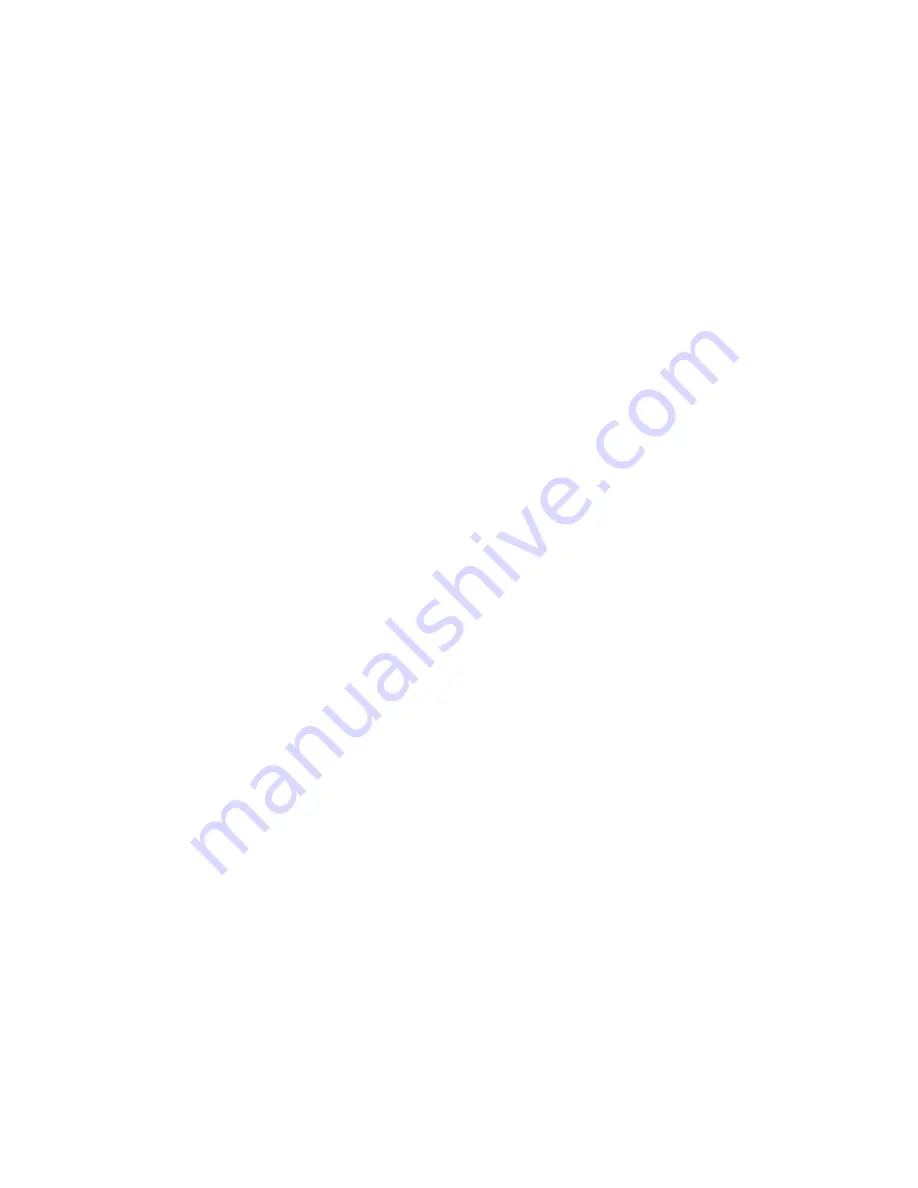
42
The dryer is made of weather resistant construction
and is designed to require a minimum of service; how-
ever, we recommend the following items be checked
before the unit is used each season. Replace any
damaged or questionable parts. THESE CHECKS
WILL HELP ELIMINATE POSSIBLE MINOR FAIL-
URES AND ASSURE DEPENDABLE OPERATION OF
THE EQUIPMENT WHEN IT IS NEEDED.
1. Shut off electrical power. Open main ASC control box
and inspect for any moisture, rodent damage, or accu-
mulated foreign material. Remove all foreign material
present. INSPECT FOR AND TIGHTEN ANY LOOSE
TERMINAL CONNECTIONS. Replace any damaged
or deteriorated wiring. Open Burner Junction Box door
and repeat the inspection and cleaning procedure.
2. Check blower for freedom of rotation. It should also be
inspected for accumulated dirt and grain dust, ESPE-
CIALLY BUILD-UP ON THE WHEEL, as any addition-
al weight can seriously affect the balance and result in
harmful vibrations and shortened bearing life. Keep
inside of the housing free of dirt build-up for efficient fan
performance.
Check that wheel hub set screws are tight before start-
up.
The roller bearing pillow blocks, located on each end of
the blower shaft, should be lubricated at the beginning
and end of each season. When grease is added, use
caution to prevent any dirt from entering the bearings.
