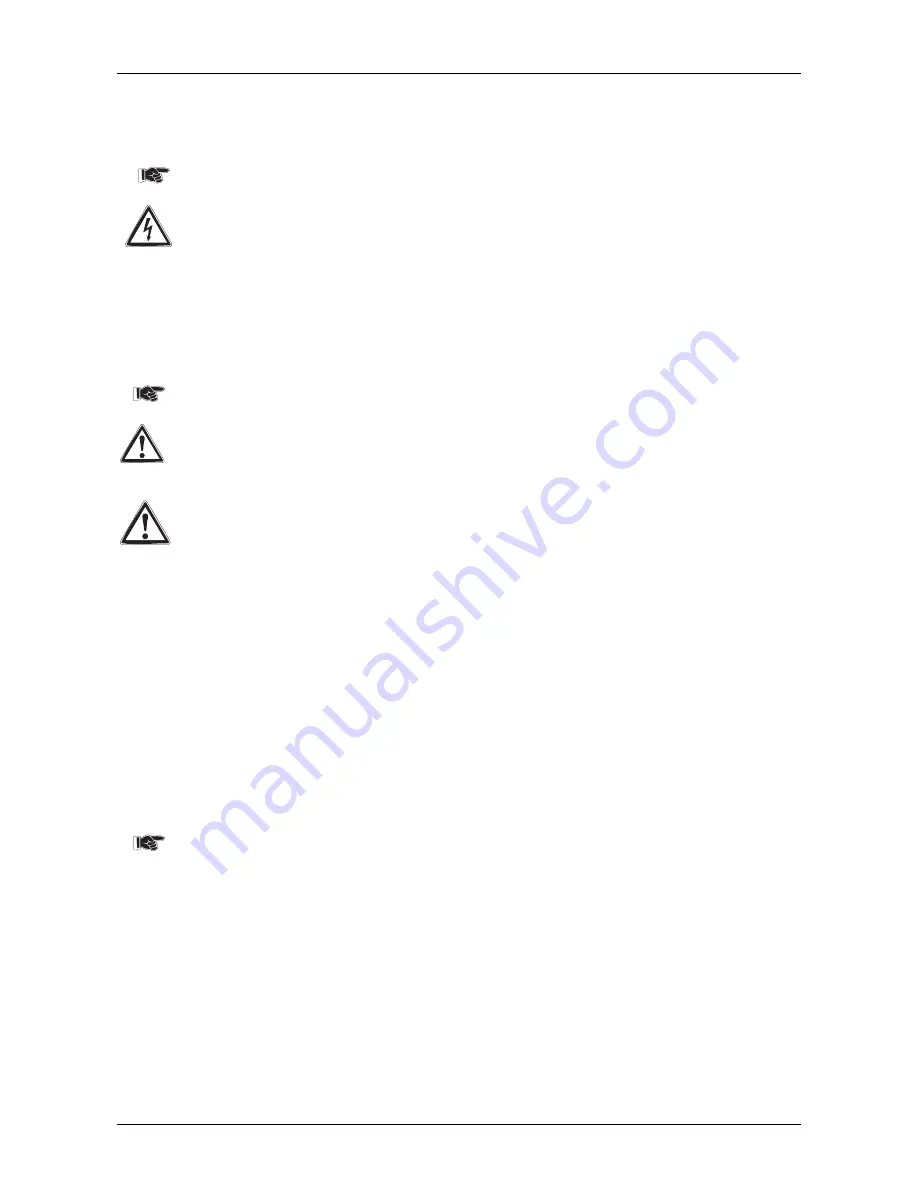
5 Commissioning
5/2
5.5.1 Workpiece
lead
•
Insert cable plug of the workpiece lead and lock by turning to the right.
TIG welding:
Welding current socket “+” (C1)
MMA welding:
Welding current socket “+” (C1)
The polarity depends on the instructions from the electrode manufacturer given on the
electrode packaging.
Remove paint, rust and dirt from clamping and welding areas with a wire brush. The
workpiece clamp must be mounted near the welding point and must be fixed in such a way
that it cannot come loose of its own accord.
Structural parts, pipes, rails etc. may not be used as return leads for the welding current
unless they are the workpiece themselves.
A perfect current connection must be ensured for welding benches and appliances.
5.5.2 Electrode
holder
•
Insert cable plug of the electrode holder into the welding current socket ( “-” D1
)
and lock by
turning to the right.
The polarity depends on the instructions from the electrode manufacturer given on the
electrode packaging.
Clamp stick electrode into electrode holder. Caution: Risk of injury from crushing!
Always put down stick electrode holder in an insulated position.
5.5.3
TIG welding torch
We can only guarantee the perfect functioning of our machines when used with our range of
welding torches.
TIG welding torches with shielded torch trigger control leads should not be connected (see
torch operating instructions).
Always put down welding torch when insulated.
Prepare welding torch according to the welding task in hand (see operating instructions for
the torch).
•
Fit tungsten electrode and gas nozzle onto the welding torch
(observe current load, see torch operating instructions).
•
Insert the welding current plug in socket "-" (D1) and lock by turning to the right.
•
Insert the torch trigger plug in the socket (B1) and tighten.
•
Screw shielding gas connection of the welding torch tightly onto the connection nipple G¼ (A1
)
(welding current potential "-").
•
For water cooled torches (optional):
Engage the rapid-action closure nipple of the TIG torch in the rapid-action closure coupling for
the coolant supply (blue) and return (red) lines of the cooling module.
5.5.4
Shielding gas supply (shielding gas cylinder to the welding machine)
No impurities must be allowed to enter the shielding gas supply, as these would otherwise
cause blockages in the shielding gas supply. Before connecting the pressure reducer to
the gas cylinder, open the cylinder valve briefly to blow out any dirt.
All shielding gas connections must be gastight.
•
Place shielding gas cylinder in the retainer provided for it and secure with chains.
•
Before connecting the pressure reducer to the gas cylinder, open the cylinder valve briefly to
blow out any dirt present.
Connection:
•
Mount the pressure reducer on the gas cylinder valve.
•
Screw the gas hose gastight to the pressure reducer and connecting nipple G ¼" on the rear of
the welding machine (F1).
Adjustment:
•
Switch on machine at the main switch (G1
)
.
•
Select the TIG welding process using the key button (chap. 3, C1).