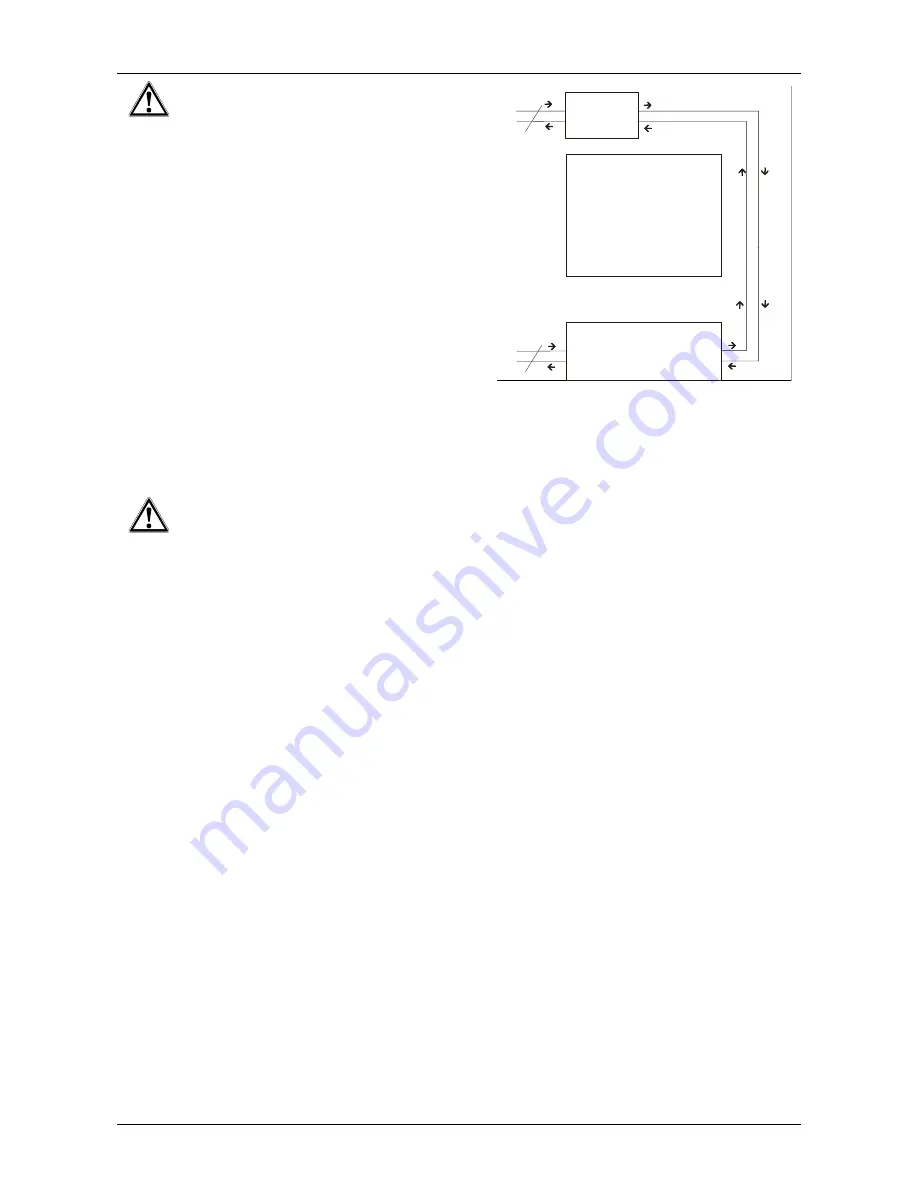
5 Commissioning
5/6
If a TIG torch and MIG/MAG torch are to be
connected at the same time (e.g. frequent
changing between the processes)
the more powerful cooling unit COOL 71U41
should be used.
Under certain circumstances, limitations in
cooling output may arise despite the more
powerful cooling unit;
e.g. excessively long intermediate hose
packages or torches, special torches, etc.
TRITON 400/500
COOL 71U41
blue
blue
blue
blue
red
red
red
TIG torch
MIG/MAG-
torch
ZWIPA
red
WF unit
Fig. 5/8
5.9.2.1 Supply to the wire feed unit
•
Insert the welding current plug of the WF unit in the socket (I2 "+") (option) and lock by turning
to the right.
For special MIG/MAG applications such as welding cored wires for example, the WF unit
welding current plug is plugged into the "-" socket (H2) (option) and locked by turning to the
right.
•
Insert the torch control lead plug (7-pole) into the connection socket (G2) and lock (rear of
machine).
•
Please see the wire feed unit operating instructions for further information.
5.9.2.2 Workpiece
lead
•
Insert cable plug of the workpiece lead into the welding current socket (C1 "+" or E1 "-"
depending on the application
)
and lock by turning to the right.
5.10 Cooling unit function specification
A function test of the cooling module is performed after the welding machine is switched on.
The coolant pump and the fan are switched on.
When the pump is running, the coolant level is sufficient and a sufficient hydrostatic pressure has
built up, the cooling module is switched off after 2 seconds.
If the level is not sufficient a coolant error is reported and the pump runs for a maximum of 30
seconds so that the operator can top up the coolant.
The cooling unit is switched on at the start of the TIG or MIG/MAG welding process.
After the welding process has stopped, the water pump and fan continue to run for a further 5min
and then switch off.
5.10.1 Coolant
error
If there is no coolant pressure for longer than 2.5 sec during the welding operation e.g. because of
a lack of coolant, pump failure or a burst or leaking hose:
•
an error message is issued (LED see fig. 3/1, pos. K1)
•
and the welding process is ended in a controlled manner
(coolant pump and power unit of the welding machine are switched off).
With renewed starting of the welding process, the coolant error is reset and the cooling module
switched on. If still no coolant pressure has built up after 2.5 sec, the cooling module is switched
off, the LED coolant level low (see fig. 3/1, pos. K1) lights up and the welding process is ended in a
controlled manner.
Содержание TRITON 260 DC
Страница 57: ...10 Circuit diagram 10 1 10 1 TRITON 260 Circuit diagrams are also in the machine...
Страница 58: ...10 Circuit diagram 10 2...
Страница 59: ...10 Circuit diagram 10 3 10 2 TRITON 360 500 Circuit diagrams are also in the machine...
Страница 60: ...10 Circuit diagram 10 4...
Страница 61: ...10 Circuit diagram 10 5...