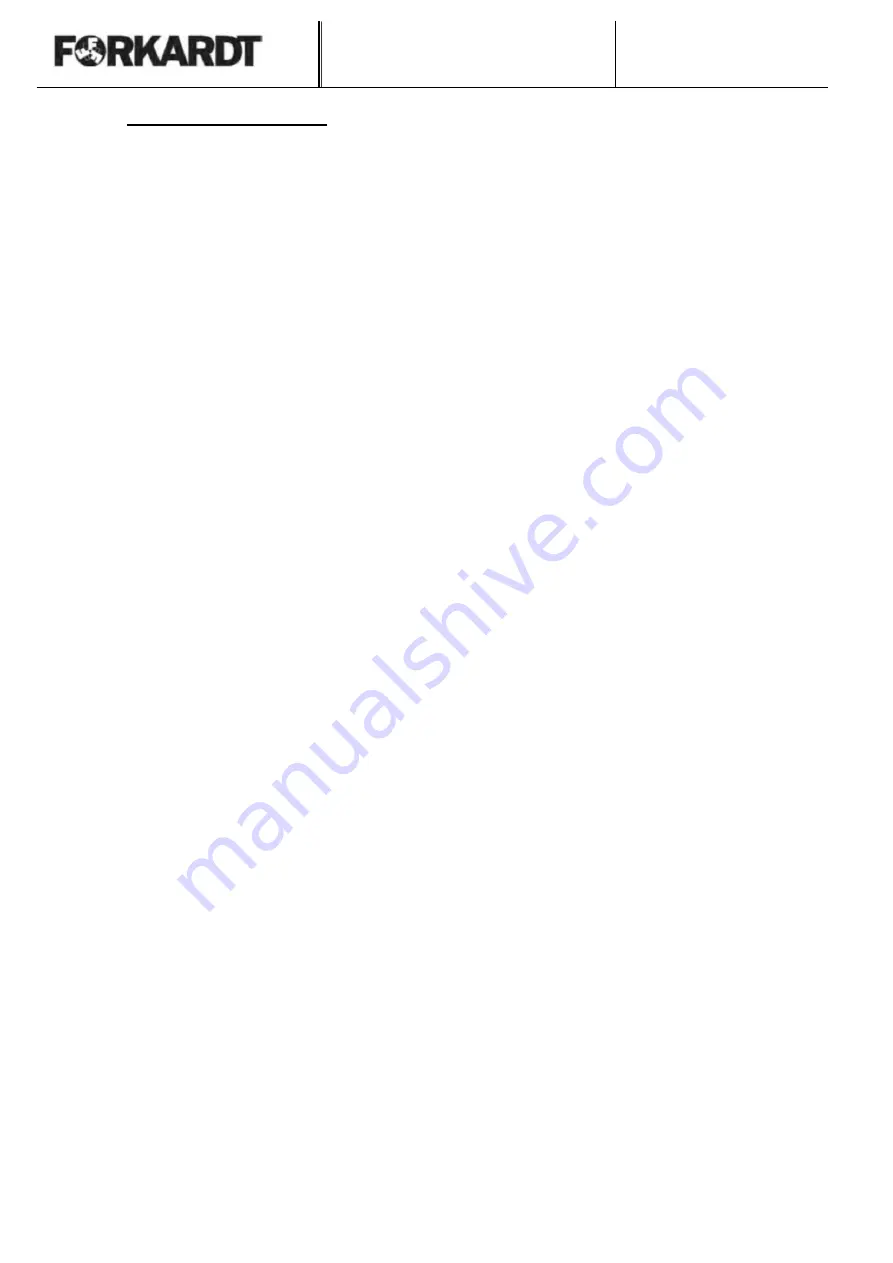
Table of contents
3QLCLM
Edition: 04/2014
23
5.3 Dynamic gripping force
The dynamic gripping force F
Sp
is the total force (daN) supplied by all of the jaws under dynamic
conditions and represents the minimum value of the available gripping force under normal operating
conditions.
These are:
•
•
well maintained condition and
•
•
adequate lubrication of all sliding surfaces
of the power chuck. In really good condition, power chucks will exceed the calculated value of F
Sp
The static gripping force is a function of the chuck design data. But does not solely determine the
gripping force under dynamic conditions. The gripping jaws appreciably effect the performances of a
chuck. They have to be selected to suit the specific application.
The gripping jaws effect the gripping force and hence the maximum permissible speed. The centrifugal
force of the jaws of power chucks can have such a significant effect on the gripping force that this
effect has to be taken into consideration at higher spindle speeds.
The centrifugal force generated by the master jaws and top jaws which reduces the gripping force of
the chuck is countered in Type 3 QLCKT power chucks by counterbalancing levers so that the gripping
force acting on the work piece remains practically constant.
The gripping force to be applied at standstill, FSp0, must be correspondingly high so that the gripping
force required for cutting is still available at the selected spindle speed. The effect of the
counterbalancing weights actuated by the levers is taken into consideration for Type 3 QLCKT power
chucks by the chuck constant C4.