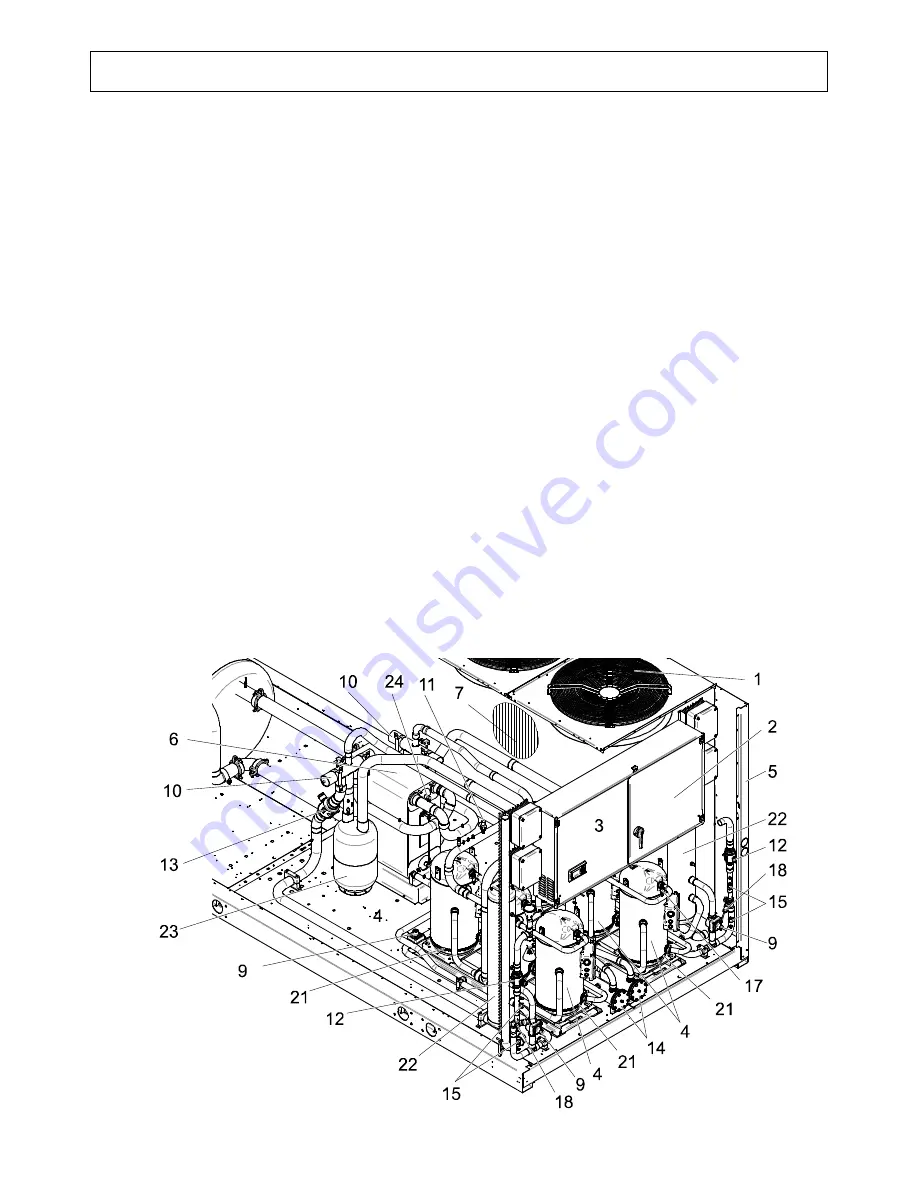
7
GENERAL SPECIFICATIONS
7. Condensing coils,
the aluminium finned pack type with shaped profile to increase the heat exchange coefficient and with copper
pipes arranged in staggered rows. A sub-cooling section is integrated into the lower part.
8. Covering panels,
made of galvanized sheet metal coated with polyurethane powder paint to ensure maximun protection against
adverse weather conditions
9.One-way valves
(IP unit only), allowing the coolant to pass into the appropriate exchangers, depending on the operating cycle.
10. 4-way cycle reversal valve
(IP unit only), reverses the flow direction of the gas as the summer/winter operating mode is changed.
Hydraulic and cooling circuit components (per circuit)
11. Safety valve.
Installed on the delivery pipe of the compressors, this operates if extreme faults should occur in the plant.
12. Fluid tap.
Ball type, this allows the gas flow on the fluid line to be turned on and off. Along with the tap on the compressor delivery,
it allows the components of the fluid line to be subjected to extraordinary maintenance work and the compressors to be replaced if
necessary (without discharging the coolant from the unit): pump down.
13. Compressor delivery tap
. Ball type, allows the gas delivered to the compressors to be turned on and off.
14. Dehydrator filter.
Mechanical cartridge type. Retains impurities and traces of moisture in the circuit.
15. Fluid and humidity indicator.
Signals when fluid passes through the circuit, indicating that the coolant charge is correct. The
fluid indicator light also indicates the amount of moisture in the coolant by changing colour.
16. Low pressure switch.
With fixed setting. It is installed on the suction pipe and blocks the compressors if the operating pressures
drop below the tolerated values. Automatically resets as the pressure increases. If it activates frequently, the unit will block and can
only be restarted by resetting via the user interface terminal.
17. High pressure switch
(n°3). With fixed setting. Are is installed on the delivery pipe and blocks the compressors if the operating pres-
sures exceed the tolerated values. If it activates, the unit will block and can only be restarted by resetting via the user interface terminal.
18. Electronic expansion valve.
This supplies the evaporator correctly, keeping the selected superheating degree at a steady level.
19. Pressure taps:
1/4 “ SAE (7/16” UNF) type with flow regulator. Allow the operating pressure of the system to be measured:
compressor delivery, lamination component inlet, compressor intake.
20. Pressure taps:
5/16 “ SAE type with flow regulator. Allow the charge/discharge of the gas from the system, precisely from com-
pressor outlet an expansion valve inlet.
21. Electrical heating elements to heat the compressor oil.
“Belt” type. These activate when the compressor turns off and keep
the temperature of the oil sufficiently high so as to prevent coolant from migrating during these pauses.
22. Fluid receiver
(IP unit only), this is a plenum tank that accounts for variations to the coolant charge the machine must supply
as the summer/winter operating mode varies.
23. Fluid separator
(IP unit only), on the compressor intake to protect against possible fluid back-flows.
24.
water differential pressure switch.
This is standard supply and is installed on the connections between the water inlet and
outlet of the exchanger. It stops the unit if it activates.
Содержание RHA series
Страница 71: ...71 ...