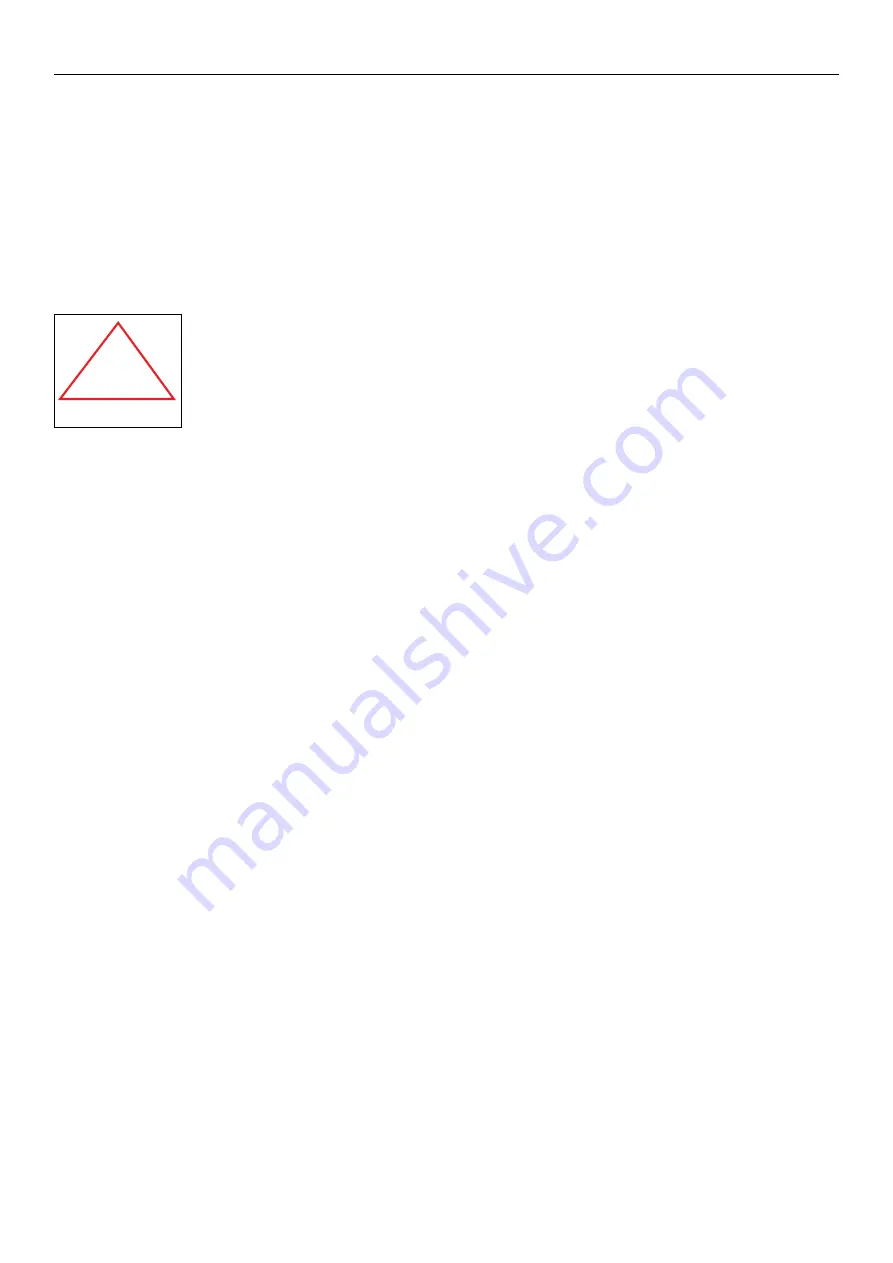
FARMI 260
8
•
When servicing the machine, place it on a level
surface and ensure that it cannot be moved.
•
Observe the service intervals and annual safety
inspections.
•
All spare parts and equipment must fulfill the
manufacturer’s requirements. This can be guaran-
teed by using original parts.
•
Put all safety devices back into place immediately
once servicing or maintenance is complete.
When lifting the machine, check
that the lifting/hoisting equip-
ment is in perfect working order.
Check the weight of the machine
before lifting it. Choose lifting
trajectories so that they do not
cause any danger.
Many countries have specific legislation on lifting,
hoisting cables and hoists. Always comply with local
safety regulations.
OILS AND LUBRICATION
•
Always use the oil types recommended by the
manufacturer. Other types of oil may cause
faults or improper operation of the equipment,
which could lead to serious damage to people or
property.
•
Never mix different liquids or oils.
•
Always follow the manufacturer’s lubrication
instructions.
•
Use control equipment carefully until the hydraulic
oil has had time to reach its operating tempera-
ture.
SAFETY INSTRUCTIONS FOR HYDRAULIC CIRCUITS
1. Work on hydraulic equipment may only be carried
out by professional hydraulic engineers.
2. Be cautious when using the equipment in cold
conditions.
3. Check the machine for leaks. Do not use the
machine if there is a leak from any system. Check all
hydraulic hoses – particularly those which are bent
during use – and replace any that are in poor con-
dition or have leaks. Ensure that all joins are tight
and that the lines are not damaged. Check that all
protective caps and filler caps are closed properly.
Check the hose sheathing for damage.
4. Check that all hose connectors, lengths and
qualities comply with applicable requirements.
When replacing or repairing hoses, use origi-
nal parts or hoses and connectors recommended
by the manufacturer. Check particularly that the
pressure classes of the hoses and connectors are
suitable to the operating pressure levels.
5. Check that all safety devices such as pressure relief val-
ves, etc., are in place and work properly. Familiari-
ze yourself with their use. Safety systems may ne-
ver be bypassed.
6. Check the main hydraulic parts daily, and always
after a fault. Replace any damaged parts imme-
diately.
7. If a component is damaged, clean it before
repairing it. Do not use solvents when cleaning
parts.
8. Do not attempt to carry out repairs that you are
not fully familiar with.
9. Never carry out repairs of the hydraulic circuit
when the system is pressurized. When pressurized,
the oil spray can penetrate the skin and cause mor-
tal danger.
10. Never work below a device or component that is
only being held up by hydraulics. Use separate sup-
ports when carrying our maintenance or repairs.
Do not disconnect cylinders or their valves until the
machine is well supported.
11. Most hydraulic oils do not evaporate easily. Risk
factors include hot oil, spills and oil mist (pressuri-
zed).
12. If oil gets into your eyes, rinse with plenty of water
and contact a doctor.
13. Avoid prolonged or repeated contact with your
skin.
14. If sprays or contact with the skin cannot be
avoided, use protective gloves, goggles and
clothing as necessary. Do not use oily clothing.
15. Avoid discharging hydraulic oil into the
environment, as it can pollute waterways and the
groundwater. If biodegradable oil is to be used,
please contact the manufacturer beforehand and
have the suitability of your equipment for the ope-
ration with biodegradable oil confirmed by him be-
fore such oil is used.
16. Store the oil in sealed containers provided by the
manufacturer. Try to transfer the oil directly from its
container into the tank.
17. If the oil must be passed through other containers, en-
sure that they are completely clean. Caps, funnels,
sieves and filling holes must also be clean.
18. Never store oil outdoors, as water could condense
in it.
19. Always dispose of oil in a suitable container, never
into the environment!
CAUTION!
!