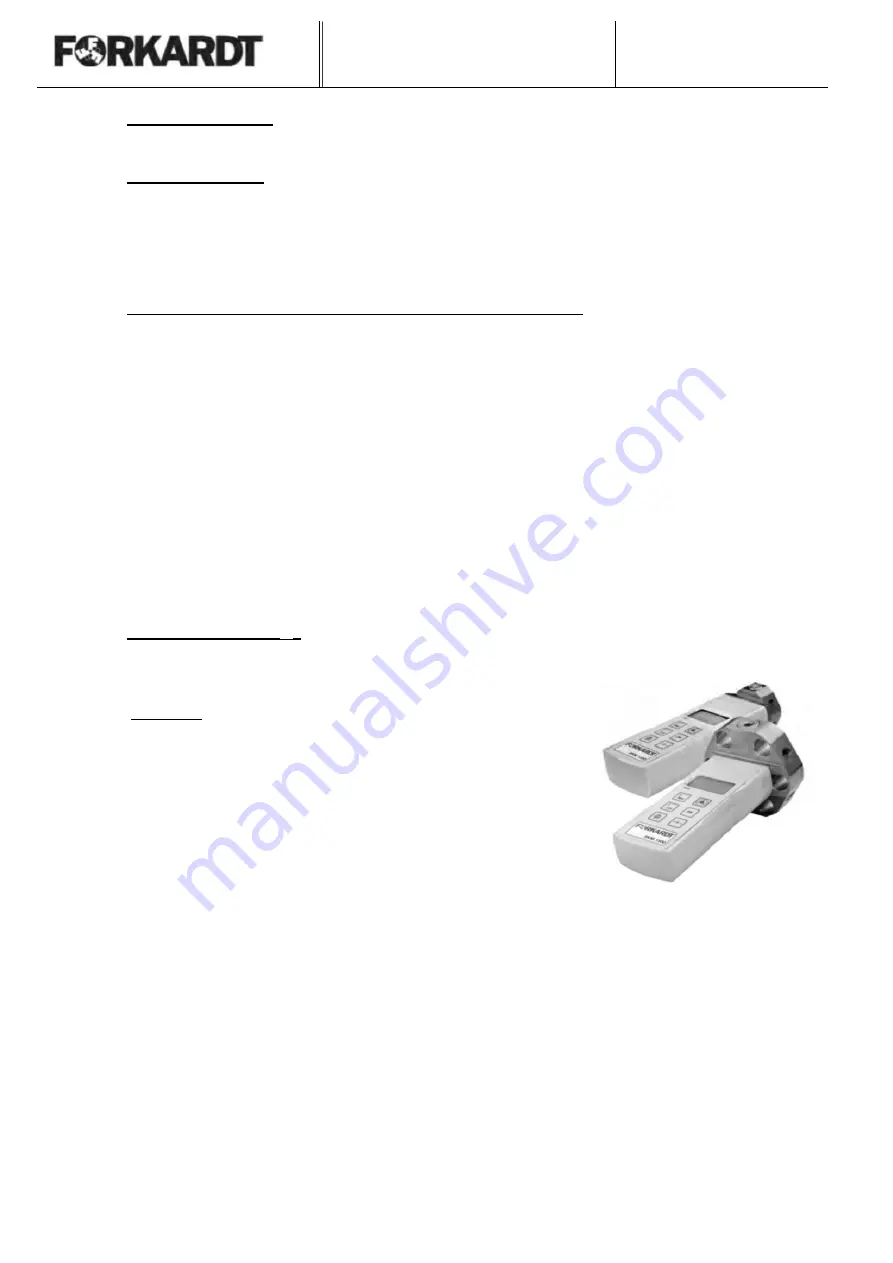
Table of contents
3QLCLM
Edition: 04/2014
22
5.0 Chucking force
5.1 General notes
The connection of the power chuck to the work piece is force-locking, i.e. the force transfer happens by
pressing the chuck jaw (master jaw with top jaw) to the work piece. The contact pressure required for
creating this force locking is called as gripping force.
Various influences have direct or indirect effect on the gripping force:
•
Variable friction coefficient between work piece and top jaw
•
Proportion of clamping diameter and working diameter
•
Magnitude of the cutting force on the cutting tool
•
Swing of the top jaw from the clamping point
•
Decrease of the gripping force through centrifugal force due to external clamping.
Rotating work holding equipment is subject to centrifugal forces that increase with the square of the
speed of rotation. The centrifugal force opposes the gripping force in the case of external chucking
and increases it in the case of internal chucking. The residual dynamic gripping force at high spindle
speeds depends on the static gripping force, the mass of the chuck jaws and the radius of their center
of gravity.
5.2
Gripping force F
Sp
0
The max. gripping force FSp0 is only achieved under favorable conditions.
These are:
•
A well maintained power chuck
•
Optimum lubrication of all sliding surfaces
•
Application of maximum actuating force
•
Short overhang of top jaws
•
Spindle static n = 0 ( or low spindle speed )
The static gripping force is measured with a static gripping force meter, e.g. SKM 1200 / 1500, SKM
1200 / 1500, see publication 930.10.02D. The values of F
Sp
0 can be used for stress calculations, e.g.
for the design of special jaws.