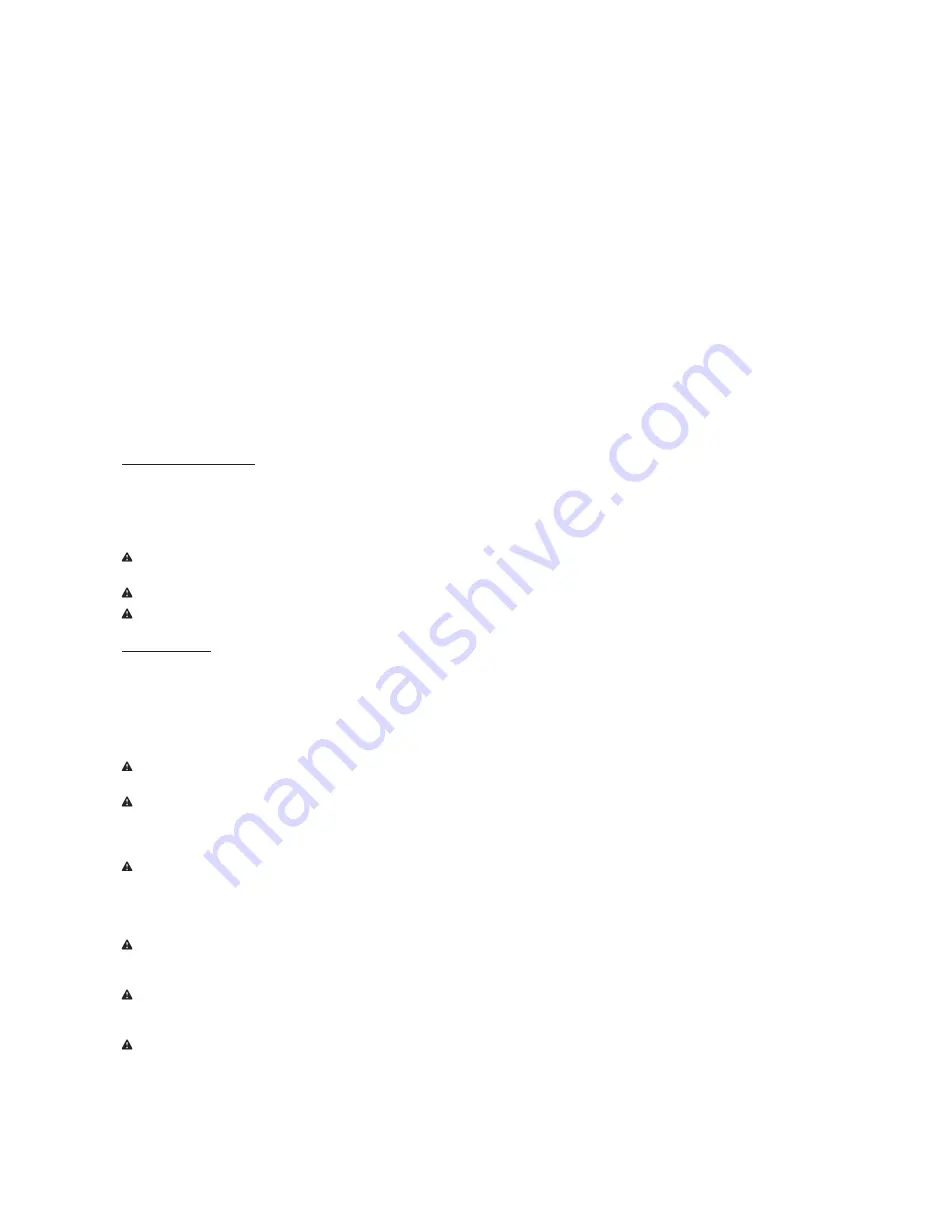
The information in this publication is provided for reference only. While every effort has been made to ensure the reliability and accuracy of
the information contained in this manual at the time of printing, we recommend that you refer to “franklinfueling.com” for the most current
version of this manual. All product specifications, as well as the information contained in this publication, are subject to change without notice.
Franklin Fueling Systems does not assume responsibility and expressly disclaims liability for loss, damage, or expense arising out of, or in any way
connected with, installation, operation, use, or maintenance by using this manual. Franklin Fueling Systems assumes no responsibility for any
infringement of patents or other rights of third parties that may result from use of this manual or the products. We make no warranty of any kind
with regard to this material, including, but not limited to, the implied warranties of merchantability and fitness for a particular purpose.
