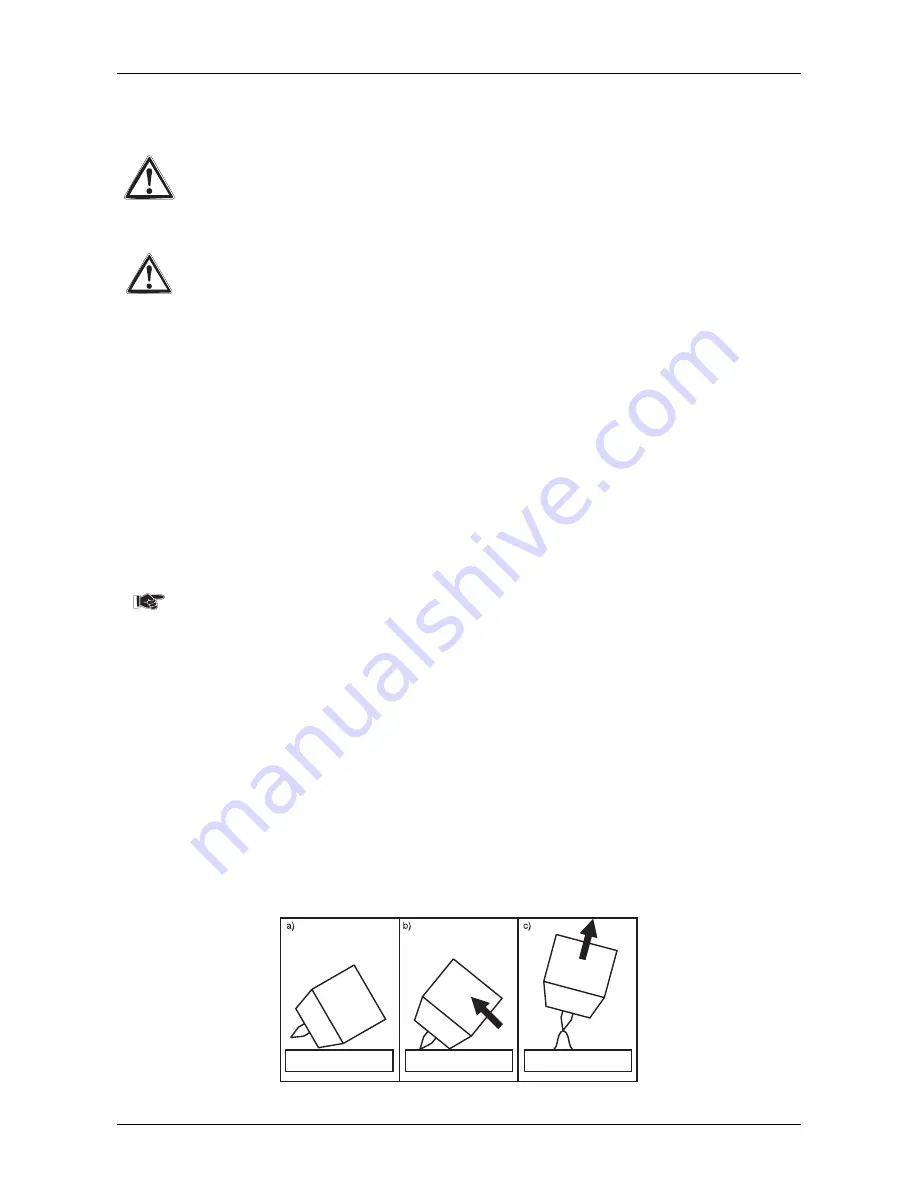
5 Commissioning
5/4
Antistick:
If the stick electrode sticks in spite of the arcforcing device, the machine automatically switches
over to the minimum current within about 1 sec, so that overheating of the electrode is prevented. If
the antistick device has been triggered, check the welding current setting and correct if necessary.
After welding, place electrode holder onto insulated base,
switch off welding machine.
Electrode is hot.
5.8 TIG
welding
Follow the safety instructions on the opening pages entitled "For your safety".
If welding is carried out alternately using TIG or MMA and if both a welding torch and an
electrode holder are connected to the machine, the open-circuit/welding voltage is applied
simultaneously to both.
The torch and the electrode holder should therefore always be placed on an insulated
surface before starting work and during breaks.
We can only guarantee the perfect functioning of our machines when used with our range
of welding torches.
TIG welding torches with shielded torch trigger control leads should not be connected
(see torch operating instructions).
•
Fit tungsten electrode and gas nozzle onto the welding torch
(take into account current load, see torch operating instructions).
•
Connect welding torch and workpiece lead.
•
Fix workpiece lead with good electrical contact to the workpiece.
•
Set the welding process “TIG welding” using the key button. (chap. 3.1; C1)
•
Switch on machine at the main switch (G1
)
.
•
Open gas cylinder valve and set recommended gas quantity on the pressure reducer.
Rule of thumb for gas flow rate:
Diameter of gas nozzle in mm corresponds to gas flow in l/min.
Example: 7 mm gas nozzle corresponds to 7 l/min gas flow.
5.8.1
TIG welding with liftarc ignition
•
Select liftarc ignition type using changeover switch (H1).
•
Select operating mode (non-latched / latched) using the key button (chap. 3, D1).
The functional sequences for TIG non-latched and TIG latched are described in chap. 5.12.3.
•
Carry out welding (see fig. 5/2)
The arc is ignited on contact with the workpiece:
•
Activate torch trigger in accordance with the operating mode selected.
•
The torch gas nozzle must be placed with its rim on the ignition point to give a gap of approx. 2-
3 mm between the electrode tip and the workpiece (a).
•
Carefully touch the workpiece with tungsten electrode tip. Press torch trigger in accordance with
the operating mode selected.
•
The arc ignites when the torch is lifted off and swivelled to its normal position (c).
Fig. 5/2: Liftarc