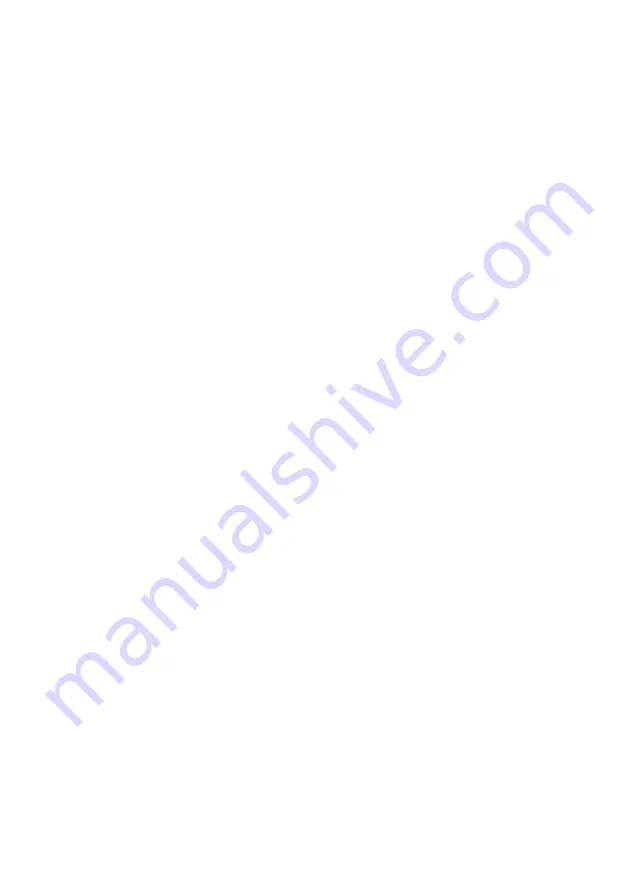
Festo — CMMT-ST-C8-1C-...-S0 — 2021-04b
Safety
5
Check the safety functions at adequate intervals for proper functioning. It is the responsibility of the
operator to choose the type and frequency of the checks within the specified time period. The manner
in which the test is conducted must make it possible to verify that the safety device is functioning
perfectly in interaction with all components. Time period for cyclical test
engineering.
Prior to initial commissioning, wire the control inputs of the safety sub-function STO. The safety
sub-function STO-t is always available without the need for any additional parameterisation.
Keep the documentation somewhere safe throughout the entire product lifecycle.
2.2
Intended use
The safety function might fail, malfunctions might occur, and the connected actuator technology
might move unintentionally if you do not comply with the parameters required for the ambient and
connection conditions.
The CMMT-ST-...-S0 supports the following safety sub-functions in accordance with EN 61800-5-2:
–
safe torque off (STO/Safe torque off)
–
safe stop 1 time controlled (SS1-t/Safe stop 1 time controlled) can only be implemented with a
suitable safety relay unit and appropriate servo drive circuitry
The safety sub-function STO is intended to switch off the torque of the connected motor, thereby
preventing an unexpected restart of the motor.
The safety sub-function SS1-t is intended to perform a fast stop with subsequent torque switch-off.
Ensure that wiring is cross-circuit proof in accordance with EN ISO 13849-1.
2.2.1
Range of application
The device is intended for use in an industrial environment.
Safety sub-functions may only be used for applications for which the stated safety reference values
are sufficient
2.2.2
Permissible components
The load and logic power supply must meet the requirements of EN 60204-1 (protective extra-low
voltage, PELV).
2.3
Foreseeable Misuse
Foreseeable misuse of the safety sub-function STO
–
Use outside the limits of the product defined in the technical data.
–
Bypassing of the safety function.
–
Cross-wiring of the diagnostic feedback signals of more than 10 servo drives. This applies to all
devices that are wired together, regardless of the type of equipment.
–
Faults in the cross-wiring of passive diagnostic contacts and active diagnostic outputs will result
in incorrect diagnostic feedback. It is therefore important to take extra care when carrying out the
cross-wiring. Only wire devices as follows: Always wire all devices with active diagnostic output,
e.g. CMMT-AS, in parallel as a group. Connect the signal from the active diagnostic outputs with the
first CMMT-ST. Wire the passive diagnostic contacts as a group in series and connect the last pas-
sive diagnostic contact directly to the safe controller for evaluation of the diagnostic information.
–
Use of the diagnostic contact STA to switch a safety function.