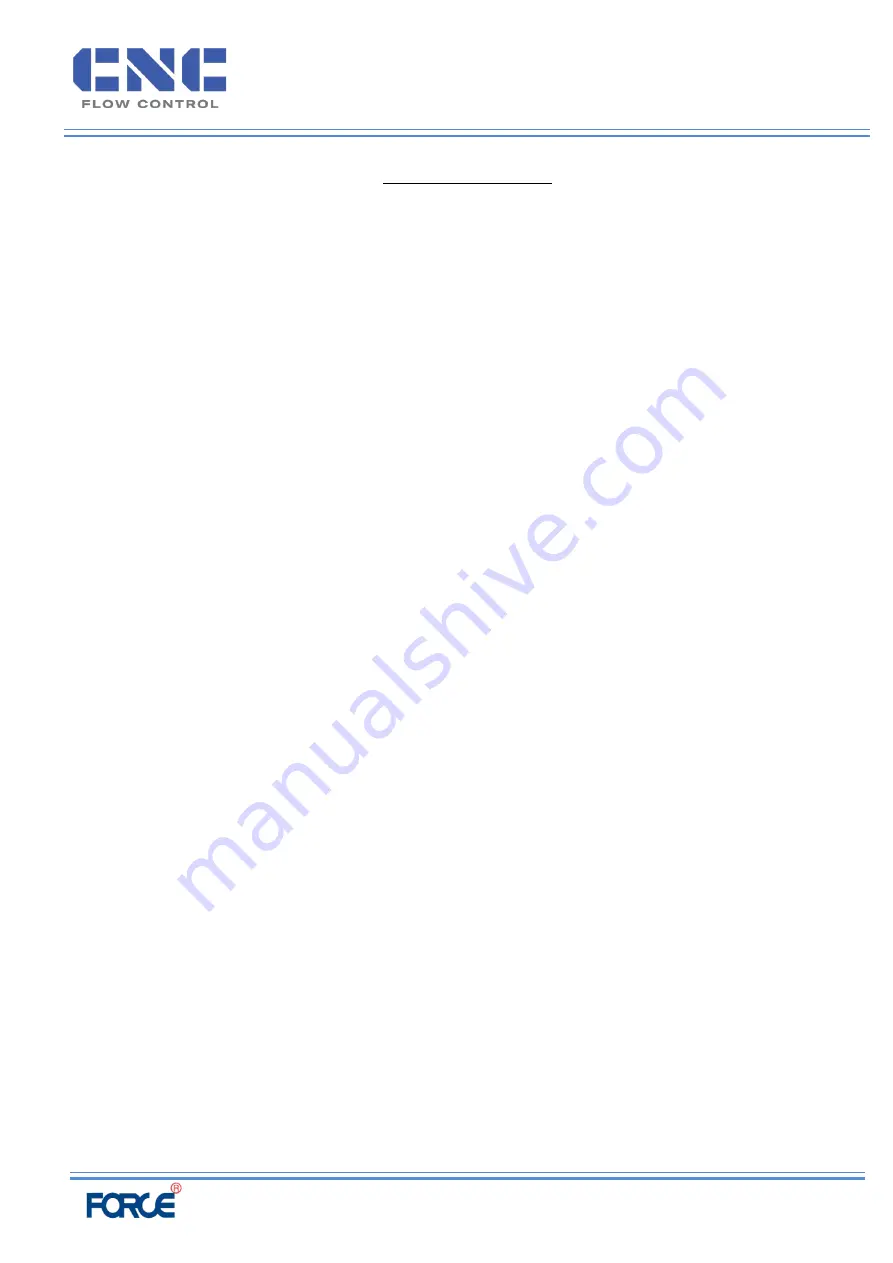
Force
– Two Piece Trunnion
Mounted Ball Valve
Document Number:
Revision:
Release Date:
EDC 514
A
05/09/2022
IOM: Installation, Operation and Maintenance Manual
30/43
Ⅵ. Periodic inspection
2.
Maintenance
Under normal conditions, the Force Trunnion mounted Ball valve’s simplistic design will
allow for a long Service life with low maintenance costs over the life of the valve.
I
t is recommended to adopt a regular maintenance schedule. Valve bodies should be
regularly drained to discourage the formation of scale, corrosion products, or
accumulation of sediment within the valve body. If, for some reason, a routine program
cannot be adopted, it is recommended to drain the valves under the following
circumstances.
A.) After Hydrostatic testing
B.) After Cleaning the line.
C.) When valve cannot be fully stroked with ease.
2.4.1
Draining Procedure.
A.) Make sure to use safety glasses, and other appropriate safety apparel before
attempting to drain a valve. Depressurize the valve/pipe line before removing the drain
fitting.
B.)
V
erify the bore position. Bleed ports should never be opened when the valve bore is
in the partially open position!
C.)
V
erify the location of the drain fitting. Note the direction of the hole where the fluid
will exit the fitting, and make sure the hole is free of dirt or debris.
D.) Apply a backup wrench to the body of the fitting to prevent the fittings itself from
being unscrewed, and with the port of the bleed fitting pointed in the opposite direction
from your body begin to loosen the bleed plug with a second wrench. Continue to
loosen the plug until a enough discharge rate has been achieved.
E.) When fluid ceases to flow from the bleed fitting, you have completely drained the
valve body. use the wrench to close the bleed plug.
F.) Move the bore position 15-20 degrees, and then return it to the fully open/closed
position. This will allow pressurized fluid to enter the body cavity again. Observe the
bleed plug to be sure it is not leaking. If the bleed plug Is not leaking, the valve is ready
for use.
G.) Note: all fluids discharged from a valve should be properly disposed in accordance
with local/state/federal Laws.
Note: only hand wrenches should be used to loosen bleed fittings. Wrenches should be
appropriately sized so as not to provide an excess of leverage which may damage the
bleed fitting. Pneumatic wrenches should not be used.