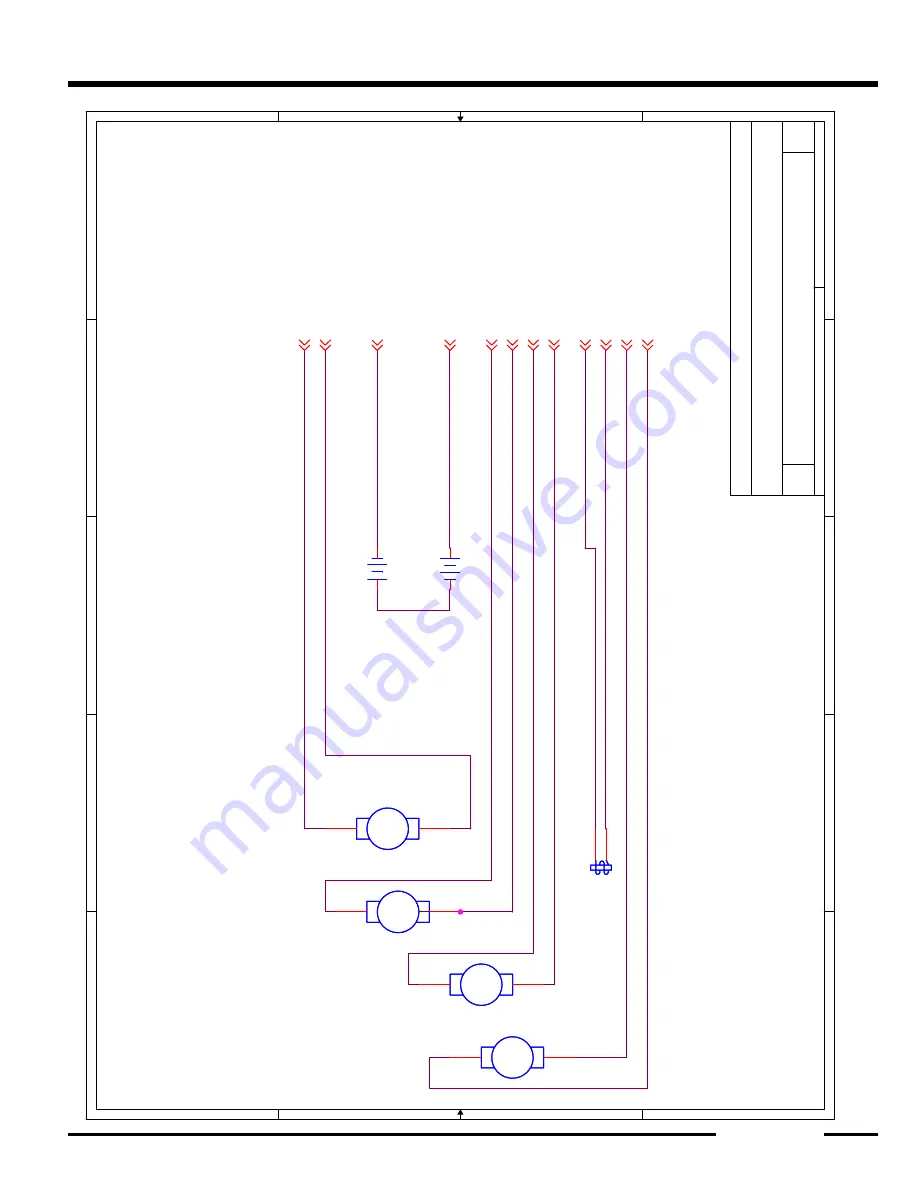
Mini-Mag Service Manual V1.0
12
12-7
ELECTRICAL SYSTEM
5
5
4
4
3
3
2
2
1
1
D
D
C
C
B
B
A
A
NEGATIVE BATTERY CABLE
POSITIVE BATTERY CABLE
BLACK #72
ORANGE #71
ORANGE #71
BLACK #72
10 Ga. BLACK
10 Ga. BLACK
10 Ga. BLACK
10 Ga. RED
10 Ga. RED
10 Ga. RED
WHITE #131
WHITE #131
WHITE #131
PINK #130
PINK #130
PINK #130
10 Ga. BLACK
10 Ga. BLACK
10 Ga. BLACK
10 Ga. RED
10 Ga. RED
RED #183
RED #183
RED #183
BLACK #184
BLACK #184
BLACK #184
TO CENTRAL COMMAND
TO CENTRAL COMMAND
TO 12 PIN MOLEX CONNECTOR
TO 12 PIN MOLEX CONNECTOR
TO GROUND STUD IN CENTRAL COMMAND
TO BRUSH MOTOR CIRCUIT BREAKER
TO 12 PIN MOLEX CONNECTOR
TO 12 PIN MOLEX CONNECTOR
TO GROUND STUD IN CENTRAL COMMAND
TO VACUUM MOTOR CIRCUIT BREAKER
TO 12 PIN MOLEX CONNECTOR
TO 12 PIN MOLEX CONNECTOR
Title
Size
Document Number
Rev
Date:
Sheet
of
000-000
1.0
MiniMAG - Brush Assist - Body Wiring
A
1
1
Tuesday, December 05, 2006
Title
Size
Document Number
Rev
Date:
Sheet
of
000-000
1.0
MiniMAG - Brush Assist - Body Wiring
A
1
1
Tuesday, December 05, 2006
Title
Size
Document Number
Rev
Date:
Sheet
of
000-000
1.0
MiniMAG - Brush Assist - Body Wiring
A
1
1
Tuesday, December 05, 2006
BT3
BATTERY 12 VOLT
BT3
BATTERY 12 VOLT
M1
-
+
MOTOR, VACUUM
M1
-
+
MOTOR, VACUUM
1
2
BT4
BATTERY 12 VOLT
BT4
BATTERY 12 VOLT
M4
-
+
MG4
MOTOR, BRUSH DRIVE
M4
-
+
MG4
MOTOR, BRUSH DRIVE
1
2
M2
-
+
MOTOR, BRUSH ACCTUATOR
M2
-
+
MOTOR, BRUSH ACCTUATOR
1
2
SOLUTION, SOLENOIDSOLUTION, SOLENOID
