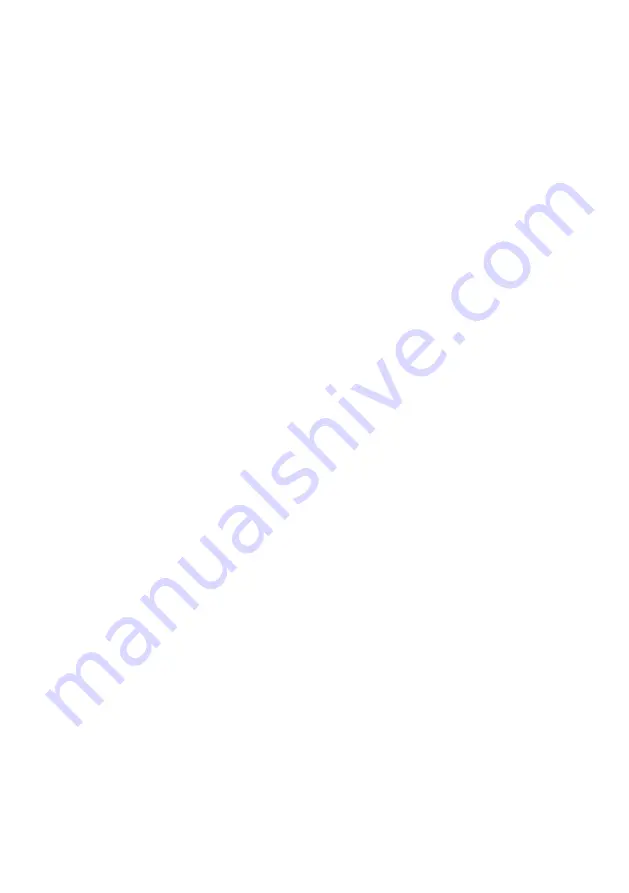
6
Festo — CMMT-ST-C8-1C-...-S0 — 2021-04b
Safety
The diagnostic contact STA must not be used to open a secure locking mechanism directly,
for example.
The diagnostic contact STA is not part of the safety circuit. The diagnostic contact STA is used to
improve diagnostic coverage of the related safety sub-function. The diagnostic contact STA may only
be used in combination with the related safe control signals (AND operation) plus a reliable time
monitoring function in the safety relay unit for the purpose of switching additional safety-critical
functions.
–
At low level, the safety relay unit used delivers a higher current than permissible (maximum
permissible input current exceeded with low level at STO-/A/B
Tab. 19 Control inputs #STO-A and
#STO-B at [X1A]). When this occurs, the device cannot recognise when the safety sub-function is
requested.
–
Use of the safety sub-function STO without external measures for drive axes influenced by external
torques.
If external torques influence the drive axis, use of the safety sub-function STO on its own is
not suitable for stopping the axis safely. Additional measures are required to prevent dangerous
movements of the drive axis, such as use of a mechanical brake.
–
Operation of EC motors requiring a safety classification of SIL 3, cat. 3, Pl e without evaluation of
the diagnostic contact STA.
–
Operation of the connected motor without the danger zone being restricted or enclosed by suitable
means.
The user must not be able to enter the danger zone without triggering the safety function.
–
The safety sub-function STO does not provide protection against electric shock, only against dan-
gerous movements.
–
The safety sub-function STO cannot prevent non-safety-related sub-functions from failing, e.g. the
braking ramp for the SS1-t function or the device's temperature monitoring function.
2.4
Training of qualified personnel
The product may be installed and commissioned only by a qualified electrical engineer who is familiar
with:
–
The installation, operation and maintenance of electrical control systems
–
The applicable regulations for operating safety-related systems
Work on safety-related systems may only be carried out by qualified personnel trained in safety
engineering.
2.5
CE marking
The product has the CE marking.
The product-related EU directives and standards are listed in the declaration of conformity
2.6
Safety engineering approval
The product is a safety device in accordance with the EC Machinery Directive. For details of the
safety-oriented standards and test values that the product complies with and fulfils, see
Technical data, safety engineering. Please note that compliance with the listed standards is limited to
the CMMT-ST-...-S0.