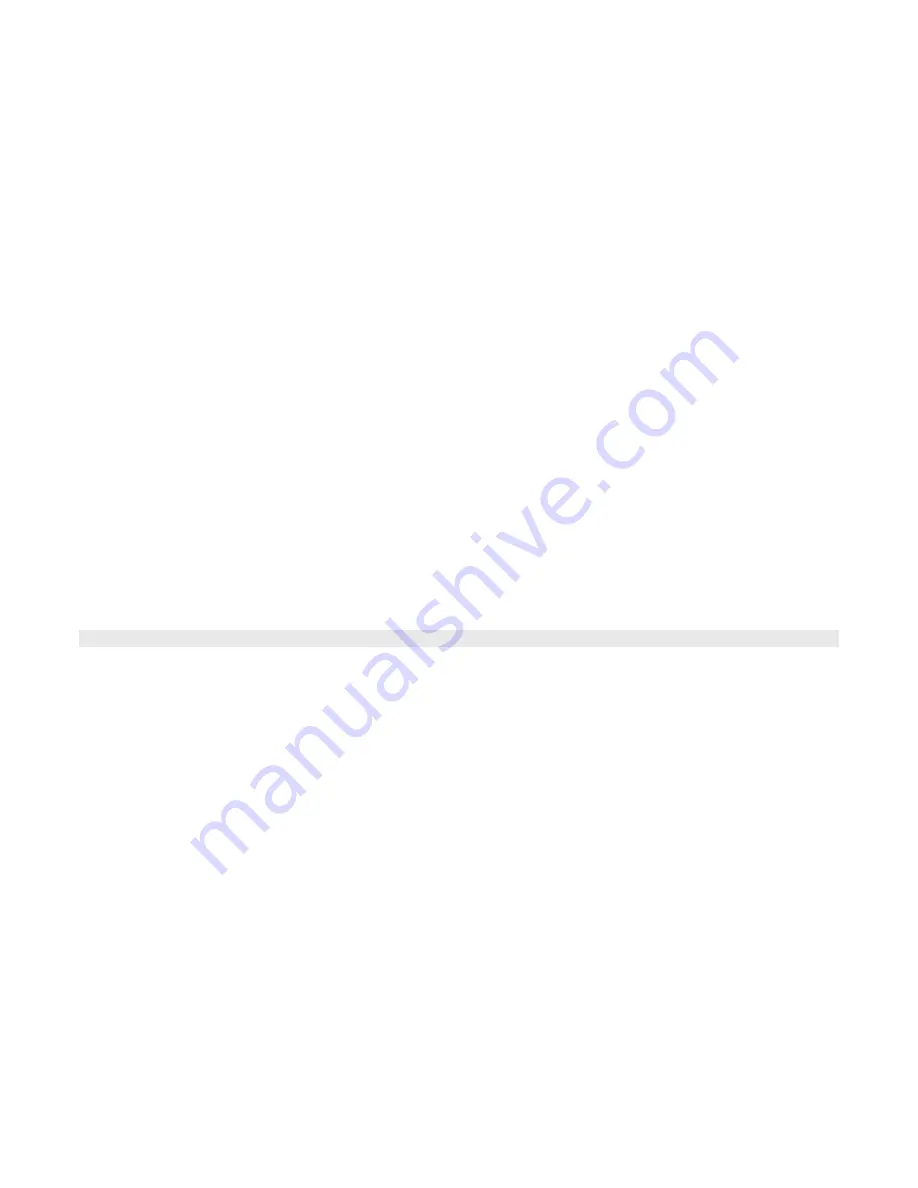
The boiler is to be yearly serviced to ensure efficient and trouble-
free operation following to the below described plan.
Maintenance (and repair) operations are to be exclusively perfor-
med by qualified personnel.
The manufacturer recommends Customers to have an Authorized
Service Center implement any maintenance and repair procedure.
Disconnect the boiler from power mains prior to performing any
maintenance procedure either involving replacement of componen-
ts and/or internal cleaning.
Maintenance plan
Routine maintenance must include the following checks:
- boiler general integrity;
- leak test involving the boiler gas pipes and the gas network;
- boiler ignition sequence;
- boiler combustion parameters test, through flue gas analysis (to
be performed on a two-year basis if boiler is individually installed.
Annually to cascade-installed boilers);
- integrity and leak test of flue gas pipe system;
- general integrity of boiler safety devices;
- water leak check and presence of oxide deposit on boiler connec-
tion pipes;
- water pressure switch efficiency;
the following cleaning operations (the boiler is to be cool):
- general internal cleaning;
- burner cleaning and adjustment as necessary;
- heat exchanger flue gas side cleaning: to be performed by means
of a swab or vacuum cleaner in order to remove combustion lefto-
vers from the heat exchanging surfaces and fins.
As an alternative, specific chemical products may be employed,
following their use instructions.
When cleaning the heat exchanger, do not employ petrol, sol-
vents or similar substances.
In the event of boiler first maintenance operation, verify:
- boiler room characteristics according to boiler requirements;
- room ventilation grilles;
- flue gas system dimensions, diameters and lengths of ducts;
- correct installation of the boiler in compliance with the instructions
in this manual.
Should the boiler not be correctly operating, and in no imme-
diate hazard to people, animals and property, notify the sy-
stem supervisor, both verbally and in writing.
4. MAINTENANCE
3.6. Switching to different gas and burner adjustment
Boiler conversion from natural gas to LPG and vice-versa is striclty
to be impelmented by qualified personnel.
In order to verify nozzle and gas inlet pressure, connect a mano-
meter to checks on the gas valve.
Boilers are factory-set according to gas type requested upon order.
Any later conversion must be performed by qualified technicians,
employing the conversion kit (supplied with boiler) and the instruc-
tions for conversion and adjustment.
Converting the boiler from natural gas to LPG
Follow the instructions below:
- remove the pilot burner natural gas nozzle after removing the bi-
cone fixing bolt and removing the pilot burner gas supply pipe;
- install the LPG nozzle, verifying its compliance with the technical
data table and, after re-installing the gas supply pipe, tighten the
bi-cone fixing bolt;
- remove the main burner natural gas nozzles and install the LPG
ones verifying their compliance with the technical data table;
- unscrew the cap of the pressure adjuster of the gas valve and fully
tighten the screw of the pressure adjuster;
- screw the cap of the pressure adjuster of the gas valve back on
and seal it (e.g. by means of paint or self-sticking label);
- check for gas leaks, especially from the gas connections that were
part of the above procedure;
- position the self-sticking label provided with the conversion kit,
indicating the type of gas and pressure for which the device was
adjusted;
Converting the boiler from LPG to natural gas
Follow the instructions below:
- remove the pilot burner LPG nozzle after removing the bi-cone
fixing bolt and removing the pilot burner gas supply pipe;
- install the natural gas nozzle, verifying its compliance with the
technical data table and, after re-installing the gas supply pipe, ti-
ghten the bi-cone fixing bolt;
- remove the main burner LPG nozzles and install the natural gas
ones verifying their compliance with the technical data table;
- unscrew the cap of the pressure adjuster of the gas valve and un-
tighten the screw of the pressure adjuster so to obtain the pressure
value compliant with technical data table;
- screw the cap of the pressure adjuster of the gas valve back on
and seal it (e.g. by means of paint or self-sticking label);
- check for gas leaks, especially from the gas connections that were
part of the above procedure;
- position the self-sticking label provided with the conversion kit,
indicating the type of gas and pressure for which the device was
adjusted.
21