1 2
M3
-
+
MOTOR, SPRAY JET
M3
-
+
MOTOR, SPRAY JET
1
2
Содержание MINI-MAG SERIES
Страница 2: ......
Страница 12: ...Mini Mag Service Manual V1 0 TOC toc 1 6 TABLE OF CONTENTS BLANK THIS PAGE WAS INTENTIONALLY LEFT BLANK ...
Страница 14: ...Mini Mag Service Manual V1 0 1 1 2 MAINTENANCE ...
Страница 15: ...Mini Mag Service Manual V1 0 1 1 3 MAINTENANCE ...
Страница 16: ...Mini Mag Service Manual V1 0 1 1 4 MAINTENANCE BLANK THIS PAGE WAS INTENTIONALLY LEFT BLANK ...
Страница 22: ...Mini Mag Service Manual V1 0 2 2 6 MACHINE INTRODUCTION BLANK THIS PAGE WAS INTENTIONALLY LEFT BLANK ...
Страница 28: ...Mini Mag Service Manual V1 0 3 3 6 SQUEEGEE SYSTEM SQUEEGEE ADJUSTMENT EXAMPLES ...
Страница 30: ...Mini Mag Service Manual V1 0 3 3 8 SQUEEGEE SYSTEM ...
Страница 42: ...Magnum Service Manual V1 0 6 6 4 SOLUTION SYSTEM BLANK THIS PAGE WAS INTENTIONALLY LEFT BLANK ...
Страница 48: ...Mini Mag Service Manual V1 0 7 7 6 BRUSH DRIVE SYSTEM BLANK THIS PAGE WAS INTENTIONALLY LEFT BLANK ...
Страница 54: ...Mini Mag Service Manual V1 0 8 8 6 BRUSH LIFT SYSTEM BLANK THIS PAGE WAS INTENTIONALLY LEFT BLANK ...
Страница 56: ...Mini Mag Service Manual V1 0 9 9 2 TRACTION DRIVE SYSTEM BLANK THIS PAGE WAS INTENTIONALLY LEFT BLANK ...
Страница 58: ...Mini Mag Service Manual V1 0 10 10 2 CHASSIS SYSTEM BLANK THIS PAGE WAS INTENTIONALLY LEFT BLANK ...
Страница 78: ...Mini Mag Service Manual V1 0 12 12 12 ELECTRICAL SYSTEM BLANK THIS PAGE WAS INTENTIONALLY LEFT BLANK ...