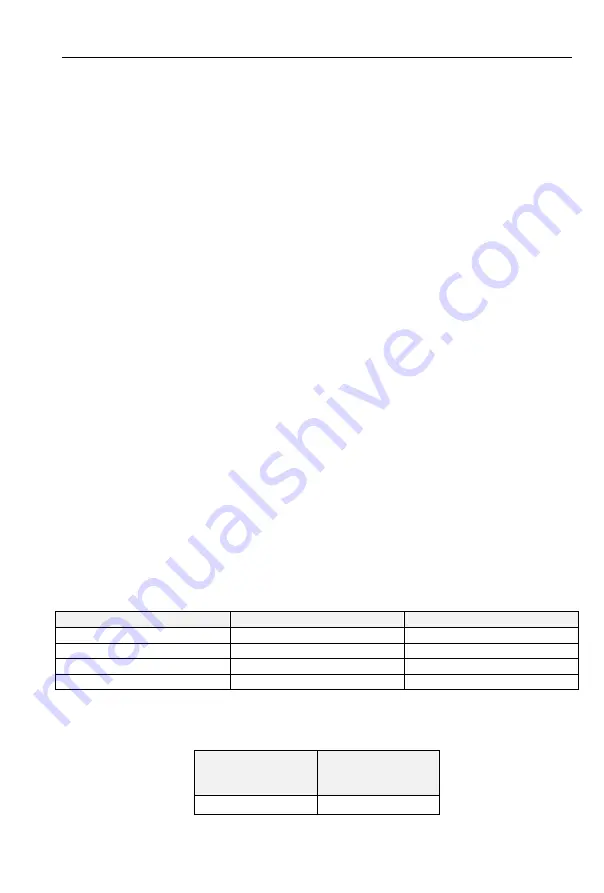
FR500D Series Special Purpose Inverter for Elevator
- 14 -
To complete the wiring of controller, elevator and motor and the wiring of PG card and encoder, no
need R2 & Y1 wiring if the controller is without operation contactor (KM20) and fault signal receive.
Then commissioning procedure is as below:
1,To set high speed and leveling speed,, related setting parameter according to the wiring is as
below:
F12.00= 0
F12.01=High speed
F12.02= Leveling speed
2, To set maintenance speed. Maintenance speed and leveling speed will be common in some
elevator controllers, if no maintenance signal output, no need wiring for maintenance; If maintenance
signal output available, the speed can be set via function code
H00.13=Maintenance speed
3,Base block signal, no need wiring of base block if base block signal is not available in elevator
controller; If base block is available, most of elevator controllers provide normally closed signal, if so
need to set DI7 in anti-logic as below
F04.14=00010
4,Maintenance operation testing. First, set F00.08=1, then switch the elevator controller to
maintenance operation mode, and press LIFT UP or LIFT DOWN to check if the running direction is
consistent. If not, exchange UP and DOWN signal line, means exchange DI1 & DI2 signal lines
5,To check encoder direction, set F00.08=1, then switch the elevator controller to maintenance
operation mode, and press LIFT UP or LIFT DOWN to check if the output frequency is consistent with
feedback speed of encoder (Shown in U00.33). If output frequency is positive, the speed of U00.33
should be also positive; If output frequency is negative, the speed of U00.33 should be also negative.
If the directions are not consistent, need to set F08.25=1 or exchange A & B pulse of encoder, then to
check output frequency is consistent with feedback speed of encoder.
6,Operation in closed loop vector control mode, to set encoder line number of F08.23, also set
motor and encoder speed ratio of F08.27, and set F00.08 for closed loop vector control mode, to
switch the elevator controller to maintenance operation mode, and press LIFT UP or LIFT DOWN to
check if elevator is working normally
7,Trial run in normal mode, to switch elevator controller to be normal operation mode for testing,
to improve the comfort by adjusting acceleration & deceleration (F03.00, F03.01) and S curve time
(F03.11)
2.6 Multi-step speed setting method
In different elevator controllers, the combination difference of multi-step speed terminal output
signal will cause the parameter setting difference of leveling speed and high speed, please refer to
below diagram for the parameter setting:
DI4(F04.03=14)
DI3(F04.02=13)
Speed setting parameter
0
0
F12.00
0
1
F12.01
1
0
F12.02
1
1
F12.03
Speed parameter of group F12 will be set by percentage, 100.0% corresponded to maximum
frequency (Setting value of F01.08),meanwhile every step speed can be acceleration time and
deceleration time independently, please refer to below diagram for the details
Multi step speed
Parameter for
selecting accel and
decel time
F12.00
F12.34