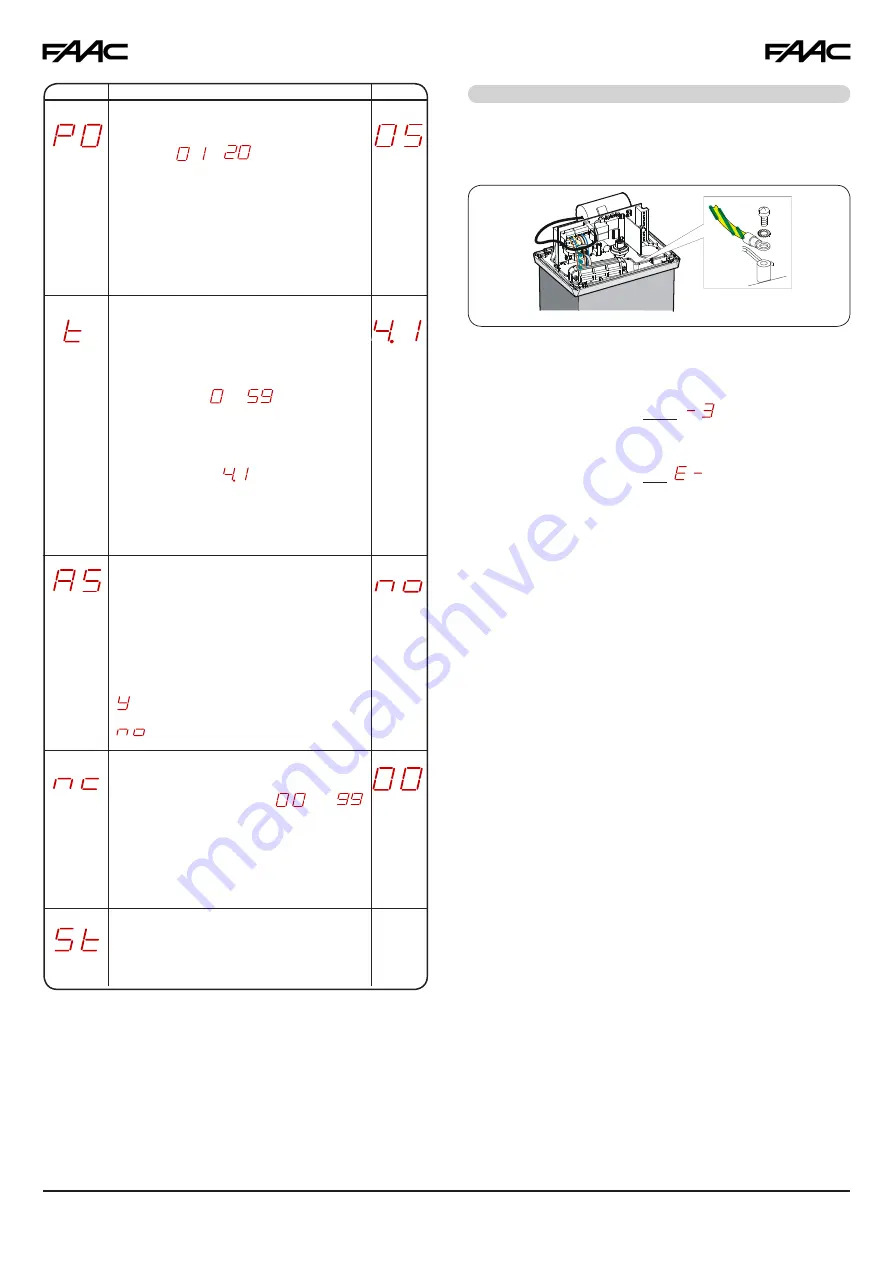
16
6. START-UP
Fig. 34
6.2.
OPENING - CLOSING DIRECTIONS
Power up the system and set the opening direction on the
board (see Section 5.5.1).
I
f opening direction is to the RIGHT
(
):
OPENING limit-switch LED =
FC1
CLOSING limit-switch LED =
FC2
If opening direction is to the LEFT
(
):
OPENING limit-switch LED =
FC2
CLOSING limit-switch LED =
FC1
Note: for RF chain applications the wires on Mot1 and Mot2
(See Fig. 23) need to be reversed.
6.1.
ELECTRIC CONNECTIONS
Make all electrical connections to the board as described in
Section 5, including grounding the operator (Fig. 34).
6.3.
DETERMINING STOP POINTS AT TRAVEL
LIMIT
The 844 operator has a limit sensor switch which, by detecting
the transit of a reference applied to the rack, commands
the motor to stop. The device can be magnetic (Fig. 41) or
inductive (Fig. 42).
6.3.1.
Magnetic Limit-Switch (MLS)
The MLS limit-switch detects the transit of two magnets fitted
on the side of the rack facing the operator.
Procedure for correct positioning of the two supplied magnets:
1. Check that the operator is in manual mode (see Sec.8).
2. Manually open the gate to within 3/4 to 2 inches of the
travel limit mechanical stop.
3. Fit the magnet (without removing the protective film from
the adhesive side) on the side of the rack facing the
operator, aligning the upper edges. Slide the magnet on
the rack in opening direction until the relevant LED turns
on (Fig. 22 and 41), then move the magnet forward an
additional 1 3/4 inches.
4. Manually close the gate to within 3/4 to 2 inches of the
travel limit mechanical stop.
5. Fit the magnet (without removing the protective film from
the adhesive side) on the side of the rack facing the
operator, aligning the upper edges. Slide the magnet on
the rack in closing direction until the relevant LED turns
on (Fig. 22 and 41), then move the magnet forward an
additional 1 3/4 inches.
6. Move the gate to its halfway travel point and relock the
system (see Sec. 9).
7. Find out the desired pre- and post-limit-switch decelera-
tion values (see Section 5.5.2) and run the automated
system for at least one complete cycle.
Display
Function
Default
Note 1
: To reset the programming default settings, check
that the edge input is closed (SAFE LED ON), and
simultaneously press keys
+, -
and
F
, holding them
down for 5 seconds.
Note 2
: Modifications of programming parameters take
effect immediately, whereas changes are saved to
memory only after you exit programming and return
to normal gate status viewing. If the equipment is
powered down before returning to status viewing,
any modifications will be lost.
ASSISTANCE REQUEST (combined with
next function):
If activated, at the end of countdown (see the
next function: "Cycle Programming") it effects
2 sec. (in addition to the value already set
with the PF function) of pre-flashing at every
Open pulse (job request). It can be useful to
set scheduled maintenance jobs.
= Active
= Disabled
WORK TIME (time-out):
It is advisable to set a value of 5 to 10 seconds
over the time taken by the gate to travel from
the closing limit-switch to the opening limit-
switch and vice versa.
Adjustable from
to
sec. in one-se-
cond steps.
Subsequently, display changes to minutes and
tens of seconds (separated by a point) and
time is adjusted in 10 second steps, up to a
maximum value of
minutes.
Attention: the set value will not exactly
match the motor's maximum operating
time if decelerations are used.
PARTIAL OPENING:
You can adjust the width of partial leaf ope-
ning. from
to
.
For example, with pinion Z20, partial opening
can vary from 2' to 13'.
CYCLE PROGRAMMING:
To set countdown of system operation cycles.
Settable (in thousands) from
to
thousand cycles.
The displayed value is updated as cycles
proceed.
GATE STATUS:
Exit from programming, save data and
return to viewing gate status (see Section
5.5.1.).