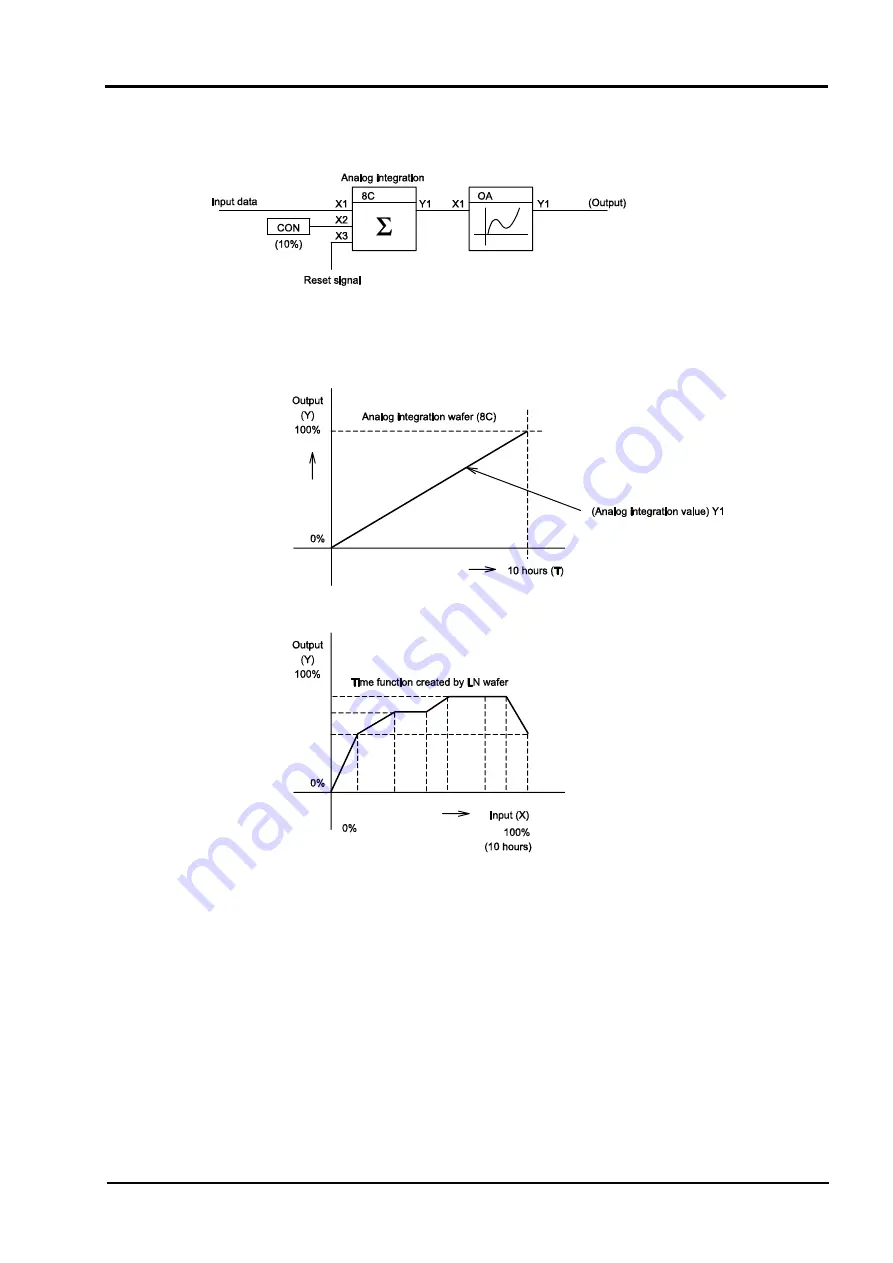
INP-TN512878-E
17
4.6 Method to create time function circuit using analog integration
wafer and N wafer
Figure 4-12
It is possible to create a time function generator by combining an analog integration wafer and a
linearize wafer.
In the example shown above, when a value of 10% is set in constant input (X
2
) of an analog
integration wafer (8C), the analog integration wafer integrates analog value of 100% in 10 hours, and
the input of the linearize wafer changes by 0 to 100% in 10 hours. It is possible to create a time
function of 10 hours by setting a function in the linearize wafer.
Содержание CC-M
Страница 1: ...INP TN512878 E COMPACT CONTROLLER M CC M TYPE PDA3 Application Manual Instruction Manual ...
Страница 9: ......
Страница 42: ......