The pipe plug or grease relief fitting should be open
when greasing to allow excess grease to flow out. The
pillow blocks should be about 1/3 full, as excess grease
may cause overheating. Use low pressure gun.
Lubricate with the following grease or their equivalent.
Shell - Alvania EP Grease No. 1
Texaco - Molytex Grease No. 1
Mobil - Mobilux EP 1
Blower wheel should be rotated at least once a month
to circulate the grease in the bearings.
Inspect blower drive belt for belt wear, alignment and
proper belt tension. Tension belts as shown in blower
drives chart, Table 1-5.
3. MAKE SURE ALL MOTOR MOUNT BOLTS AND
BLOWER BEARING BOLTS ARE TIGHT.
4. Auger motor bearings should be relubricated periodi-
cally, depending upon operating conditions. Under nor-
mal usage, it is desirable to have the motor cleaned
and checked, and the bearings repacked by an autho-
rized service station every two to three seasons. If the
unit is operated continuously through most of the year,
this service should be performed each year.
NOTE:
If on-site bearing relubrication is to be per-
formed, use CHEVRON SR1-2 high temperature
grease or a compatible equivalent product.
Most fan motors are equipped with grease fittings to
allow the fan motor bearing to be relubricated without
disassembly. Lubricate the fan motor bearings once
each year at the beginning of the drying season by
applying 1/2 fl. oz. (approximately 8 strokes from std.
hand gun) to the front and rear bearing using SHELL
DOLIUM R or CHEVRON SRI-2 motor grease. DO
NOT OVERLUBRICATE!!
To keep motor bearings properly lubricated and dispel
any accumulation of moisture within the windings, the
fan and auger motors should be operated for 15 to 30
minutes each month. The motor manufacturers'
Authorized Service Station list is packed with all units
and should be saved for reference and identification of
service stations.
5. Remove and clean the gas line strainers. Make certain
gas valves are closed and that gas is purged from sys-
tem before attempting disassembly.
6. Inspect burner assembly for loose hardware and tight-
en as required.
7. Inspect ignitor plug and clean the electrodes, if
required. Use an ignition point file to remove carbon
and rust between the electrode surfaces. Spark gap
should be about 3/32 inch.
8. Inspect flame rod for possible damage, accumulation of
ash, or poor connections. The flame rod, ignitor plug,
and burner ground wires must be in good condition.
9. Inspect and manually rotate the top auger paddle
switch assembly. The paddle unit must rotate freely
without any indication of sticking or binding.
10.Inspect all drive belts and chains for proper adjustment
and condition. Readjust tension as required. See Figs.
6-9, 6-10, 6-12, & 6-13.
NOTE: All auger and meter roll end bearings are lifetime
lubricated and do not require service relubrication.
Remove gearbox drive cover and check SCR drive belt
for proper adjustment and condition. Also check oil
level in gearbox. See Fig. 6-13 for oil level plug loca-
tion. For recommended lubricant, see the SPEED
REDUCER GEARBOX subhead under "SCR Drive and
Meter Roll" later in this section.
11. Lubricate the auger drive SPEEDJACK SLEEVE
BEARING FITTINGS as follows:
Relubricate the bottom auger speedjack bearings
every 100 hours of operation using a dependable
brand of MULTI-PURPOSE LITHIUM BASE BEARING
GREASE. See Fig. 6-9.
12.Operate dryer clean-out mechanism and check it for
proper operation. See Fig. 7-1 & 7-2. With clean-out
open, inspect for and remove all dirt and trash accu-
mulation.
NOTE: Do not allow high moisture material to collect
within the auger trough area as it may adversely affect
the metal parts.
13.Inspect entire dryer for loose, worn, or damaged parts.
Include check of auger flighting, meter rolls, and other
internal parts. Check that temperature sensors within
air plenum chamber are secured within the insulated
clamps and do not chafe on other metal parts.
Содержание C-21100B
Страница 22: ...20 ...
Страница 36: ...34 Fig 6 3 LP vaporizer assembly Fig 6 4 ASC control panel ...
Страница 49: ...Fig 8 1 Power circuit 220V 3 PH for C 2130B C 2140B C 2160B only 47 4B0280A TIF ...
Страница 50: ...48 Fig 8 2 Power cirucit 220V Part wind start for C 2175B C 21100 models only 4B0280C TIF ...
Страница 51: ...49 Fig 8 3 Power circuit 440V 3 PH for all C 2100B models 4B0280B TIF ...
Страница 52: ...Fig 8 4 Control circuit all models except part wind start p 1 of 3 50 4B0280D TIF ...
Страница 53: ...Fig 8 4 Control circuit all models except part wind start p 2 of 3 51 4B0280E TIF ...
Страница 55: ...Fig 8 5 Control circuit part wind start models only p 1 of 3 53 4B0280H TIF ...
Страница 56: ...Fig 8 5 Control circuit part wind start models only p 2 of 3 54 4B0280I TIF ...
Страница 58: ...Fig 8 6 Safety circuit portion of control circuit all models 56 4B0280G TIF ...
Страница 65: ......