Copyright © 2021 Franklin Fueling Systems, LLC, Madison, WI 53718. All world rights reserved. No part of this publication may be stored in a
retrieval system, transmitted, or reproduced in any way, including, but not limited to, photocopy, photograph, magnetic, or other record, without
the prior written permission of Franklin Fueling Systems.
For technical assistance, please contact Franklin Fueling Systems:
franklinfueling.com
3760 Marsh Rd. • Madison, WI 53718 • USA
Tel: USA & 1 800 225 9787 • Fax: +1 608 838 6433
Tel: UK +44 (0) 1473 243300 • Tel: Mex 001 800 738 7610
Tel: DE +49 6571 105 380 • Tel: CH +86 10 8565 4566
Belden is a trademark of Belden Technologies, Inc
EVO is a trademark and FE PETRO, FFSPro,
and AUTO-LEARN are registered trademarks of Franklin Electric Company, Inc.
Red Jacket and Veeder-Root are registered trademarks of The Veeder-Root Company
000-2145 r11
Conventions used in this manual
This manual includes safety precautions and other important information presented in the following format:
NOTE
: This provides helpful supplementary information.
IMPORTANT
: This provides instructions to avoid damaging hardware or a potential hazard to the environment, for example: fuel leakage from
equipment that could harm the environment.
CAUTION
: This indicates a potentially hazardous situation that could result in minor or moderate injury if not avoided. This may also be used to
alert against unsafe practices.
WARNING
: This indicates a potentially hazardous situation that could result in severe injury or death if not avoided.
DANGER
: This indicates an imminently hazardous situation that will result in death if not avoided.
Operating precautions
Franklin Fueling Systems (FFS) equipment is designed to be installed in areas where volatile liquids such as gasoline and diesel fuel are present.
Working in such a hazardous environment presents a risk of severe injury or death if you do not follow standard industry practices and the
instructions in this manual. Before you work with or install the equipment covered in this manual, or any related equipment, read this entire
manual, particularly the following precautions:
IMPORTANT
: To help prevent spillage from an underground storage tank, make sure the delivery equipment is well-maintained, that there is a
proper connection, and that the fill adaptor is tight. Delivery personnel should inspect delivery elbows and hoses for damage and missing parts.
CAUTION
: Use only original FFS parts. Substituting non-FFS parts could cause the device to fail, which could create a hazardous condition and/
or harm the environment.
WARNING
: Follow all codes that govern how you install and service this product and the entire system. Always lock out and tag electrical
circuit breakers while installing or servicing this equipment and related equipment. A potentially lethal electrical shock hazard and the possibility
of an explosion or fire from a spark can result if the electrical circuit breakers are accidentally turned on while you are installing or servicing this
product. Refer to this manual (and documentation for related equipment) for complete installation and safety information.
WARNING
: Before you enter a containment sump, check for the presence of hydrocarbon vapors. Inhaling these vapors can make you dizzy or
unconscious, and if ignited, they can explode and cause serious injury or death. Containment sumps are designed to trap hazardous liquid spills
and prevent environmental contamination, so they can accumulate dangerous amounts of hydrocarbon vapors. Check the atmosphere in the
sump regularly while you are working in it. If vapors reach unsafe levels, exit the sump and ventilate it with fresh air before you resume working.
Always have another person standing by for assistance.
WARNING
: Follow all federal, state, and local laws governing the installation of this product and its associated systems. When no other
regulations apply, follow NFPA codes 30, 30A, and 70 from the National Fire Protection Association. Failure to follow these codes could result in
severe injury, death, serious property damage, and/or environmental contamination.
WARNING
: Always secure the work area from moving vehicles. The equipment in this manual is usually mounted underground, so reduced
visibility puts service personnel working on it in danger from moving vehicles that enter the work area. To help prevent this safety hazard, secure
the area by using a service truck (or some other vehicle) to block access to the work area.
DANGER
: Make sure you check the installation location for potential ignition sources such as flames, sparks, radio waves, ionizing radiation,
and ultrasound sonic waves. If you identify any potential ignition sources, you must make sure safety measure are implemented.
Содержание TS-LS500
Страница 1: ...TS LS500AUTO LEARN LINE LEAK DETECTION INSTALLATION GUIDE...
Страница 37: ...33 Control Drawing 1...
Страница 38: ...34 Control Drawing 2...
Страница 39: ...Intentionally Blank...
Страница 40: ...000 2145 r11...