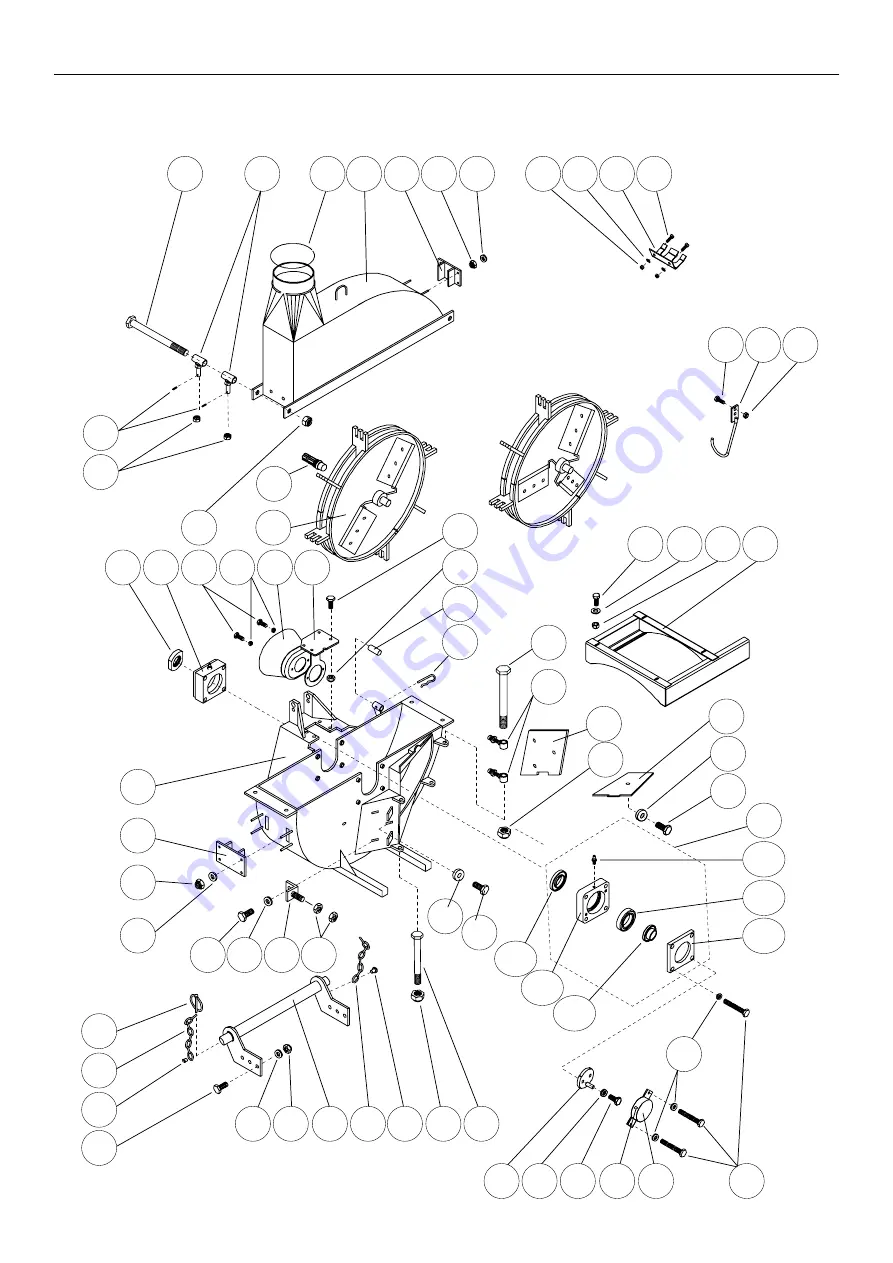
FARMI 260
30
FARMI 260
1
10
9
8
7
6
5
4
3
2
11
20
19
17
16
15
14
13
12
21
30
29
28
27
26
25
24
23
22
31
40
39
38
37
36
35
44
33
32
41
49
48 47
46
45
44
43
42
44
52
20.1
20.2
20.3
20.4
20.5
20.6
56
55
54
53
20
22
23
53
29
6
26
25
29
30
28
44
36
29
33
When ordering spare parts, please indicate the machine’s type and serial number
from the machine plate, spare part’s order number, description and quantity required.
Example. CH260, serial number xxxxxxx, 43298410, knife, 2 pc