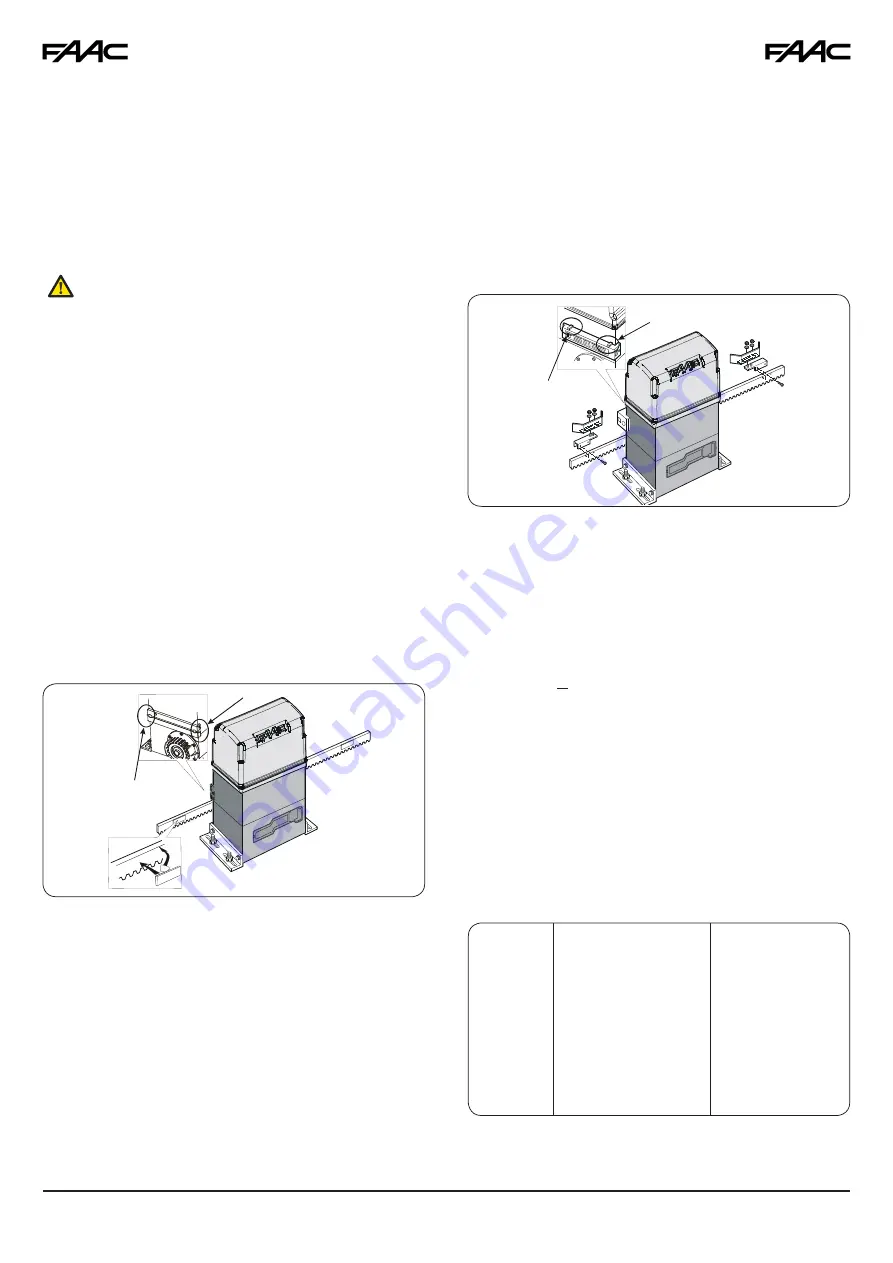
17
2
1
FC2
FC1
Fig. 35
FC2
FC1
Fig. 36
6.3.2.
Inductive Limit-Switch
The inductive limit-switch detects the travel of the two steel
plates fitted on the top of the rack or the chain.
Procedure for correct positioning of the two supplied steel
plates:
1. Assemble the limit-switch by centering the plate with
respect to the threaded pins of the support (Fig. 36).
2. Check that the operator is in manual operating mode
(see Section 8).
3. Manually open the gate to within 3/4 to 2 inches of the
mechanical stop limit.
Attention: Due to the powerful magnetic fields produced
by the supplied magnets, do not place magnetic storage
devices (credit cards, magnetic tapes, floppy disks, etc) or
sensitive electronic equipment (watches, CRT monitors, LCD
screens, etc.) near the magnets.
Notes on Magnet Positioning
• To ensure correct operation, allow at least 3/4 inch from
the mechanical stop limit in the gate stop position. Carry
out this check after determining the values of the pre-
and post-limit switch decelerations (see Section 5.5.2.)
and after running at least one complete cycle of the
automated system.
• The distance between the limit-switch and magnets
must be from 1/4 to 1/2 inch.
• Magnets should be fitted on the rack and not on the
screws. If necessary, position the magnet at the side of
the screw and adjust decelerations (see Section 5.5.2) in
order to obtain the correct stop point.
Notes on Plate Positioning
• To ensure correct operation, allow at least 3/4 inch from
the mechanical stop limit in the gate stop position. Carry
out this check after determining the values of the pre-
and post-limit switch decelerations (see Section 5.5.2.)
and after running at least one complete cycle of the
automated system.
• The distance between the limit-switch and the plates
must be < 3/16 inch.
LEDS
ON
OFF
OP-A
Command activated
Command inactive
OP-B
Command activated
Command inactive
FC1
Limit-switch free
Limit-switch engaged
FC2
Limit-switch free
Limit-switch engaged
FSW OP
Safety devices disengaged
Safety devices engaged
FSW CL
Safety devices disengaged
Safety devices engaged
STOP
Command inactive
Command activated
SAFE
Safety devices disengaged
Safety devices engaged
ENC
Flashes while the motor rotates
6.4.
INPUTS CHECK
The table below shows the status of the LEDs in relation to to
the status of the inputs.
Note the following:
L
ed
ON
= closed contact
L
ed
OFF
= open contact
Check the status of the LEDs as per the following table.
Note
: The status of the LEDs while the gate is closed are shown
in bold. If opening direction is to the left, the status of LEDS FC1
and FC2 is reversed.
Table 2: Operation of the Signalling Status LEDs
8. Check that the gate stops approximately 3/4 to 2 inches
from its mechanical stop point. If necessary, correct the
position of the magnets and check that the stop point is
correct.
9. Mark the position of the magnets on the rack, and remo-
ve them.
10. Clean the rack on its fitting points, remove the film on
the adhesive parts of the magnets (Fig. 41 Ref. 1) and re-
position the magnets with the adhesive strip in contact
with the rack (Fig. 35 Ref. 2).
4. Allow the plate to move on the rack in opening direction
until the relevant LED goes off (Figs. 22 and 36); next,
move the plate forward an additional 1 3/4 inches and
secure it to the rack by tightening the screws.
5. Manually close the gate to within 3/4 to 2 inches of the
mechanical stop limit.
6. Allow the plate to move on the rack in closing direction
until the relevant LED goes off (Figs. 22 and 36); next,
move the plate forward by an additional 1 3/4 inches
and secure it to the rack by tightening the screws.