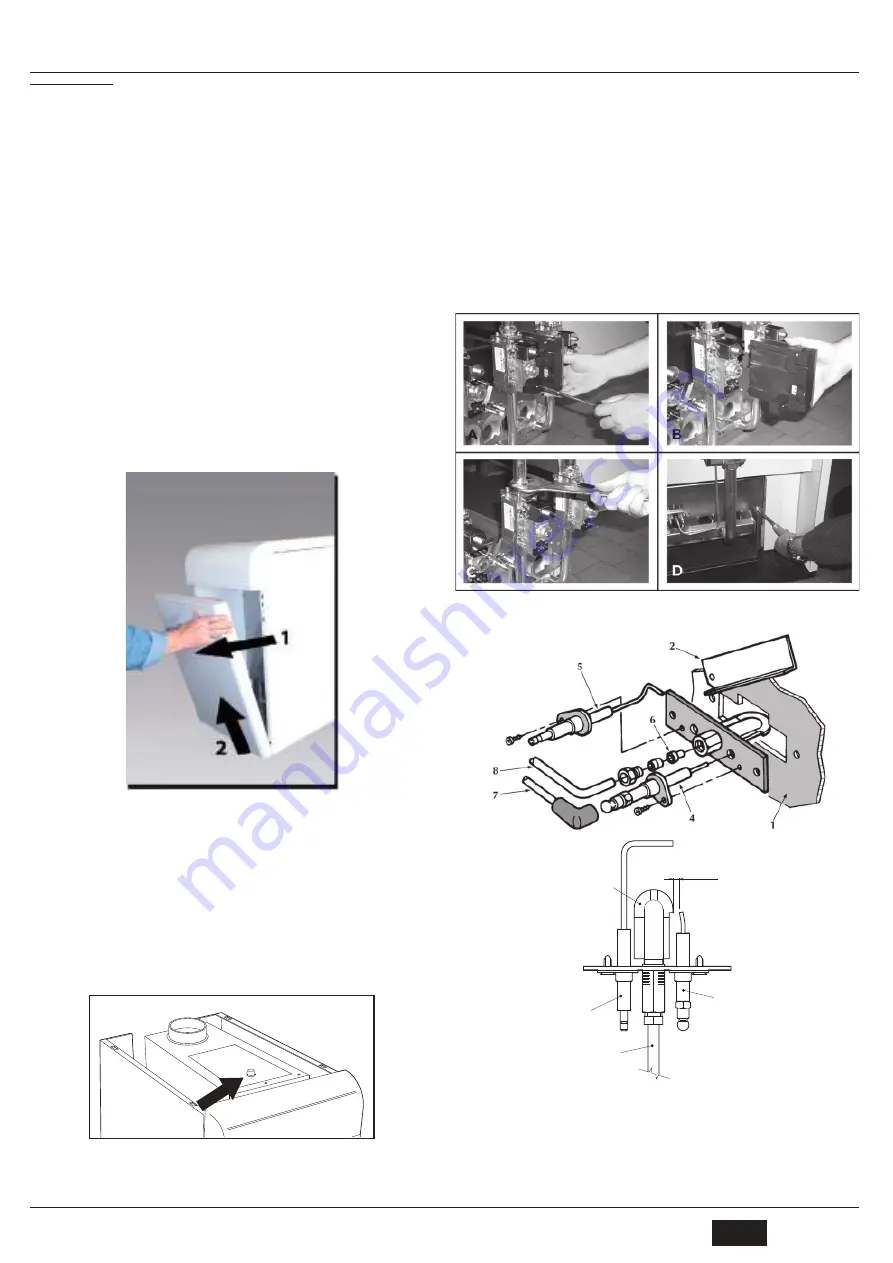
PEGASUS LN 2S
29
EN
4.3 Maintenance
B
THE FOLLOWING OPERATIONS MUST ONLY BE CARRIED OUT BY
QUALIFIED PERSONNEL.
Seasonal inspection of the boiler and flue
It is advisable to carry out the following checks at least once a year:
•
The control and safety devices (gas valve, thermostats, etc.) must function correctly.
•
The fume ducts must be free of obstructions and leaks.
•
The gas and water systems must be tight.
•
The burner and boiler shell must be clean. Follow the instructions in the next section.
•
The electrodes must be free of deposits and properly positioned (see fig. 10).
•
The water pressure in the system when cold must be approx. 1 bar; otherwise bring
it to that value.
•
The expansion tank, if present, must be filled.
•
The gas delivery and pressure must correspond to that given in the technical data
table (see sec. 5.3).
•
The circulating pumps must not be blocked.
Safety devices
The boiler PEGASUS LN 2S is equipped with devices that guarantee safety in case of
operation faults.
Temperature limiter (safety thermostat) with manual reset
This device prevents the water temperature in the system from exceeding boiling point.
The maximum cut-in temperature is 110°C.
Automatic reset of the temperature limiter can only occur on cooling of the boiler (the
temperature must drop by at least 10°C) and identification and elimination of the problem
that caused the shutdown. To reset the temperature limiter, unscrew the cover 3 of fig. 1
and press the button below.
Opening the front casing
To open the front casing, see the sequence in fig. 7.
fig. 7 - Front panel opening
B
Before carrying out any operation inside the boiler, disconnect the power supply
and close the gas cock upstream.
Combustion analysis
A fume sampling point has been included in the upper part of the anti-backflow device
inside the boiler (see fig. 8).
To take the sample:
1.
Remove the top panel of the boiler
2.
Remove the insulation covering the anti-backflow device
3.
Open the fume sampling point;
4.
Insert the probe;
5.
Adjust the boiler temperature to maximum.
6.
Wait 10-15 minutes for the boiler to stabilise*
7.
Take the measurement.
fig. 8 - Combustion analysis
A
Analyses made with a non-stabilised boiler can cause measurement errors.
Burner assembly removal and cleaning
To remove the burner assembly:
•
Disconnect the power and turn off the gas ahead of the boiler.
•
Undo the two screws securing the electronic flame controllers to the gas valve (de-
tail A - fig. 9) and remove them from the gas valves (detail B - fig. 9).
•
Undo the screws securing the connectors to the gas valves and remove them from
the same.
•
Disconnect the ignition and ionisation cables from the electrode assembly.
•
Undo the nuts securing the gas supply pipe ahead of the gas valves (detail C -
fig. 9).
•
Undo the two nuts fixing the combustion chamber door to the cast iron elements of
the boiler (detail D - fig. 9)
•
Remove the burner assembly and combustion chamber door.
Check and clean the burners. Only use a non-metal brush or compressed air to clean the
burners; never use chemical products.
On completion, refit everything by proceeding in reverse order.
fig. 9 - Burner removal and cleaning
Pilot burner assembly
fig. 10 - Pilot burner
1
Combustion chamber door
2
Inspection door
3
Pilot burner
4
Ignition electrode
5
Detection electrode
6
Pilot nozzle
7
High voltage cable
8
Gas supply pipe
3
3 ÷ 4 mm
5
8
4
cod. 3540S242 - Rev. 03 - 04/2018