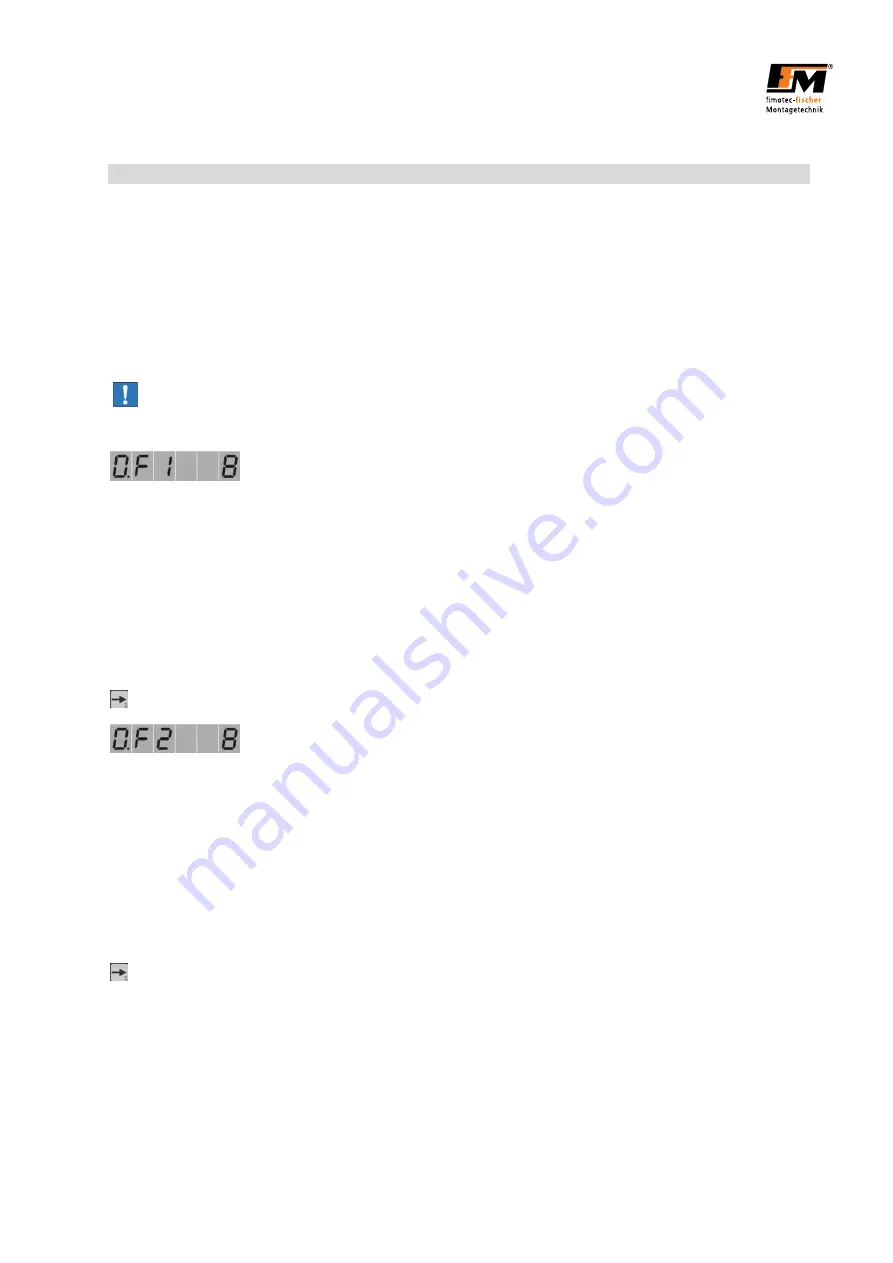
Operating instructions FS-26E
Status as of 10 / 2019
Page 23
4.8 LEVEL 0. - Logic, vibratory conveyor drive
After power ON, the display switches to the "Amplitude" root display.
From here, the 6 key (press 5x) can be used to change to level 0.
On level 0, the control of the vibratory conveyor (physical) and the feedback of the vibratory conveyor
status (logical) are defined and set. The feedback is available as a signal to be further processed
(comparable to an external control signal) with other outputs (functions, such as delayed blast air, can be
easily realized this way).
The following parameters are available:
A logical 1 causes a reaction.
A logical 0 causes no reaction.
Parameter: F1 [function]
Code A and B
Value can be set to O, S
The function has a direct influence on the physical state
of
the
vibratory
conveyor (inversion of the physical state).
O – An applied HI signal is not inverted and is
further
processed
as
logical
1.
An applied LO signal is not inverted and is
further
processed
as
logical
0.
S – An applied HI signal is inverted and is
further
processed
as
logical
0.
An applied LO signal is inverted and is
further
processed
as
logical
1.
Parameter: F2 [function]
Code A and B
Value can be set to O, S
The
function
has
a
direct
influence on the logical, further processable
status
of
the
vibratory
conveyor (inversion of the logical state).
O – An applied HI signal is not inverted and is
further
processed
as
logical
1.
An applied LO signal is not inverted and is
further
processed
as
logical
0.
S – An applied HI signal is inverted and is
further
processed
as
logical
0.
An applied LO signal is inverted and is
further
processed
as
logical
1.